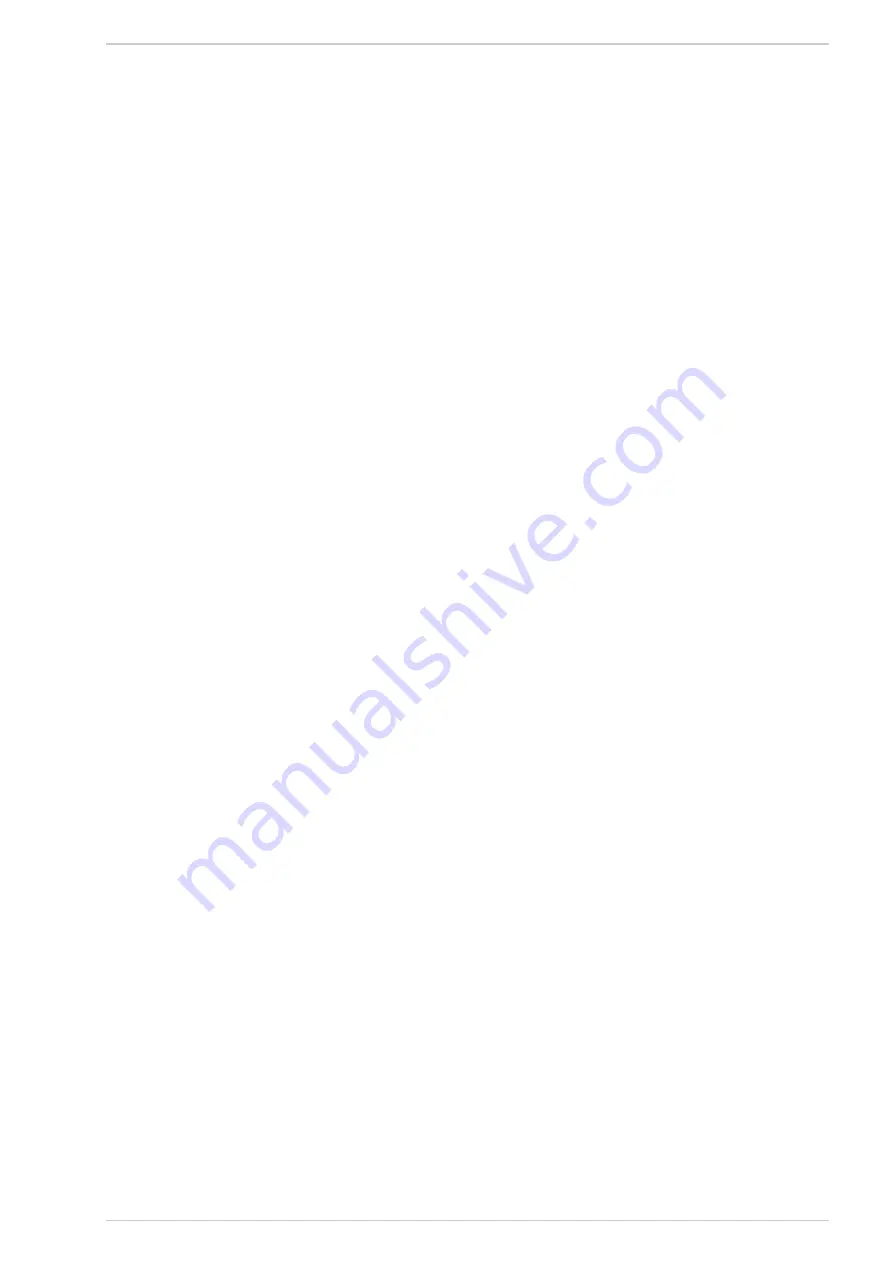
6
Where no specific instructions are given,
the installation should be in accordance
with the relevant recommendations in the
current editions of the following British
St andar ds and Codes of Pr actice: BS
5440-1, BS 5440-2, BS 5449, BS 5482
(propane installations), BS 5546, BS 6700,
BS 6798, BS 6891, Institute of Gas Engi-
neer document IGE/UP-7, BS 7074 (expan-
sion vessel), and to other relevant British
Standards or code of Practice as neces-
sary. It is a
Statutory Requirement
that
the installation conforms to the appropria-
te Building Regulations either The Building
Regulations, The Building Regulations (Sco-
tland), Building Regulations (Northern Ire-
land), the Water Fitting Regulations or
Water Byelaws in Scotland, and the cur-
rent I.E.E Wiring Regulations. When hand-
ling, due consideration should be given to
the appliance weight. If the appliance is not
to be installed immediately it should be sto-
red in a clean dry place.
2.1
BOILER ROOM
The
“DEWY 30/130 HE FS”
version boilers
can be installed in any domestic environ-
ment
without any location restrictions,
other than the load bearing capacity of the
wall where the appliance is to be sited,
(consult section 1.3 for weight),
or “Combu-
stion”
air requirements. However, suitable
clearances for maintenance and servicing
should be provided, see fig. 1.
2.2
CONNECTING UP SYSTEM
Before proceeding to connect up the boi-
ler, you are recommended to make the air
circulating in the piping in order to elimi-
nate any foreign bodies that might be
detrimental to the operating efficiency of
the appliance. When making the hydraulic
connections, make sure that the dimen-
sions indicated in fig. 1 are respected.
Fit the supplied; pressure reducing valve
(30 fig. 2), check valve (31 fig. 2) and expan-
sion relief valve assembly (32 fig. 2) with its
associated tundish (33 fig. 2), in the D.H.W.
supply to the appliance, see fig. 2 and fig. 4
for details. It is important that no isolating
valve is fitted between the expansion relief
valve and the inlet to the D.H.W. tank.
Any additional D.H.W. drain down tap fitted
should be positioned as low as possible to
ensure that at least 80% of the D.H.W.
tank’s capacity can be drained.
If installed in a Hard Water area, then a sui-
table device should be fitted to treat the
mains supply to the appliance (Contact your
Water Distribution Company for advice on
suitable devices).
The discharge pipe of the safety valve
must be connected to a collector funnel
for channelling away any discharge if the
safety valve goes into action.
The gas connection must be made using
seamless steel pipe (Mannesmann type),
galvanized and with threaded joints provi-
ded with gaskets, excluding three-piece
connections, except for initial and end con-
nections.
Where the piping has to pass through
walls, a suitable insulating sleeve must be
provided. When sizing gas piping, from the
meter to the boiler, take into account both
the volume flow rates (consumption) in
m
3
/h and the relative density of the gas in
question.
The sections of the piping making up the
system must be such as to guarantee a
supply of gas sufficient to cover the maxi-
mum demand, limiting pressure loss
between the gas meter and any apparatus
being used to not greater than 1.0 mbar for
family II gases (natural gas).
An adhesive data plate is stuck inside the
front panel; it contains all the technical data
identifying the boiler and the type of gas for
which the boiler is arranged.
2.2.1
Connection of condensation
water trap
The drip board and its water trap must be
connected to a civil drain through a pipe
with a slope of at least 5 mm per metre to
ensure drainage of condensation water.
The plastic pipes normally used for civil
drains are the only type of pipe which is
appropriate for conveying condensation
to the building’s sewer pipes.
2.2.2
Filter on the gas pipe
The gas valve is supplied ex factory with an
inlet filter, which, however, is not adequate to
entrap all the impurities in the gas or in gas
main pipes. To prevent malfunctioning of the
valve, or in certain cases even to cut out the
safety device with which the valve is equip-
ped, install an adequate filter on the gas pipe.
2.2.3
Plant filling
The boiler is designed to house a plant filling
kit (code 8091810), which can be purchased
separately.
2.2.4
Discharge Pipes and fittings
The position of any tundish must be visible to
the occupants and any tundish, drain valve
and discharge pipe and must be sited away
from any electrical components.
The connections to the expansion relief valve
and temperature and pressure relief valve
should not be used for any other purpose.
See fig. 4 for example of the discharge
pipe(s) for the temperature and pressure
relief valve, and expansion relief valve termi-
nations.
Note: it is permitted to connect discharge
pipes together provided that the joint pipe is
sized to accommodate the combined flow.
2.2.5 Expansion Vessel (C.H. only)
C.H. EXPANSION VESSEL – The integral
expansion vessel is pre-charged to a pres-
sure of 1.0 bar, which should be checked
before the C.H. water system is filled.
This vessel is suitable for correct operation
of system capacities up to 82 litre capacity.
If the actual C.H. system volume is greater,
then an additional vessel must be fitted to
the system. For systems where the volume
is greater, the additional expansion vessel
volume can be determined by multiplying
the volume in excess of that which can be
accommodated by the appliance by the fac-
tor 0.901. BS 7074 gives further details
regarding C.H. expansion vessel sizing.
2.3
CHARACTERISTICS
OF C.H. FEEDWATER
– All recirculatory systems will be subject
to corrosion unless an appropriate
water treatment is applied.
This means that the efficiency of the
system will deteriorate as corrosion
sludge accumulates within the system,
risking damage to pump and valves, boil-
er noise and circulation problems.
– For optimum performance after instal-
lation this boiler and its associated cen-
tral heating system must be flushed in
accordance with the guidelines given in
B S 7 5 9 3 “ Tr e a t m e n t o f w a t e r i n
domestic hot water central heating sys-
tems”.
– This must involve the use of a propri-
etary cleanser, such as Sentinel X300
or X400, or Fer nox Super f loc. Full
instructions are supplied with the prod-
ucts, but for immediate information
please cont act GE Betz (0151 420
9563) or Fernox (01799 550 811)
directly.
– For long term protection against corro-
sion and scale, after flushing it is rec-
ommended that an inhibitor such as
Sentinel X100, or Fernox MB-1 or Copal
is dosed in accordance with the guide-
lines given in BS 7593.
Failure to flush and add inhibitor to
the system may invalidate the appli-
ance warranty.
– It is important to check the inhibitor
concentration after installation, system
modification and at every service in
accordance with the manufacturer’s
instructions. (Test kits are available
from inhibitor stockists).
2.4.
FILLING AND COMMISSIONING
2.4.1
D.H.W. circuit
Before filling the D.H.W. system, ensure
2
INSTALLATION