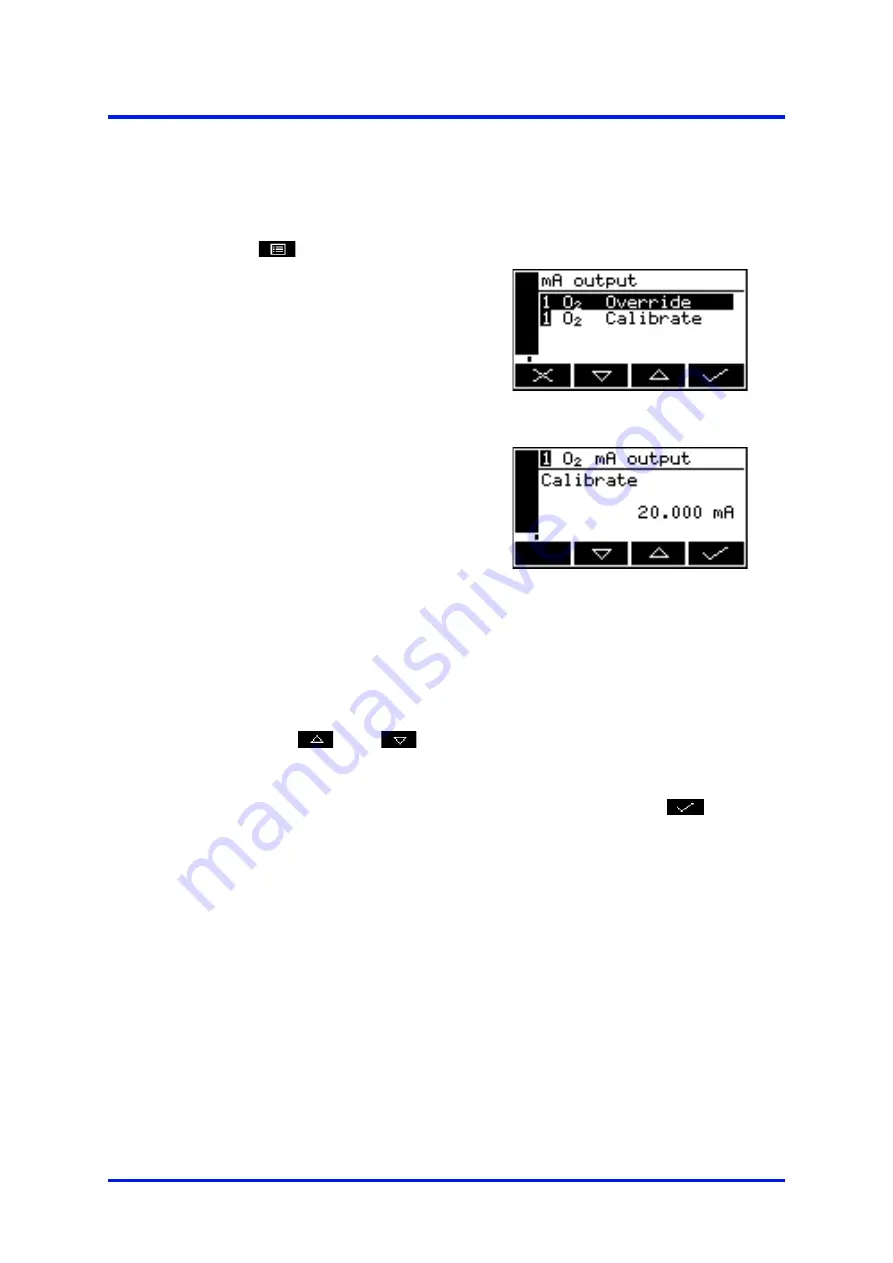
5 – Installation and set-up
MultiExact Gas Analyser
5.7.4 Calibrating the mA output
Use the following procedure to calibrate the mA output:
1.
Select
➞
Service
➞
mA output.
Figure 57 – The mA output
service screen
2.
Select the required 'Calibrate' option.
Figure 58 – The mA output
calibrate screen
3.
As soon as the mA output calibrate screen is shown, the nominal mA output
value is set to 20 mA:
•
Use your control/monitoring equipment (connected to the analyser) to
monitor the actual output value.
•
Use the
and
soft keys to increase or decrease the actual
output value until your control/monitoring equipment indicates 20 mA
output.
4.
When the mA output has been correctly calibrated, press the
soft key:
the mA output service screen (Figure 57) will then be displayed again.
☞
The actual mA output value is controlled from the mA output calibrate screen
as long as the screen is displayed. As soon as the mA service screen is no
longer displayed, the mA output value will be updated to reflect the
corresponding gas measurement.
56
05410001A / Revision 6