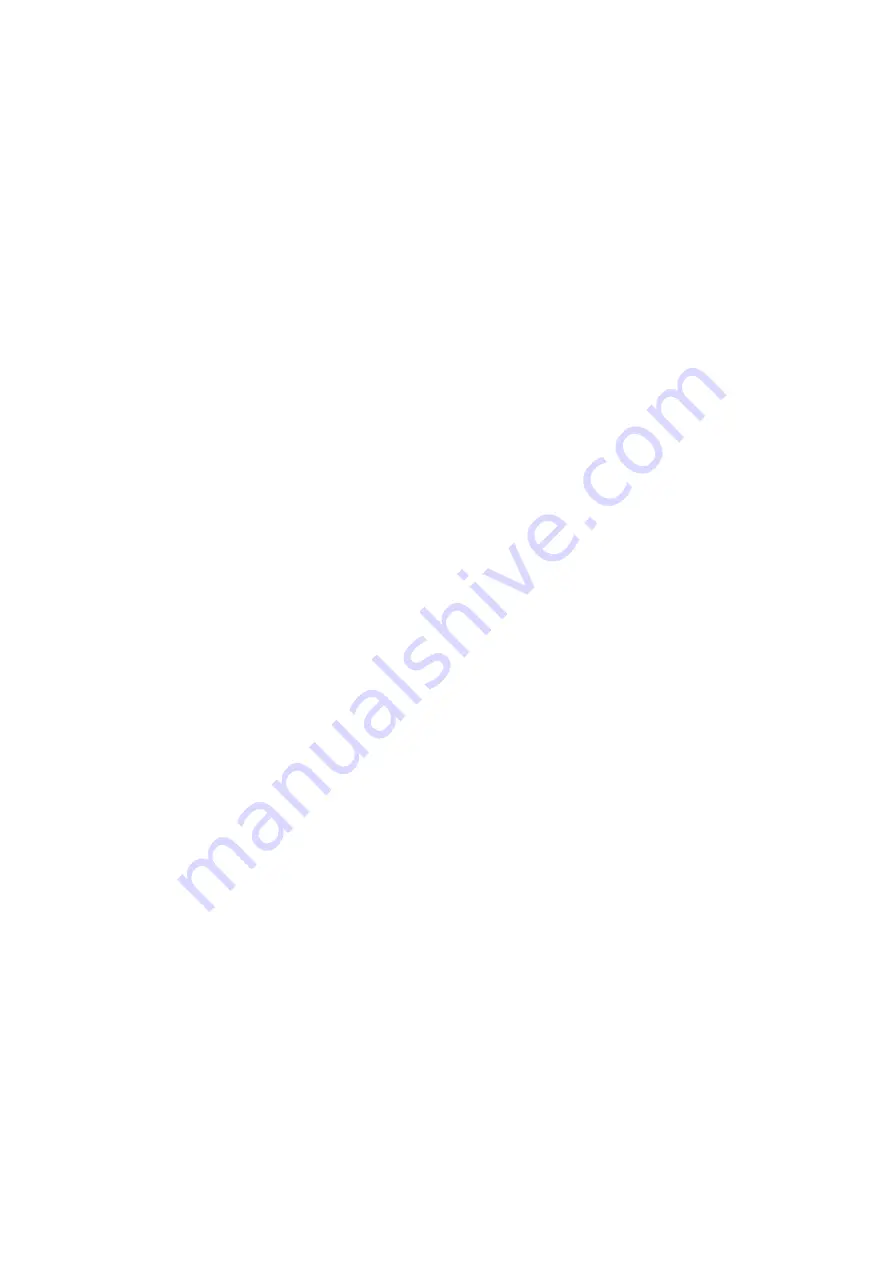
3-14
3.3.6 Motor Drive Precautions
Using the motor drive circuit other than the circuit shown in "Section 3.3.2 Sample Drive Circuit" may
not ensure the specified efficiency.
To prevent degradation in the print quality due to the backlash of the paper drive system, feed the
thermal paper for 48 steps or more at the initialization, at a time after setting/releasing the platen unit,
a time after feeding the thermal paper backward and a time after cutting with a paper cutter. During
this time, drive the motor with constant speed at the 1st acceleration step.
When printing, change the motor drive pulse rate depending on the operational conditions such as
voltage, temperature, and the number of activated dots. (See "CHAPTER 5 PRINT DRIVE
METHOD" for details.)
When printing, change the motor drive pulse rate so that the activation pulse width of the thermal
head does not exceed the sum of the two-step times of the motor. (See "CHAPTER 5 PRINT DRIVE
METHOD" for details.)
Do not perform continuous printing to prevent the motor from overheating.
Surface of the thermal paper may get scratched by backward feed. The backward feed may cause
paper skew and jams depending on the paper roll layout and designing of the paper holder. Be sure
to confirm performance with your product before using the backward feed.
Do not print intermittently. (Do not repeat printing and stopping in a short interval.)
If doing so, print quality may be decreased due to unevenness of the paper feed pitch.
Always perform the start and the stop steps for both character print and bit image print.
For the motor stop, a minimum one dot line of motor feed is required from the step that thermal head
was activated. If the motor is stopped at the step that the thermal head has been activated, paper
feed difficulty may be caused due to sticking of the thermal paper to the thermal head.
Sound and vibration during printing vary depending on the motor drive pulse rate. Verify the
performance with your actual device.