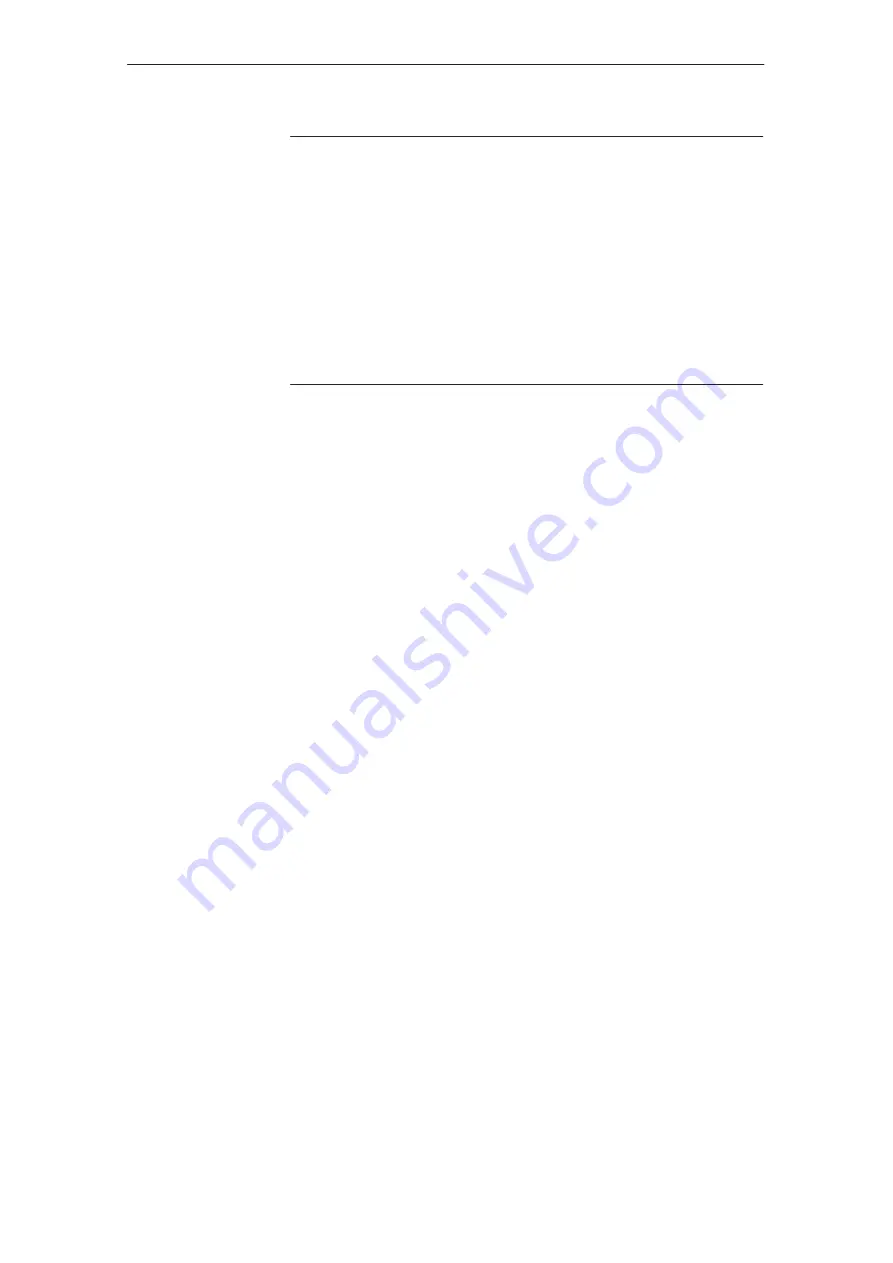
1
05.01
1.1 Overview of SIMODRIVE 611
1-28
©
Siemens AG 2012 All Rights Reserved
SIMODRIVE 611 Configuration Manual (PJU) – 02/2012 Edition
Note
Siemens accepts the warranty for satisfactory and reliable operation of the
drive system under the clear understanding that only original SIMODRIVE
system components are used in conjunction with the original accessories
described in this Configuration Manual and in Catalog NC 60.
The user must take the planning and engineering data into consideration.
Combinations that differ from the engineering specifications – where relevant,
also in conjunction with third–party products, require a special, contractual
agreement.
The converter system is designed for installation in control cabinets which
conform with the relevant standards for processing machines, especially
EN 60204.
Description
The converter system comprises the following modules (refer to Fig. 1-2 and
1-3):
S
Transformer
S
Switching and protective elements
S
Line filter
S
Commutating reactors
S
Infeed modules
S
Power modules
S
Control units harmonized to the application technology/process and motor
types
S
Special modules and other accessories
Various cooling methods are available for the power–dependent line supply
infeed and drive modules:
S
Internal cooling
S
External cooling
S
Hose cooling
1 Overview of the Drive System
11.05