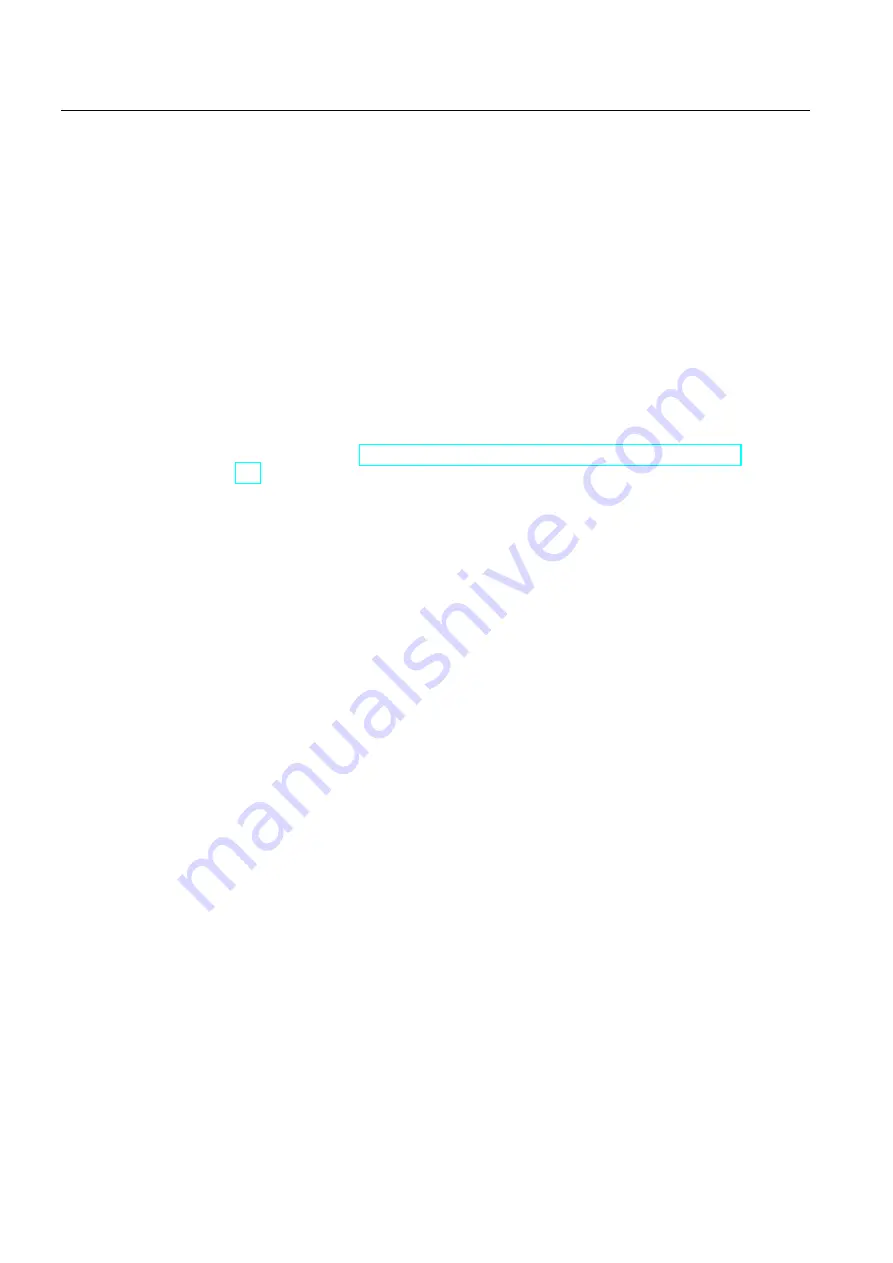
Fault-tolerant automation systems
2.1 Redundant SIMATIC automation systems
S7-400H
26
System Manual, 03/2012, A5E00267695-11
Why fault-tolerant automation systems?
The purpose of using fault-tolerant automation systems is to reduce production downtimes,
regardless of whether the failures are caused by an error/fault or are due to maintenance
work.
The higher the costs of production stops, the greater the need to use a fault-tolerant system.
The generally higher investment costs of fault-tolerant systems are soon recovered since
production stops are avoided.
Redundant I/O
Input/output modules are termed redundant when they exist twice and they are configured
and operated as redundant pairs. The use of redundant I/O provides the highest degree of
availability, because the system tolerates the failure of a CPU or of a signal module. If you
require a redundant I/O, you use the blocks of the "Functional I/O Redundancy" function
block library, see section Connecting redundant I/O to the PROFIBUS DP interface
(Page 177).
Содержание SIMATIC S7-400H
Страница 24: ...Preface 1 1 Preface S7 400H 24 System Manual 03 2012 A5E00267695 11 ...
Страница 46: ...Getting Started 4 5 Special layout features of SIMATIC Manager S7 400H 46 System Manual 03 2012 A5E00267695 11 ...
Страница 120: ...Memory concept 10 1 Overview of the memory concept of S7 400H CPUs S7 400H 120 System Manual 03 2012 A5E00267695 11 ...
Страница 258: ...Communication 14 8 General issues regarding communication S7 400H 258 System Manual 03 2012 A5E00267695 11 ...
Страница 354: ...Synchronization modules 18 3 Selecting fiber optic cables S7 400H 354 System Manual 03 2012 A5E00267695 11 ...
Страница 434: ...Technical data 20 6 Runtimes of the FCs and FBs for redundant I Os S7 400H 434 System Manual 03 2012 A5E00267695 11 ...
Страница 460: ...Function modules and communication processors supported by the S7 400H S7 400H 460 System Manual 03 2012 A5E00267695 11 ...