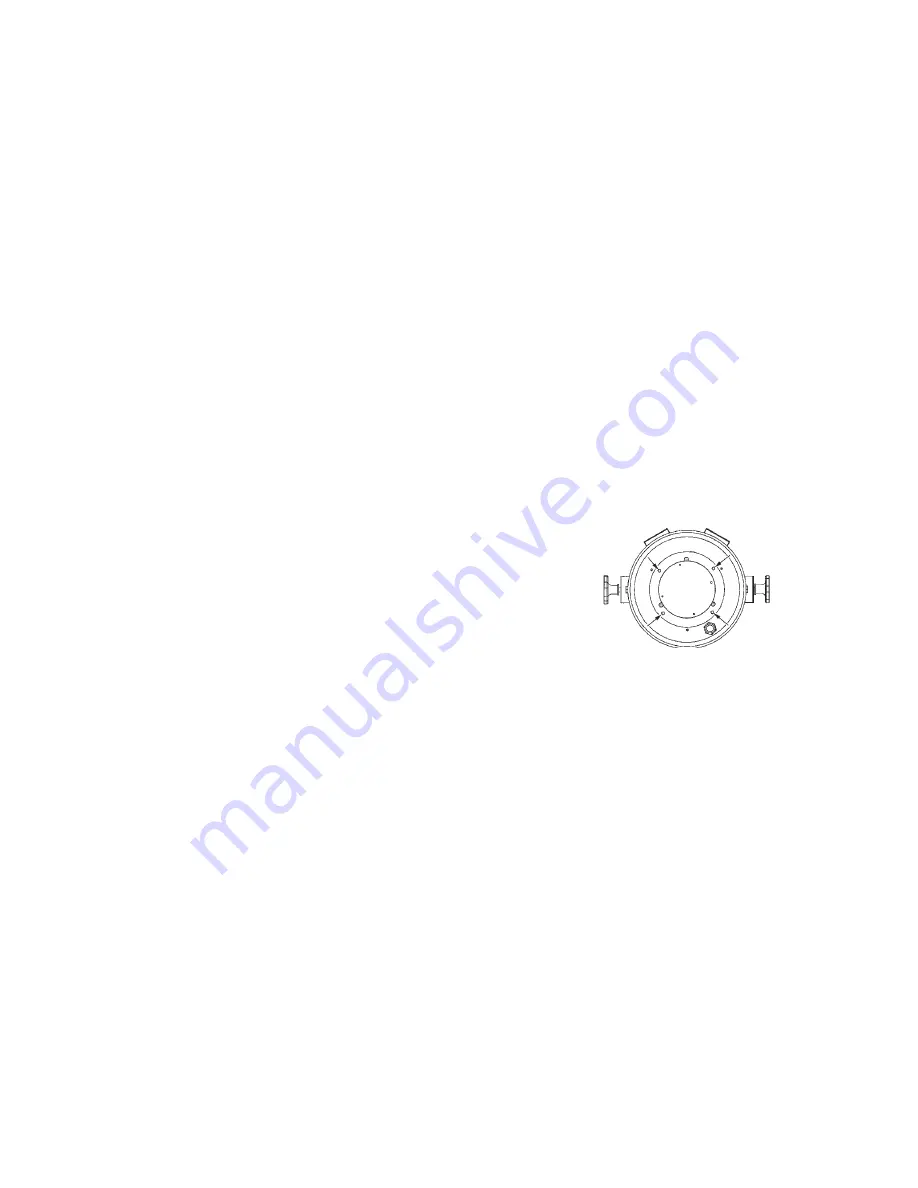
4
MAINTENANCE
Except for unusual conditions of use (dirty environment, flooding, etc.) the frequency of
service and replacement of certain parts and components because of normal wear is
directly related to hours of use.
Inspection and preventive maintenance should be preformed approximately every 250
hours of use or every three months (whichever occurs first). The period can be adjusted
according to actual circumstances.
Lamphead
Clean both surfaces of the front lens on a regular basis. When the lamphead front cover is
removed, clean the surface of the reflector. Normal soiling can be removed from the reflec-
tive surface with a clean, dry cloth. If excessively soiled, use a commercial glass cleaning
solvent (i.e. Windex
®
).
Use no abrasives.
Before replacing the front cover, inspect the
envelope of the metal halide lamp, and dust off any foreign objects. If excessively soiled,
clean with alcohol and a clean cloth.
The lamphouse fan and intake cover can be dismounted from
the lamphead as an assembly by removing the four phillips-
head screws (arrows) adjacent to the lamp position adjustment
holes. A molded plug can then be disconnected from the
blower frame to separate the fan and cover from the lamphead.
Clean the fan blades and keep the intake opening free from
dust or other obstructions. The fan motor requires no oil.
Base Assembly
The motor of the squirrelcage blower in the base requires a few drops of light, non-deter-
gent lubricating oil every 250 hours of use or every three months (whichever occurs first).
The oil holes are marked on the motor housing.
Periodically vacuum or otherwise clean the interior of the base assembly. The heat sink of
the metal halide power supply and the exterior of the motor speed controller must be free
from dust or other obstructions to permit proper cooling. A thermal switch in the lamp
power supply will disable operation of the unit if it overheats. Keep air intakes clean to
allow free air flow.
Both the upper and lower ball bearing pillow block assemblies of the rotating yoke shaft
have easily accessible grease fittings. Check the bearings annually for proper lubrication;
add all-purpose automotive grease as required.
The slip ring attached to the shaft of the yoke assembly transfers electrical current from the
stationary base assembly to the rotating lamphead. Proper maintenance of this item is
mandatory to insure the correct operation of the MiniTracker. Brushes and springs are key
components and are subject to periodic replacement under normal conditions.
Содержание MiniTracker
Страница 8: ...6 FIGURE 1 MiniTracker Lamphead Assembly No 3200387...
Страница 14: ......