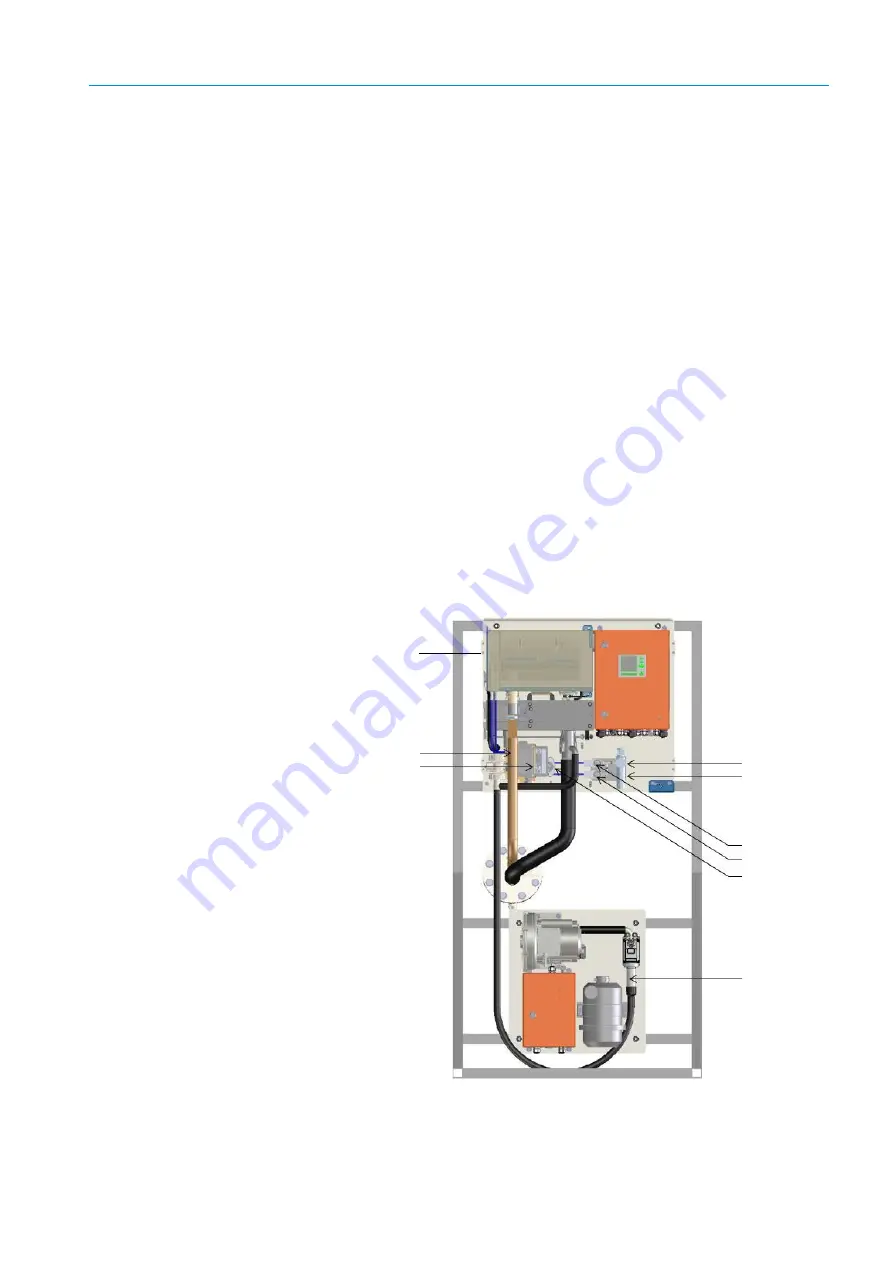
7
8024019/AE00/V1-0/2019-02| SICK
A D D E N D U M T O O P E R A T I N G I N S T R U C T I O N S | FWE200DH
Subject to change without notice
PRODUCT DESCRIPTION
2
2
Product description
2.1
Characteristics and function
The water back purge WBP is an option of the FWE200DH measuring system.
Water purging is carried out regularly during the control cycle. This runs every 8 hours
according to the factory settings. The cycle time can be changed using SOPAS ET (see
FWE200DH Operating Instructions). The water flow dissolves deposits mechanically, salt
deposits dissolve in the water and are flushed into the flue gas duct.
2.2
Device components
The following components are additionally installed or prepared at the factory for the
FWE200DH with water back purge WBP:
●
Pressure regulator with manometer and water filter
●
Water connection, customer interface G¼ inch inside thread
●
Valve 1
●
Valve 2
●
Ball valve
●
Connecting hoses
●
Purge air heater (optional, must be ordered separately)
●
Heated extraction hose (optional, must be ordered separately)
●
WBP swirl chamber cover for water back purging
Fig. 1: Auxiliary components FWE200DH
Pressure regulator
Water connection
Valve 1
Valve 2
Ball valve
Connection hoses
Purge air heater (optional)
Heated extraction hose
(optional)
WBP swirl chamber cover for
water back purging