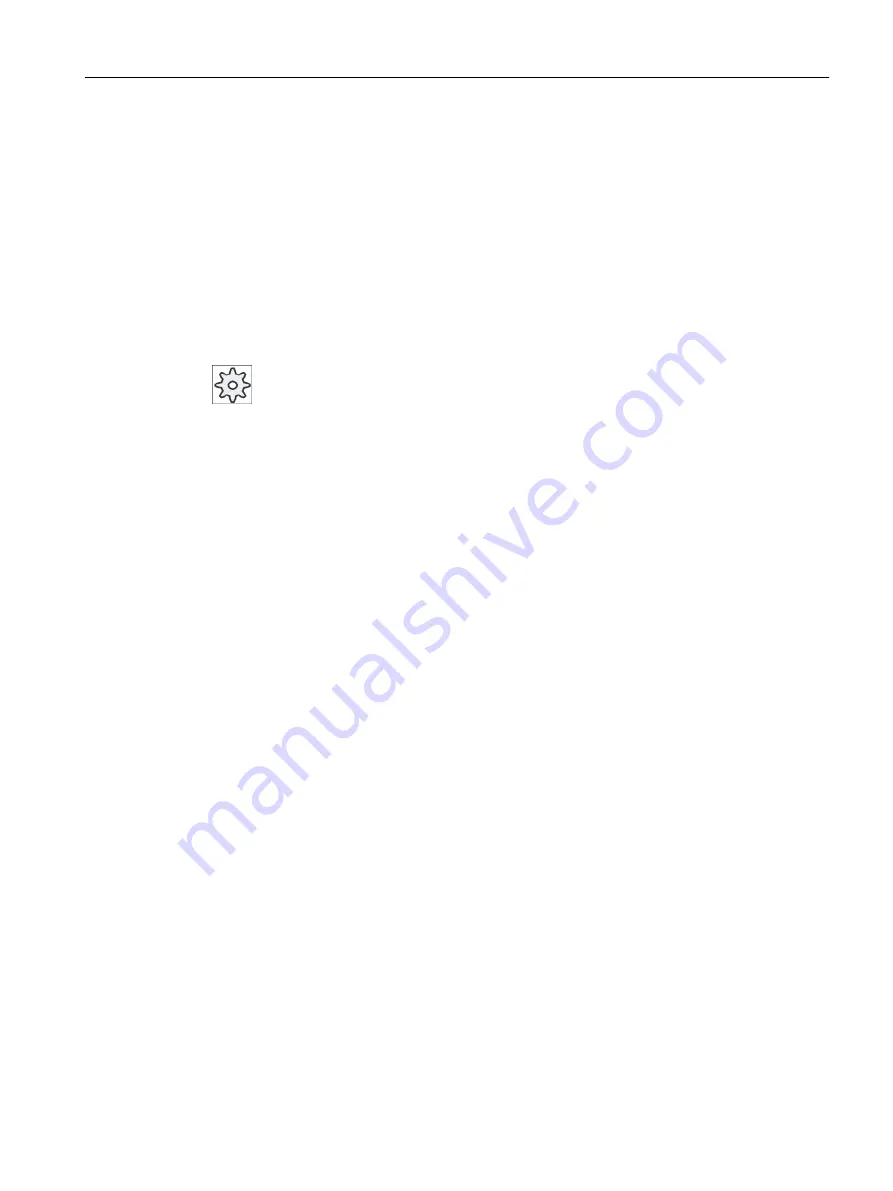
not overlap adjacent blank spigots and is automatically placed by the cycle in a central position
on the finished spigot.
The rectangular spigot is machined using only one infeed. If you want to machine the spigot
using multiple infeeds, you must program the "Rectangular spigot" cycle several times with a
reducing finishing allowance.
Input simple
For simple machining operations, you have the option to reduce the wide variety of parameters
to the most important parameters using the "Input" selection field. In this "Input simple" mode,
the hidden parameters are allocated a fixed value that cannot be adjusted.
Machine manufacturer
Various defined values can be pre-assigned using setting data.
Please refer to the machine manufacturer's specifications.
If the workpiece programming requires it, you can display and change all of the parameters
using "Input complete".
Sequence
1. The tool approaches the starting point at rapid traverse at the height of the retraction plane
and is fed in to the safety clearance. The starting point is on the positive X axis rotated
through α0.
2. The tool approaches the spigot contour sideways in a semicircle at machining feedrate.
The tool first executes infeed at machining depth and then moves in the plane. The
rectangular spigot is machined depending on the programmed machining direction (up-cut/
down-cut) in a clockwise or counterclockwise direction.
3. When the rectangular spigot has been traversed once, the tool retracts from the contour in
a semicircle and then infeed to the next machining depth is performed.
4. The rectangular spigot is approached again in a semicircle and traversed once. This
process is repeated until the programmed spigot depth is reached.
5. The tool moves back to the safety clearance at rapid traverse.
Machining type
● Roughing
Roughing involves moving around the rectangular spigot until the programmed finishing
allowance has been reached.
● Finishing
If you have programmed a finishing allowance, the rectangular spigot is moved around until
depth Z1 is reached.
● Chamfering
Chamfering involves edge breaking at the upper edge of the rectangular spigot.
Programming technological functions (cycles)
10.2 Milling
Milling
Operating Manual, 08/2018, 6FC5398-7CP41-0BA0
437
Содержание SINUMERIK 828D Turning
Страница 68: ...Introduction 2 4 User interface Milling 68 Operating Manual 08 2018 6FC5398 7CP41 0BA0 ...
Страница 162: ...Setting up the machine 4 12 MDA Milling 162 Operating Manual 08 2018 6FC5398 7CP41 0BA0 ...
Страница 270: ...Machining the workpiece 6 17 Setting for automatic mode Milling 270 Operating Manual 08 2018 6FC5398 7CP41 0BA0 ...
Страница 278: ...Swivel combination 45 90 Simulating machining 7 1 Overview Milling 278 Operating Manual 08 2018 6FC5398 7CP41 0BA0 ...
Страница 294: ...Simulating machining 7 9 Displaying simulation alarms Milling 294 Operating Manual 08 2018 6FC5398 7CP41 0BA0 ...
Страница 316: ...Generating a G code program 8 10 Measuring cycle support Milling 316 Operating Manual 08 2018 6FC5398 7CP41 0BA0 ...
Страница 684: ...Collision avoidance 12 2 Set collision avoidance Milling 684 Operating Manual 08 2018 6FC5398 7CP41 0BA0 ...
Страница 746: ...Tool management 13 16 Working with Multitool Milling 746 Operating Manual 08 2018 6FC5398 7CP41 0BA0 ...
Страница 830: ...Alarm error and system messages 15 9 Remote diagnostics Milling 830 Operating Manual 08 2018 6FC5398 7CP41 0BA0 ...
Страница 846: ... Working with Manual Machine 16 7 More complex machining Milling 846 Operating Manual 08 2018 6FC5398 7CP41 0BA0 ...
Страница 870: ...HT 8 840D sl only 18 5 Calibrating the touch panel Milling 870 Operating Manual 08 2018 6FC5398 7CP41 0BA0 ...
Страница 890: ...Easy Message 828D only 20 7 Making settings for Easy Message Milling 890 Operating Manual 08 2018 6FC5398 7CP41 0BA0 ...
Страница 924: ...Edit PLC user program 828D only 23 8 Searching for operands Milling 924 Operating Manual 08 2018 6FC5398 7CP41 0BA0 ...
Страница 925: ...Appendix A A 1 840D sl 828D documentation overview Milling Operating Manual 08 2018 6FC5398 7CP41 0BA0 925 ...