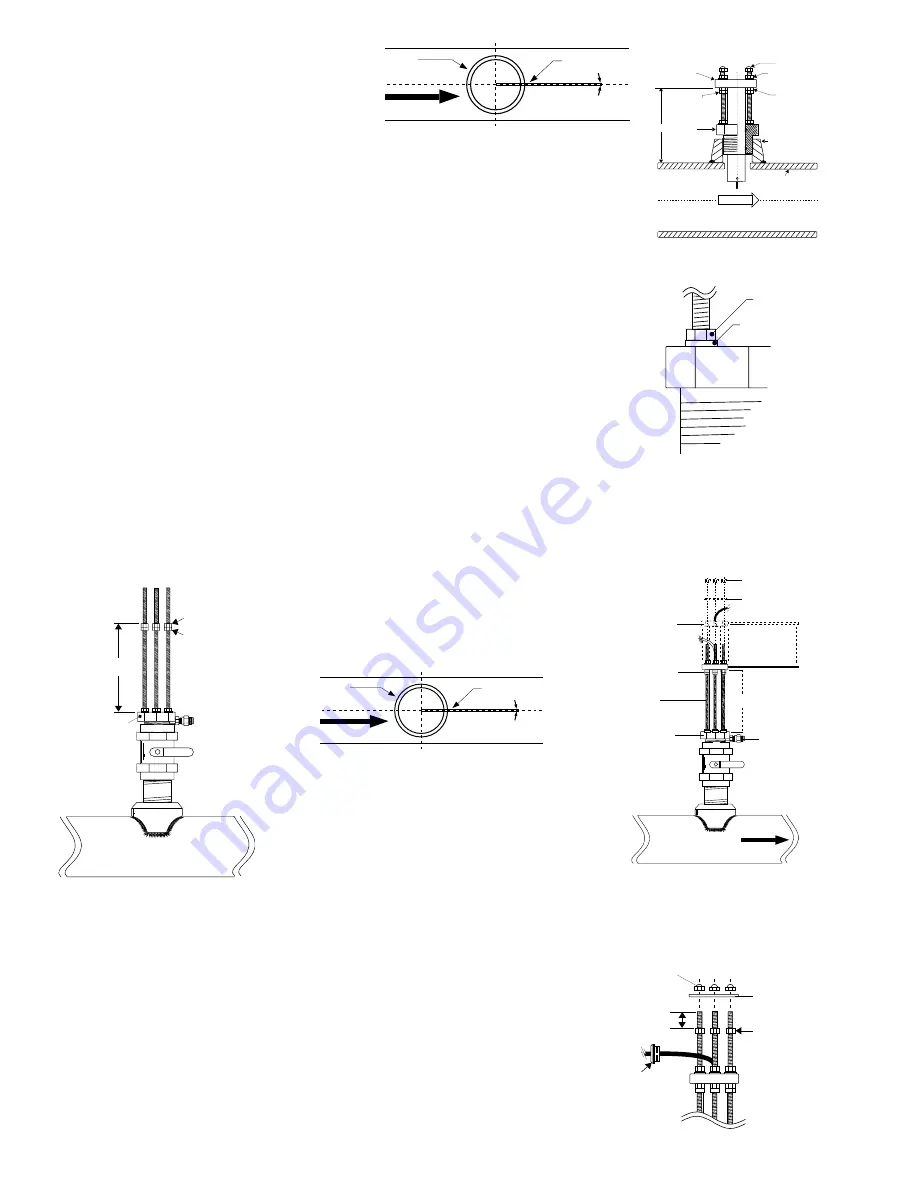
‡ SIGNET
2540 High Performance Flow Sensor
Page 4 of 8
lower hex nut
and jam nuts
sensor flange
18 inch
threaded rods
359 mm (14.14 in)
process pipe (side view)
direction of flow
alignment rod
Upper hex nuts
(3/16 x 1/4-20)
1/4 in. lock
washers
sensor
fitting
bleed valve
cable
grommit
25mm
(1.0 in.)
protector plate
hex nut (3/16 x
1/4-20)
protector plate
removed during
sensor installation
protector plate
cap nuts
lower hex nuts
(3/16 x 1/4-20)
jam nuts
(5/32 x 1/4-20)
359 mm
(14.14 in.)
sensor
fitting
UNDER PRESSURE!
alignment
rod
sensor
flange
process pipe
(top view)
The flow alignment rod
MUST
be
parallel to the process pipe as shown.
flow direction
F.
Thread protector plate hex nuts onto each of the three threaded rods. Adjust each hex nut to a
height of approximately 25 mm (1 in.) from the top of each rod. Remove the black plastic cable
grommet in top of sensor with a screwdriver. Slide the grommet up the cable away from sensor.
(Fig. 12)
Fig. 9
Fig. 10
Fig. 11
D.
Place the alignment rod in the alignment hole on the
sensor flange. Align the flange so rod is parallel to the
process pipe. (Fig. 6)
E
.
Thread upper hex nuts with lock washers until they
contact the sensor flange and tighten. Check for proper "H"
dimension and readjust if necessary. (Fig. 7)
4.7 Hot-Tap Sensor Installation
A.
Thread one hex nut onto each of the three threaded
rods included in package. Install threaded rod with a lock
washer onto the sensor fitting. Secure rods in place by tightening each hex nut against the sensor fitting.
(Fig. 8)
B.
Thread one jam nut and lower hex nut onto each threaded rod so that the top surface of each
nut is 359 mm (14.14 in.) from the top surface of the sensor fitting. Secure each hex nut with a
jam nut. (Fig. 9)
CAUTION: This setting is critical to ensure an adequate sensor seal and to prevent the rotor
from hitting the isolation valve orifice during installation.
C.
Wipe the sensor body with a dry, clean cloth. Orient the alignment hole on the sensor flange
to point
downstream
. Place the slotted flange over the threaded rods. Lower the sensor into the
fitting until the sensor flange rests on the lower hex and jam nuts.
D.
Secure the sensor with lock washers and upper hex nuts on the top of the flange. Before
tightening, align the sensor flange so that the alignment rod is parallel and level with the process
pipe. (Fig. 10 & Fig. 11)
E.
Make sure the bleed valve is closed (full clockwise position).
"
H
"
process
pipe wall I.D.
sensor
fitting
upper hex nuts
& lockwashers
lower hex nuts
jam nuts
sensor
flange
cap nuts
female pipe fitting
FLOW
sensor fitting
hex nut
Lock washer
alignment
rod
sensor
flange
process pipe
(top view)
The flow sensor alignment rod
MUST
be
parallel to the process pipe as shown.
flow direction
Fig. 6
Fig. 7
Fig. 8
Fig. 12