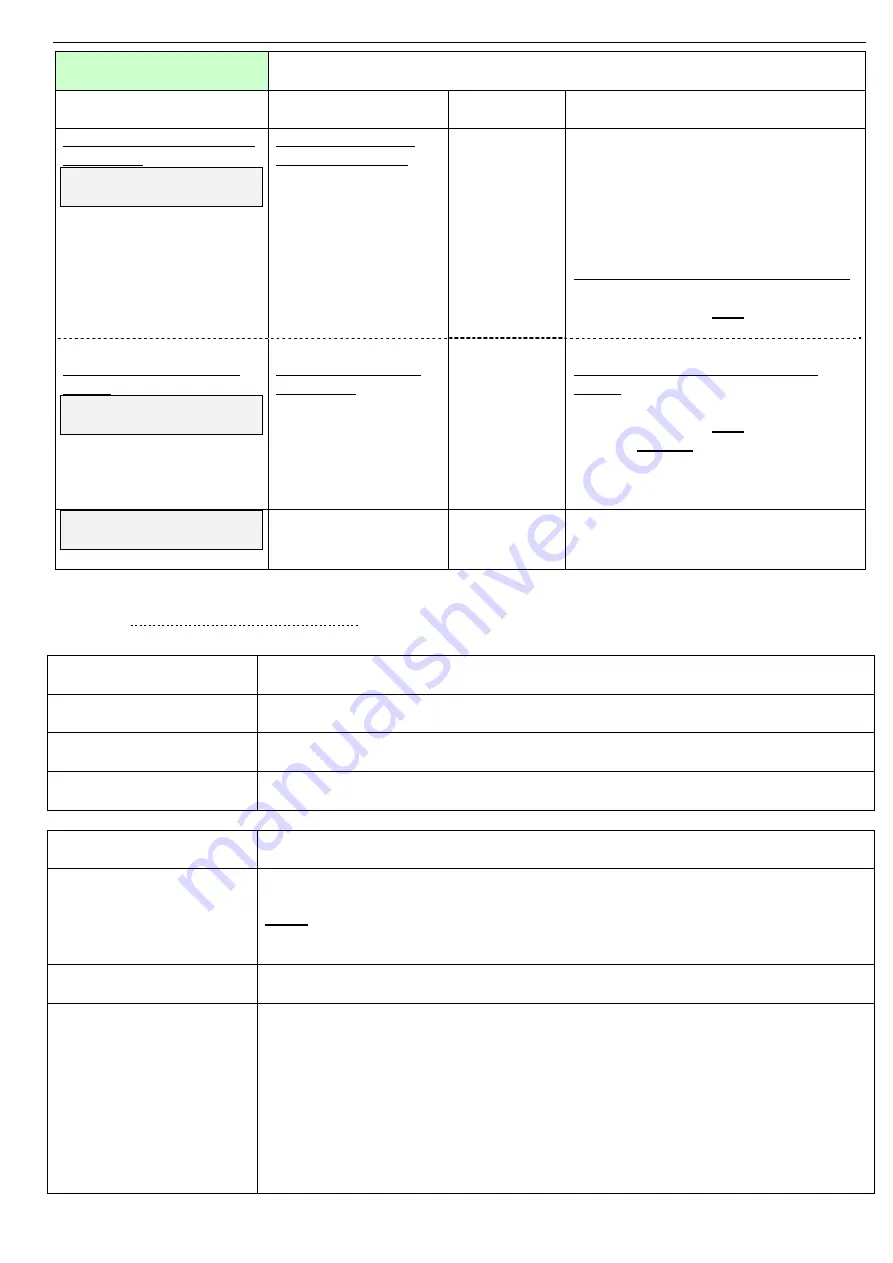
84 • Control Keypad
_____________________________________________________________________________________________
I/O PROGRAMMING
PARAMETERS
Displays in MAXIMIZED MODE only
6.5.1 page 56 for changing mode)
Display and Default
Values
Range Description
Remarks
All RVS-DN except 1000V
and 1200V
AN. OUT PARAMETER
I, 0...200% OF FLA
All RVS-DN except
1000V and 1200V
I, 0...200% OF FLA
Sets
ANALOG
OUTPUT
mode of
operation.
Available when the analog card is
installed.
The dip switch settings on the analog
card define full scale as either 20mA
or 10V. Refer to section
59 for more details.
All RVS-DN except 1000V and 1200V
The full scale of the analog card is
related to 200% of
FLA
(2x <
rated
motor current
>).
For RVS-DN 1000V and
1200V
ANALOG OUTPUT
NORMAL
For RVS-DN 1000V
and 1200V
NORMAL/INVERTED
For RVS-DN 1000V and RVS-DN
1200V
The full scale of the analog card is
related to 200% of
FLC
(2x <
rated
RVS-DN current
>).
When INVERTED is set the full scale
relates to 0 current and 0mA, 0V or
4mA relates to 200% FLC.
STORE ENABLE
I/O PROG.PARAMETERS
Same as STORE ENABLE
MAIN PARAMETERS on page 71
7.7.8.1
Terminal 7 and 8 Programming
Input Terminal 7
Programmed Function
Description
RESET (default setting)
Input terminal 7 is used as RESET to reset all RVS-DN faults.
The RESET command will take effect only if the start command is removed.
SLOW SPEED
While input terminal 7 is on, the motor will start slow speed forward.
Refer to section
7.7.6 on page 80 and section
ENERGY SAVER
While input terminal 7 is on, the motor will operate in the ENERGY SAVER mode.
Refer to section
Input Terminal 8
Programmed Function
Description
DUAL ADJUSTMENT
(default setting)
Input terminal 8 is used to start and stop from the DUAL ADJUSTMENT
PARAMETERS page. Refer to section
Note:
When dip switch #3 is on, DUAL ADJUSTMENT parameters will operate the RVS-
DN with D.ADJ.:GENERATOR PARAMETERS. Refer to section
RESET
Input terminal 8 is used as RESET to reset all RVS-DN faults.
The RESET command will take affect only if the start command is removed.
SLOW SPD REVERSE
In order to operate in SLOW SPEED REVERSE terminal 7 must be programmed
as SLOW SPEED and the control input voltage must be connected to terminal 7
as well.
You can give the reverse command before the motor is started or during operation
at SLOW SPEED.
Connecting control voltage to terminal 8 before the motor is started, starts the
motor in reverse direction.
Connecting the control voltage while the motor is running at SLOW SPEED stops
the motor for 0.6 – 2 sec (according to motor size) before it reverses its direction.
Refer to section
7.7.6 on page 80 and section