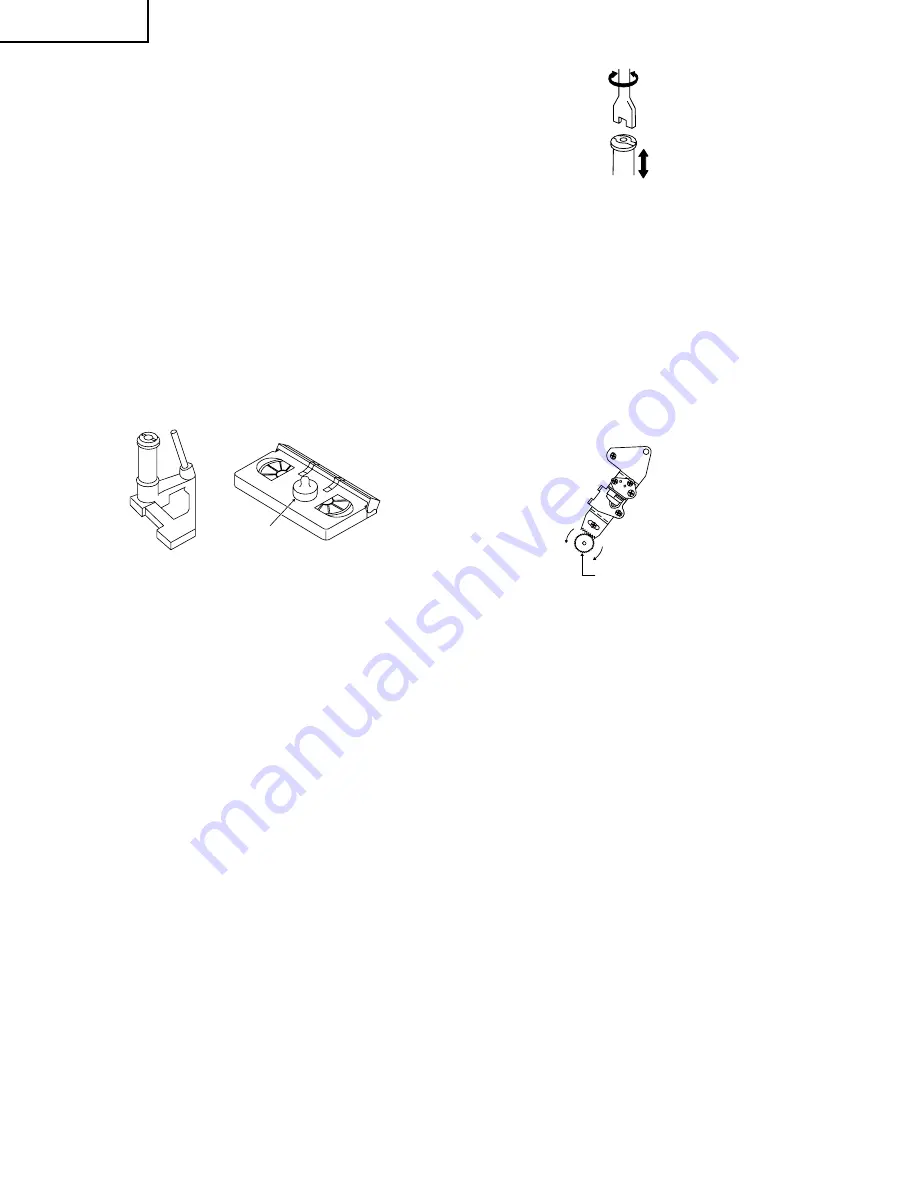
38
VT-G14
VT-G21
Figure 1-32.
ADJUSTMENT OF TAPE DRIVE TRAIN
1. Tape run rough adjustment
1
Remove the cassette housing control assembly.
2
After shortcircuiting TP7701 (J301) and TP7702
(J302) provided at the left on the main PWB, plug
in the power cord, then turn on the power.
3
Check and adjust the position of the tension pole.
(See page 33.)
4
Check and adjust the video search rewind back
tension. (See page 33.)
5
Connect the oscilloscope to the test point for PB
CHROMA envelope output (TP3301). Set the
synchronism of the oscilloscope to EXT. The PB
CHROMA signal is to be triggered by the head
switching pulse (TP3302).
6
After turnning off the power, set the alignment
tape (VROCPSV) then turn on the power and
playback the tape. (Put a 500g weight on the
cassette tape to prevent lift of cassette tape.)
7
Press the tracking button (+), (–) and change the
envelope waveform from max to min and from min
to max. At this time make sure that the envelope
waveform changes nearly parallel.
8
Unless the envelope waveform changes nearly
parallel, adjust the height of supply side and take-
up side guide roller so that the envelope wave-
form changes nearly parallel. (For envelop ad-
justment procedure refer to Figure 1-35.)
9
Turn the tilt screw to remove the tape crease at
the fixing guide flange.
Play back the tape and check for tape crease at
the fixing guide flange.
(1) If there is no tape crease
Turn the tilt screw clockwise so that tape
crease appears once at the flange, and then
return the tilt screw so that the crease disap-
pears.
(2) If there is tape crease
Turn counterclockwise the tilt screw so that
the tape crease disappears.
(Reference) If the tilt screw is turned clockwise
crease appears at the lower flange.
Notes:
1. Previously set the tracking control in the center posi-
tion, and adjust the envelop waveform to maximum
with X value adjustment nut. Thereby the tape run
rough adjustment is facilitated.
2. Especially the outlet side envelope waveform must
have higher flatness.
Figure 1-31.
Guide roller
Cassette Tape
500g
Weight of 500g
2. Adjustment of A/C head height and azimuth
1
Perform the initial setting of A/C head position by
the method stated in "Page 37 Replacement -3.".
2
Connect the oscilloscope to the audio output
(TP6601).
3
Using the alignment tape in which 1 kHz linear
audio signal has been recorded, adjust the height
screw so as to get max audio output.
4
Using the alignment tape in which 6 kHz linear
audio signal has been recorded, adjust the azi-
muth screw so as to get max audio output.
5
The adjustment of
3
and
4
twice or three times
repeat, and finally adjust
4
.
Figure 1-33.
3. Tape run adjustment
1
Connect the oscilloscope to PB CHROMA enve-
lope output test point (TP3301), set oscilloscope
sync to EXT, trigger-input the head switching
pulse (TP3302).
2
Rough adjustment of X value
Tentatively fix A/C head arm screws
1
and
2
by
the method described in Page 36 "Replacement
-3.".
After shortcircuiting TP7701 (J301) and TP7702
(J302), plug in the power cord, turn off the power,
set the alignment tape (VROCPSV), turn on the
power and then playback the tape. As a result the
auto-tracking is automatically cancelled, so that
the X value adjustment mode is set.
Move the A/C head with the X value adjustment
gear driver (JiGDRiVER-6) by the method shown
in Figure 1-33, and adjust the A/C head so as to
get the maximum envelope waveform. (Note:
When the A/C head is adjusted, adjust so that the
maximum envelop waveform is obtained nearest
the position of initial setting made in Page 37.)
3
When the VROUBZFS tape is used, press the
tracking button (+), (–) and change the envelope
waveform from max to min and from min to max.
At this time adjust the height of supply and take-
up side guide roller with the adjustment driver
(JiGDRiVERH-4) so that the envelope waveform
changes nearly parallel.
For X value adjustment
Adjust the X value, turning the gear-
type screwdriver.
Содержание VT-G14
Страница 69: ...71 VT G14 VT G21 70 12 11 10 9 8 7 6 5 4 3 2 1 A B C D E F G H BLOCK DIAGRAM OF TV SECTION 1 ...
Страница 76: ...80 VT G14 VT G21 6 5 4 3 2 1 A B C D E F G H MODEL VT G14 SCHEMATIC DIAGRAM OF TV SECTION CRT and POWER Unit ...
Страница 77: ...81 VT G14 VT G21 6 5 4 3 2 1 A B C D E F G H MODEL VT G14 SCHEMATIC DIAGRAM OF TV SECTION KEY and IF Unit ...
Страница 80: ...86 VT G14 VT G21 6 5 4 3 2 1 A B C D E F G H MODEL VT G21 SCHEMATIC DIAGRAM OF TV SECTION CRT and POWER Unit ...
Страница 81: ...87 VT G14 VT G21 6 5 4 3 2 1 A B C D E F G H MODEL VT G21 SCHEMATIC DIAGRAM OF TV SECTION KEY and IF Unit ...
Страница 85: ...94 VT G14 VT G21 6 5 4 3 2 1 A B C D E F G H BLOCK DIAGRAM OF VCR SECTION Ë SYSTEM CONTROL BLOCK DIAGRAM ...
Страница 86: ...95 VT G14 VT G21 6 5 4 3 2 1 A B C D E F G H BLOCK DIAGRAM OF VCR SECTION Ë SAFETY DEVICE BLOCK DIAGRAM ...
Страница 88: ...98 VT G14 VT G21 6 5 4 3 2 1 A B C D E F G H BLOCK DIAGRAM OF VCR SECTION Ë Y C BLOCK DIAGRAM ...
Страница 90: ...101 VT G14 VT G21 100 12 11 10 9 8 7 6 5 4 3 2 1 A B C D E F G H SCHEMATIC DIAGRAM OF VCR SECTION VCR 1 Unit ...
Страница 93: ...106 VT G14 VT G21 6 5 4 3 2 1 A B C D E F G H PRINTED WIRING BOARD ASSEMBLIES PWB C POWER Unit Wiring Side ...
Страница 94: ...107 VT G14 VT G21 6 5 4 3 2 1 A B C D E F G H PWB F KEY Unit Wiring Side PWB D CRT Unit Wiring Side ...
Страница 95: ...109 VT G14 VT G21 108 12 11 10 9 8 7 6 5 4 3 2 1 A B C D E F G H PWB A MAIN Unit Wiring Side ...
Страница 96: ...111 VT G14 VT G21 110 12 11 10 9 8 7 6 5 4 3 2 1 A B C D E F G H PWB A MAIN Unit Chip Parts Side ...
Страница 98: ...113 VT G14 VT G21 6 5 4 3 2 1 A B C D E F G H Chip Parts Side Wiring Side PWB B TUNER DEF Unit ...