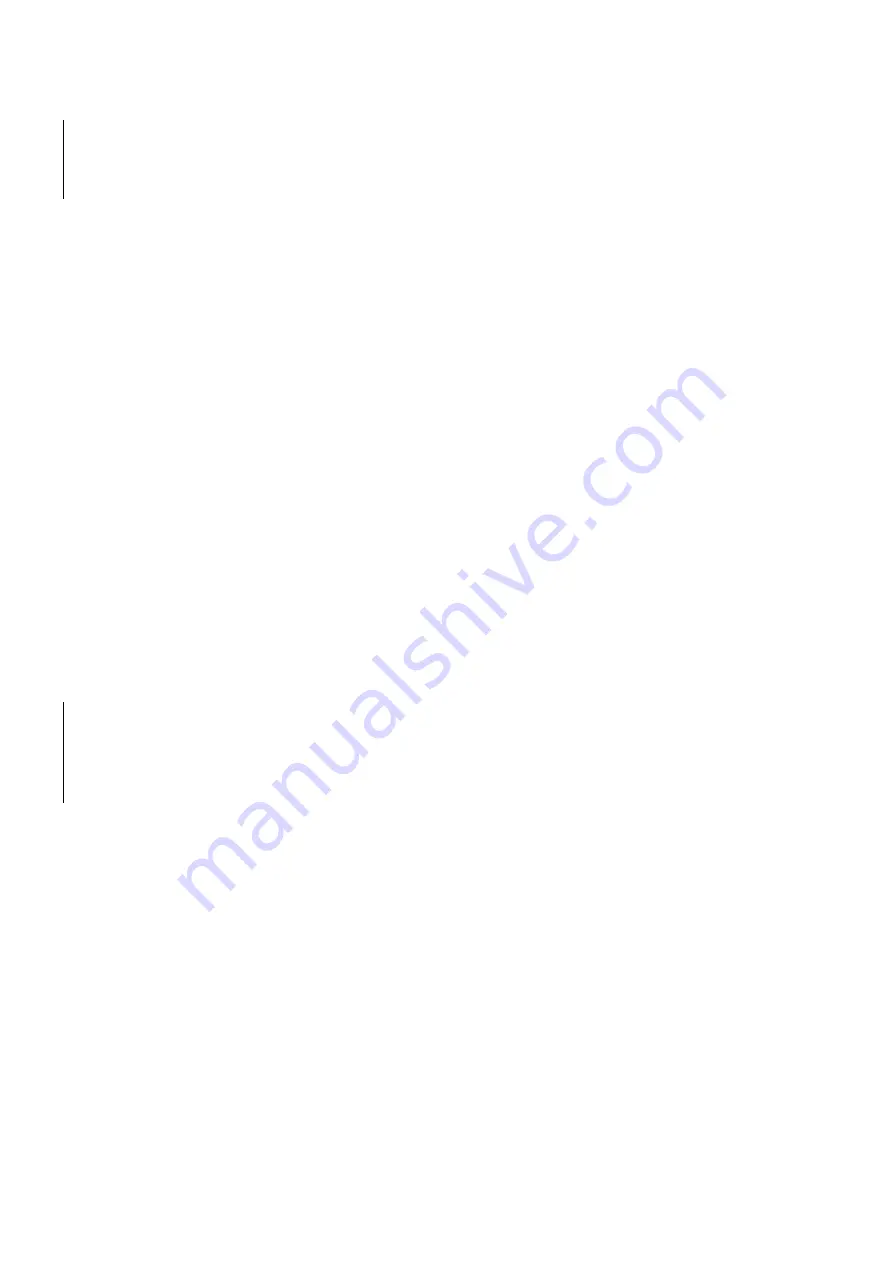
Programming and Operating Manual (Milling)
88
6FC5398-4DP10-0BA1, 01/2014
Programming example
N10 G1 X70 Z20 F300 S270 M3
;
Before
the axis traversing X, Z the spindle accelerates to 270
rpm, clockwise
N80 S450
; Speed change
N170 G0 Z180 M5
; Z movement, spindle comes to a stop
8.8.3
Spindle positioning: SPOS
Functionality
Requirement: The spindle must be technically designed for position control.
With the function SPOS= you can position the spindle in a specific angular position. The spindle is held in the position
through position control.
The speed of the positioning procedure is defined in machine data.
With SPOS=
value
from the M3/M4 movement, the respective direction of rotation is maintained until the end of the
positioning. When positioning from standstill, the position is approached via the shortest path. The direction results from the
respective start and end position.
Exception: First movement of the spindle, i.e. if the measuring system is not yet synchronized. In this case, the direction is
specified in machine data.
Other movement specifications for the spindle are possible with SPOS=ACP(...), SPOS=ACN(...), ... as for rotary axes.
The spindle movement takes place parallel to any other axis movements in the same block. This block is ended when both
movements are finished.
Programming
SPOS=...
; Absolute position: 0 ... <360 degrees
SPOS=ACP(...)
; Absolute dimensions, approach position in positive direction
SPOS=ACN(...)
; Absolute dimensions, approach position in negative direction
SPOS=IC(...)
; Incremental dimensions, leading sign determines the traversal direction
SPOS=DC(...)
; Absolute dimensions, approach position directly (on the shortest path)
Programming example
N10 SPOS=14.3
; Spindle position 14.3 degrees
N80 G0 X89 Z300 SPOS=25.6
; Positioning spindle with axis movements
; This block is ended when all movements have finished
N81 X200 Z300
; The N81 block only begins once the spindle position from N80
is reached
8.9
Contour programming support
8.9.1
Contour definition programming
Functionality
If the end points for the contour are not directly specified in the machining drawing, it is also possible to use an angle
specification ANG=... to determine the straight line. In a contour corner, you can insert the elements chamfer or rounding.
The respective instruction CHR= ... or RND=... is written in the block, which leads to the corner.
The blueprint programming can be used in blocks with G0 or G1 (linear contours).
Theoretically, any number of straight line blocks can be connected and a rounding or a chamfer can be inserted between
them. Every straight line must be clearly identified by point values and/or angle values.