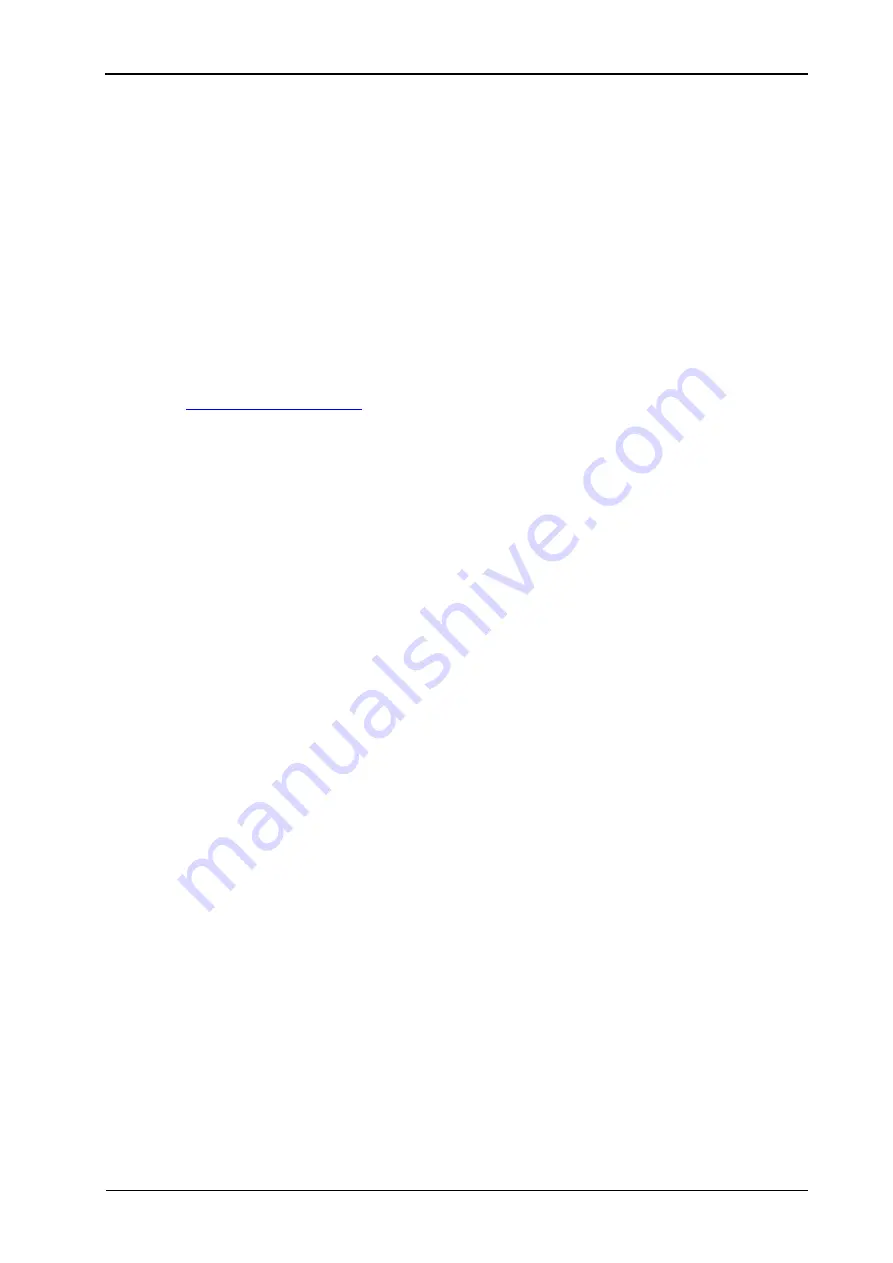
Introduction
20
ATM60 / ATM90 / KHK53
Dec 2021
The Encoder SIG has, in agreement with the PNO, produced a device profile (Version 1.1), to
ensure the interoperability of their devices.
The following issues were defined:
•
Measuring principle of absolute and incremental encoders.
•
Functionality of two device classes (Device Class 1, Class 2).
4.5 Further Information
Profibus Nutzerorganisation e.V. (PNO)
Haid-und-Neu-Str. 7
D-76131 Karlsruhe
Phone: (49) 721 - 96 58 590
Fax:
(49) 721 - 96 58 589
Web:
http://www.profibus.com
http://www.profibus.de
Further literature and guidelines (partly available in English only, but partly also in German):
•
Profibus DP Specification
•
Guideline for Profibus DP/FMS (V1.0), Order No. 2.112
•
Profibus RS485 User & Installation Guideline (V1.1), Order No. 2.262
•
Profibus Profile for Encoders (V1.1), Order No. 3.062
•
M. Popp, Profibus DP/DPV1, (Huethig, 2000), ISBN 3-7785-2781-9
•
New Rapid Way to Profibus DP (2002), Order No. 4.072
•
Profibus System Description (Vers. 10/ 2002), Order No. 4.002
Содержание ATM60
Страница 7: ...Dec 2021 ATM60 ATM90 KHK53 5 ...
Страница 10: ...Introduction 8 ATM60 ATM90 KHK53 Dec 2021 ...
Страница 73: ...Technical Description Dec 2021 ATM60 ATM90 KHK53 71 Notes ...