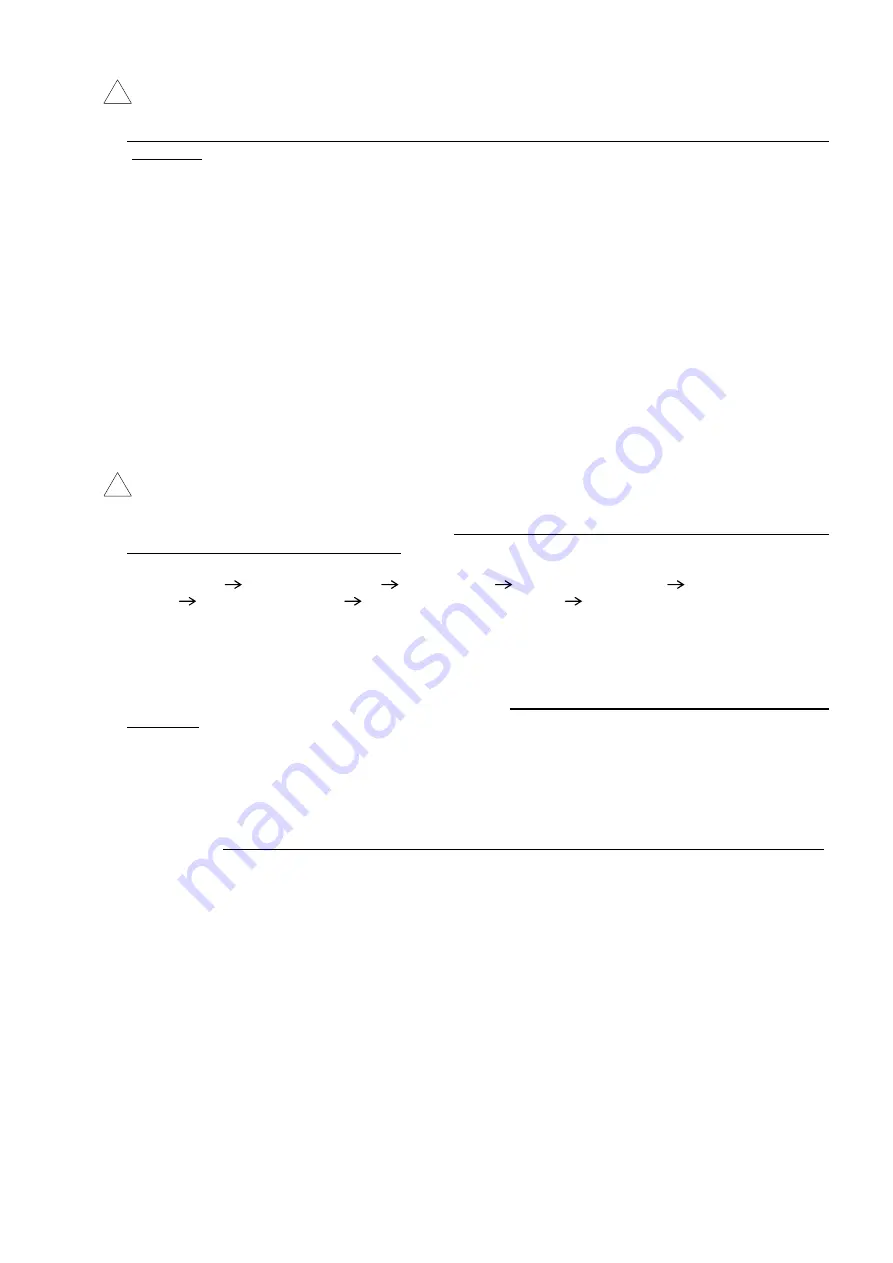
- 2 -
1. Precautions for handling
!
Warning
1) Operating environment
•
When dangerous fluid or fluid possibly harmful to human is used, take measure to isolate human from
the pump. Should the external leakage of transported fluid come out, the serious damage to human
could be caused.
•
When flammable or highly corrosive fluid is transported, keep the fire source away from the pump.
Otherwise, the fire and explosion could be caused.
•
Prevent splash of corrosive fluid or other solvents to the external face of the pump.
•
If attachment of unknown liquid is found on the external face of the pump, do not touch it without care.
2) External leakage of transported fluid
•
When flammable or dangerous fluid is transported, keep the fire source and corrosive material away
from the pump. For this purpose, prepare the vessel for possible leakage and take other measures to
prevent contact with the fire source and corrosive material. Otherwise, the fire and explosion could
be caused.
•
During operation of pump, the transported fluid could leak due to life out of the diaphragm. In this
case, take prevention for the leakage to avoid adverse effect to human or facility.
•
Do not touch the leakage of fluid without care. If the fluid has high temperature or is chemical, the
contact could result in burn and other injuries.
3) Disassembly
•
Do not disassemble the pump.
!
Caution
1) Quality of supplied air
•
Mount the filter with filtration of approx.
0.01
μ
. For the quality of air to be used, refer to Compressed
Air Cleaning Equipments Catalog No. 5
∗
∗
Typical circuit shown on No.5
Compressor HAW(after cooler) AT(air tank) AFF(main line filter) IDF(refrigerating air
dryer) AM(mist separator) AMD(micro mist separator) PAF
•
If the amount of foreign materials generated from air supply (carbon powder etc.) is large, mount
super mist separator etc. to reinforce prevention for attachment of dust. Deposit of foreign materials
could increase resistance and prevent smooth operation.
2) Quality of transported fluid
•
If it is known solid materials enter the transported fluid, mount the filter with filtration of 0.2mm at least
on fluid in.
3) Life and replacement
•
Suspend operation and replace the diaphragm before it reaches the end of life. If the diaphragm
breaks, the transported fluid leaks inside the pump and exhaust port, and the internal parts of the
pump are damaged and the air blows FLUID OUT port.
Calculation of life of diaphragm (depending on operating conditions)
0.130
l
(discharge amount per one cycle) X 50 million cycles (referential life cycles)
Referential
life date =
Discharge per 1min. (
l
) X operating time per day (hour) X 60 (min.)
•
The pump internal capacity is about 600 m
l
.
4) Pilot air
•
Confirm the supplied pilot air is within specified range from 0.2 to 0.5MPa. The air out of this range
could cause malfunction, stop of operation, damage of internal parts and external leakage.
5) Discharge amount and suction head
•
Given discharge rate and suction head are for the condition with fresh water, room temperature,
atmospheric pressure and no piping. Thus, they are varied by physical characteristic of transported
fluid, and in some cases, enough suction head can’t be obtained.
6) Max. Discharge amount
•
Given max. discharge rate is for the condition with supplied pressure of 0.5MPa, no suction head,
piping I.D. of 5/8”, piping length of 0.5m.
7) Operating temperature
•
The pump is available from 0 to 90
O
C, but should be cared not to freeze.(Avoid exposure to heat
cycle)