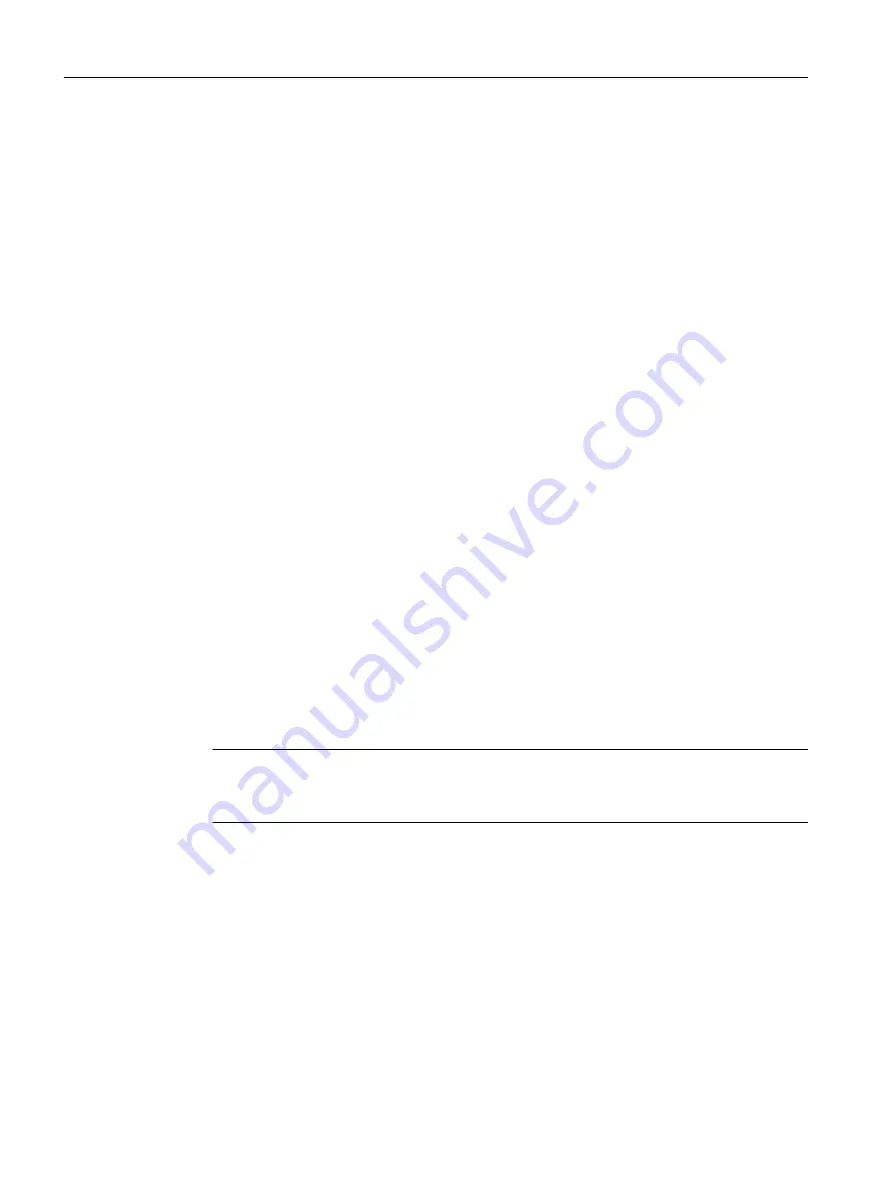
Soft first cut into the material
The entry into the material can be influenced, depending on the tool and the material.
The soft first cut comprises two partial distances:
● The first cut feedrate is maintained to a programmable first feed distance ZS1.
● An additional programmable feed distance ZS2 immediately following ZS1 is used to
continuously increase the first cut feedrate (with FLIN) to the drilling feedrate.
With chip breaking / swarf removal, this mechanism takes effect at each infeed.
The input parameters ZS1 and ZS2 are maximum values that are limited by the cycle to the
infeed depth to be executed.
Deep-hole drilling at the exit from the hole
It makes sense to reduce the feedrate when for through drilling the exit is inclined with respect
to the tool axis.
● Through drilling "no"
The machining feedrate is used when drilling to the final drilling depth. You then have the
option of programming a dwell time at the drilling depth.
● Through drilling "yes"
Up to the remaining drilling depth, you program drilling with the drilling feedrate and, from
that point onward, you program drilling with a special feedrate FD.
Retraction
Retraction can be realized at the pilot hole depth or the retraction plane.
● Retraction to the retraction plane is realized with G0 or feedrate, programmable speed as
well as direction of rotation respectively stationary spindle.
● For retraction at the pilot hole depth, subsequent retraction and insertion are performed
with the same data.
Note
Direction of spindle rotation
The direction of spindle rotation is not reversed; however, where necessary, can be stopped.
Coolant
The technology and tools require that also in the G code, the control for the coolant is
supported.
● Coolant on
Switch on at Z0 + safety clearance or at the pilot hole depth (if a pilot hole is being used)
● Coolant off
Always switch off at the final drilling depth
● Programming in the G code
An executable block (M command or subprogram call), which can be programmed as string.
Programming technological functions (cycles)
10.1 Drilling
Milling
386
Operating Manual, 08/2018, 6FC5398-7CP41-0BA0
Содержание SINUMERIK 828D Turning
Страница 68: ...Introduction 2 4 User interface Milling 68 Operating Manual 08 2018 6FC5398 7CP41 0BA0 ...
Страница 162: ...Setting up the machine 4 12 MDA Milling 162 Operating Manual 08 2018 6FC5398 7CP41 0BA0 ...
Страница 270: ...Machining the workpiece 6 17 Setting for automatic mode Milling 270 Operating Manual 08 2018 6FC5398 7CP41 0BA0 ...
Страница 278: ...Swivel combination 45 90 Simulating machining 7 1 Overview Milling 278 Operating Manual 08 2018 6FC5398 7CP41 0BA0 ...
Страница 294: ...Simulating machining 7 9 Displaying simulation alarms Milling 294 Operating Manual 08 2018 6FC5398 7CP41 0BA0 ...
Страница 316: ...Generating a G code program 8 10 Measuring cycle support Milling 316 Operating Manual 08 2018 6FC5398 7CP41 0BA0 ...
Страница 684: ...Collision avoidance 12 2 Set collision avoidance Milling 684 Operating Manual 08 2018 6FC5398 7CP41 0BA0 ...
Страница 746: ...Tool management 13 16 Working with Multitool Milling 746 Operating Manual 08 2018 6FC5398 7CP41 0BA0 ...
Страница 830: ...Alarm error and system messages 15 9 Remote diagnostics Milling 830 Operating Manual 08 2018 6FC5398 7CP41 0BA0 ...
Страница 846: ... Working with Manual Machine 16 7 More complex machining Milling 846 Operating Manual 08 2018 6FC5398 7CP41 0BA0 ...
Страница 870: ...HT 8 840D sl only 18 5 Calibrating the touch panel Milling 870 Operating Manual 08 2018 6FC5398 7CP41 0BA0 ...
Страница 890: ...Easy Message 828D only 20 7 Making settings for Easy Message Milling 890 Operating Manual 08 2018 6FC5398 7CP41 0BA0 ...
Страница 924: ...Edit PLC user program 828D only 23 8 Searching for operands Milling 924 Operating Manual 08 2018 6FC5398 7CP41 0BA0 ...
Страница 925: ...Appendix A A 1 840D sl 828D documentation overview Milling Operating Manual 08 2018 6FC5398 7CP41 0BA0 925 ...