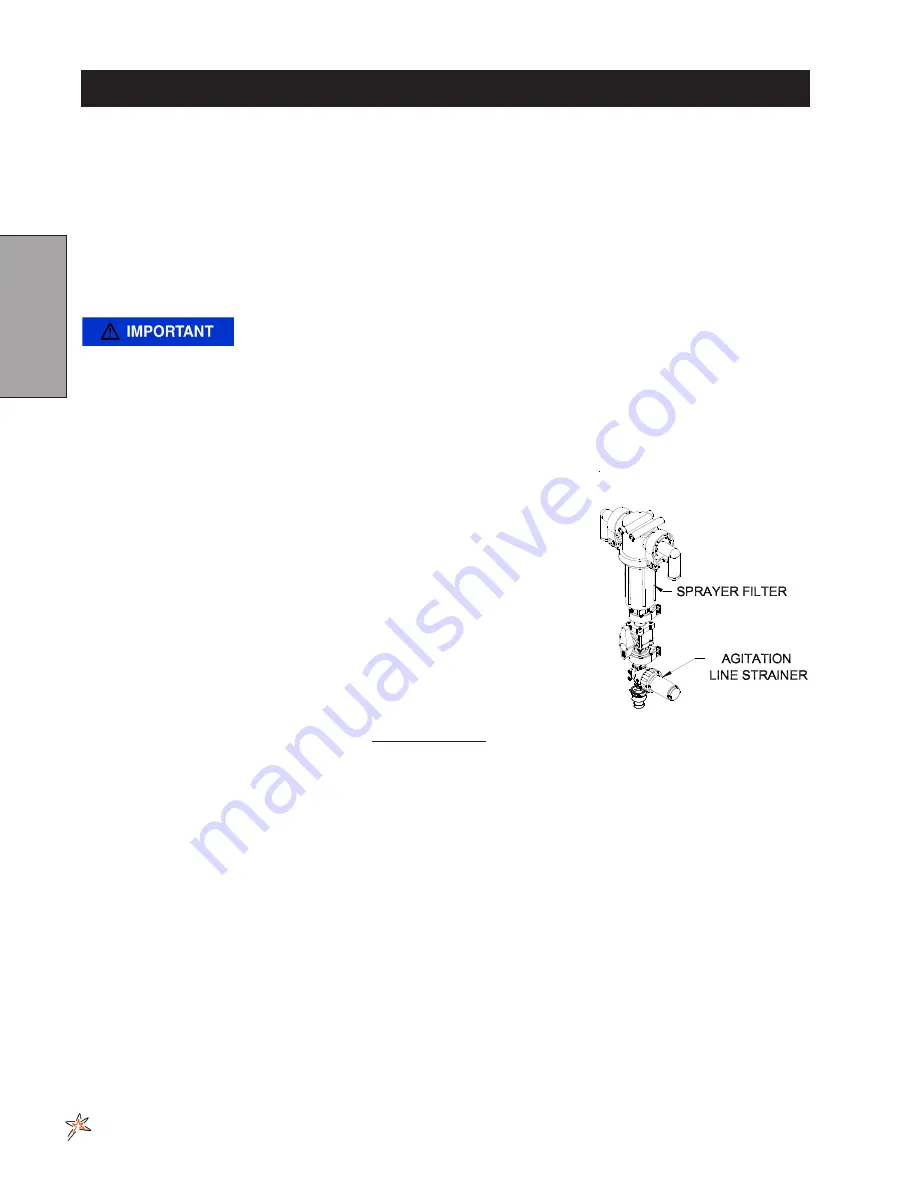
14
Operation
PARTS MANUALS AVAILABLE ONLINE AT smithco.com
SPRAYER CLEANING
One of the most common causes for faulty-pump performance is corrosion inside the pump. Flush the pump and
entire system with a solution that will chemically neutralize the liquid pumped. Mix according to manufacturer’s
directions. This will dissolve most residue remaining in the pump, leaving the inside of the pump clean for the next
use.
TO PREVENT CORROSION
After cleaning the pump as directed, flush it with a permanent type automobile antifreeze (Prestone, Zerex, etc.)
containing a rust inhibitor. Use a 50% solution that is, half antifreeze and half water. Then coat the interior of the
pump with a substance which will prevent corrosion such as Fluid Film or WD40. If unit will not be used for an ex-
tended period of time, disconnect hoses into and out of the pump, seal openings to the pump with caps or tape.
Dispose of fluids according to all federal, state and local regulations.
All chemicals and chemical residue must be removed after each use. Dispose of
fluids and residue according to all federal, state and local regulations.
SPRAYER CLEANING
Empty tank and clean unit thoroughly after each use following these instructions:
1. Turn off 3-way valve and rinse inside of tank thoroughly with clean water, remove cap from valve to drain.
2. Fill tank ten percent full with clean water, Turn 3-way valve on and start pump and discharge water through
spray hose or spray boom (with nozzles removed), until empty.
3. Turn off 3-way valve again and rinse tank interior thoroughly. Remove
cap from 3-way valve to drain.
4. Rinse exterior of sprayer thoroughly with clean water.
5. This sprayer is equipped with a self cleaning strainer. The strainer uses
the excess pump flow to bypass clogging particles back to the spray
tank. There is a gap between the tapered inner cylinder and the screen
face that causes the inlet fluid to flow at a high velocity past the screen
face providing a continuous wash down of particles. For this wash down
to occur a minimum of +GPM/23 l/min is required through the bypass
line.
AGITATION LINE STRAINER CLEANING
Agitation line strainer is located below the sprayer filter. This strainer catches
impurities that go to the turbo-jet agitation system in the spray tank. It has a
quick disconnect pin on it to remove the bowl.
After EVERY use
, remove bowl
and clean screen. Replace screen as needed. We recommend a 50 Mesh
screen.
MANUAL HOSE REEL
Located at the back of the Spray Star on top of the tank. Open the ball valve located near the manifold valve to
allow fluid to flow into the hose reel. Place the lockout pin in the unlocked position by pulling and turning it half a
turn, this will allow you to pull out additional hose or to use the handle and wind up the hose. To prevent movement
during transport or storage place the lockout pin in the locked position.
ELECTRIC HOSE REEL
Located at the back of the Spray Star on top of the tank. Open the ball valve located near the manifold valve to
allow fluid to flow into the hose reel. To unwind hose just pull on the hose to get the desired amount. To wind up
the hose make sure the toggle switch is in the ON position, push the momentary push button switch until you have
reeled in the amount of hose desire. Turn off the safety switch when not in use.
FOAM MARKER SWITCH
Located to the control panel. Use the rocker switch designate to which boom is to be used to dispense foam. Use
dial located on the foamer to adjust pressure for the amount of foam that will be dispensed. Switch on compressor
also turns foamer on or off.
1 millimeter (mm) = 0.039 inch
1 centimeter (cm) = 0.393 inch