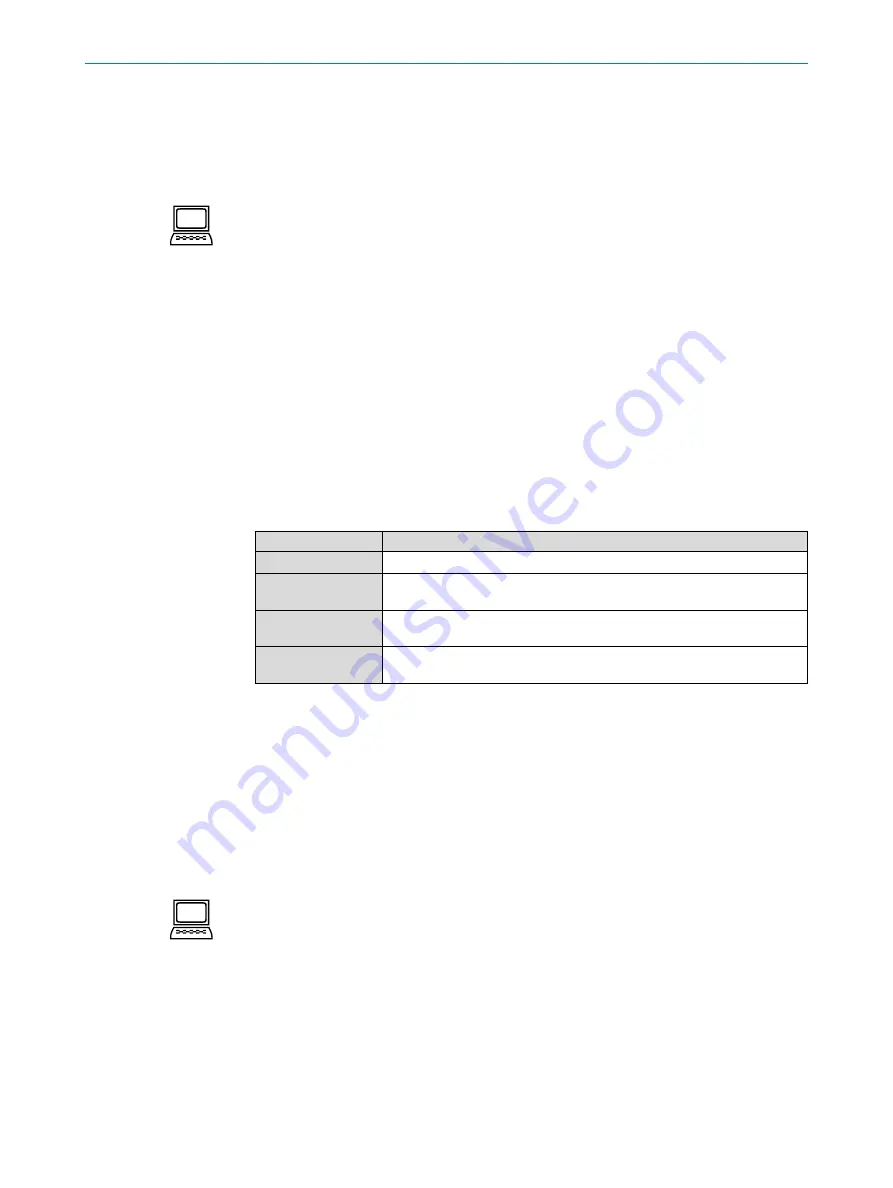
O P E R AT I N G I N S T R U C T I O N S |
Bulkscan LMS511
8014829/ZNC5/2017-06-06 |
S I C K
Subject to change without notice
6 0
COMMISSIONING
• Slits or gaps on the conveyor belt have to be covered in order to teach-in the refer-
ence contour
• We recommend setting a value of at least 5 mm to avoid incorrect measurement due
to conveyor belt vibration.
How to configure the ignoring of measurement points below the reference contour:
Switch to the
System
tab.
Activate the
Ignore measurement points below the reference contour
checkbox.
Configure the
Threshold
value in mm.
8.4
Monitoring of the contamination degree
The front screen of the Bulkscan may become contaminated due to the environmental
conditions. This reduces the emitted and received energy from the laser beam and
thereby the measurement accuracy.
The Bulkscan has six contamination sensors which monitor contamination during oper-
ation.
You can choose from different contamination measurement strategies, these determine
the number of contamination sensors which are evaluated.
Strategy
Behavior
Inactive
Contamination measurement is not carried out
Highly availabe
Contamination warning and contamination errors are only output when
the front screen is uniformly contaminated.
Available
Contamination warning and contamination errors are output when the
front screen is partially contaminated.
Sensitive
Contamination warning and contamination errors are output even when
there is just a little or local contamination.
Tab. 14: Contamination measurement strategies
A contamination warning is output first for the different degrees of contamination. If
the front screen is not cleaned and contamination increases, then a contamination
error is output and the Bulkscan stops the measuring operation.
Static charges cause dust particles to be attracted to the front screen. The front screen
of the Bulkscan should be cleaned regularly and in the event of contamination (see
"9.1 Cleaning the front screen“ on page 64).
How to configure contamination measurement:
Switch to the
System
tab.
Configure the contamination measurement
Strategy
.
Configure the
Response time
.
Configure the
Threshold
for the contamination warning and error. Enter the degree of
available view as a % for the thresholds.
Note
Note
8.5
Scan frequency
The scan frequency is the frequency with which the Bulkscan determines and outputs
measured values at the interface.
Scan frequency
Cycle time
35 Hz
28.6 ms
50 Hz
20.0 ms
75 Hz
13.3 ms
Tab. 15: Configurable scan frequencies
•
If you configure the output of the
Volume quota
or the
Mass quota
on a digital
output, then make sure that duration of the pause between pulses is longer than
the cycle time resulting from the scan frequency (see "4.13 Digital outputs“ on page
• The selection of the scan frequency affects the energy consumption of the sensor.
System
tab,
Scan frequency
group
8.6
Taking a reference measurement (compensation function)
Depending on the application, systematic errors can occur during the determination of
the volume. In particular the compression of the lower layers of bulk due the mass of
the bulk above will result in reproducible deviations. This systematic error can be calcu-
lated from the volume using a compensation function.
The software calculates this compensation function based on one or more reference
measurements:
• Perform up to 10 reference measurements when the load on the conveyor belt varies
in operation.
• The best results are achieved if the reference measurements cover the entire mea-
suring range, meaning minimum to maximum belt load.
If you replace a sensor, you can also enter the compensation function directly instead
of the reference measurements.
Requirements for the prevention of measurement errors
• Bulk height of the good transported at least 200 mm.
• Constant belt speed during the calibration.
• Constant bulk properties.
• Suitable mounting location and mounting orientation (see "5.2 Selecting the mount-
• Deformations of the conveyor belt under load < 5 mm.
Reference volume
For the reference measurement you need a reference volume. To determine the refer-
ence volume, a reference measuring system with an accuracy of ±1% with reference
to the end value of the measuring range is required. Examples for suitable reference
measuring systems:
• Packing plant for the bulk:
• Vessel with straight contours (e.g., container) into which the bulk is transported with
the possibility of subsequently determining the volume.
Note
Note