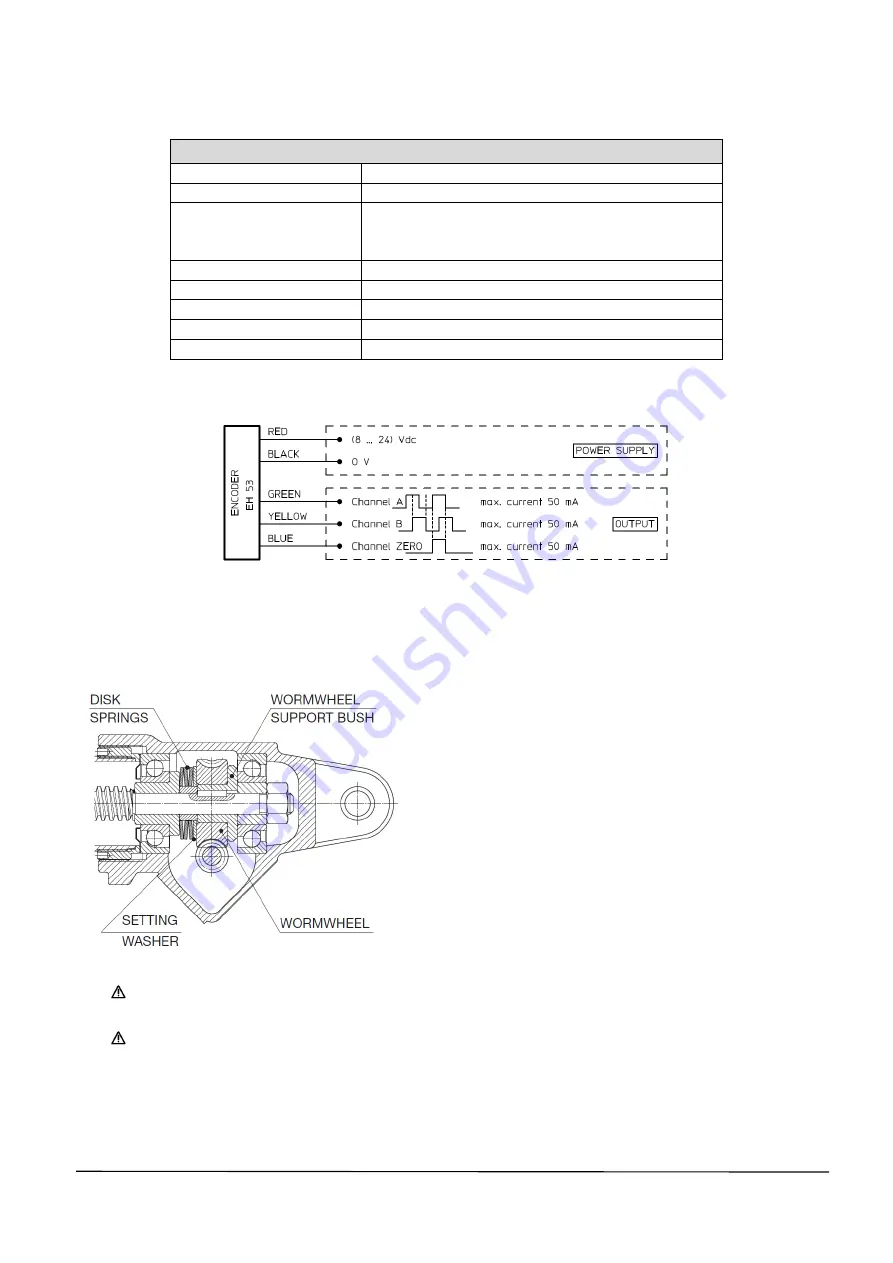
15
6.6
Rotary encoder EH53
Encoder EH53 – TECHNICAL FEATURES
Transducer type
Optical encoder, incremental, bi-directional
Resolution
100 or 500 pulses per revolution
Output
PUSH-PULL
2 channels (A and B, phase difference 90°)
channel ZERO
Input voltage
8 ÷ 24 V DC
No-load current
100 mA
Max commutable current
50 mA
Cable length
0.5 m
Enclosure rating
IP 54
The rotary encoder ENC.4 must be connected to the electric control circuit as shown in the following
WIRING DIAGRAM:
6.7
Safety clutch FS
The safety clutch is a device able to protect the actuator and the machinery where it is installed from dynamic
overload during the linear travel and from incorrect use which could bring the actuator to the mechanical
stop. This device is a torque limiter on the worm wheel.
The torque limiter clutch is preloaded during
assembly.
The preload is fixed and related to the ratio and the
performances of each actuator as stated on the
performance tables in the catalogue.
On request, a different preload can be set to achieve
different performance.
If an overload is applied on the actuator, the safety
clutch starts slipping and the push rod stops while the
motor is still running. When the overload decreases up to
the rated load value or less, the safety clutch stops slipping
and the push rod starts travelling again.
The safety clutch FS is not intended to be used as a load limiter, but only to protect the actuator and
the machinery where it is installed.
DO NOT USE THE SAFETY CLUTCH AS A STROKE END CONTROL DEVICE! If it is frequently activated it
rapidly wears, the preload is reduced and consequently also the actuator load performance is lower.