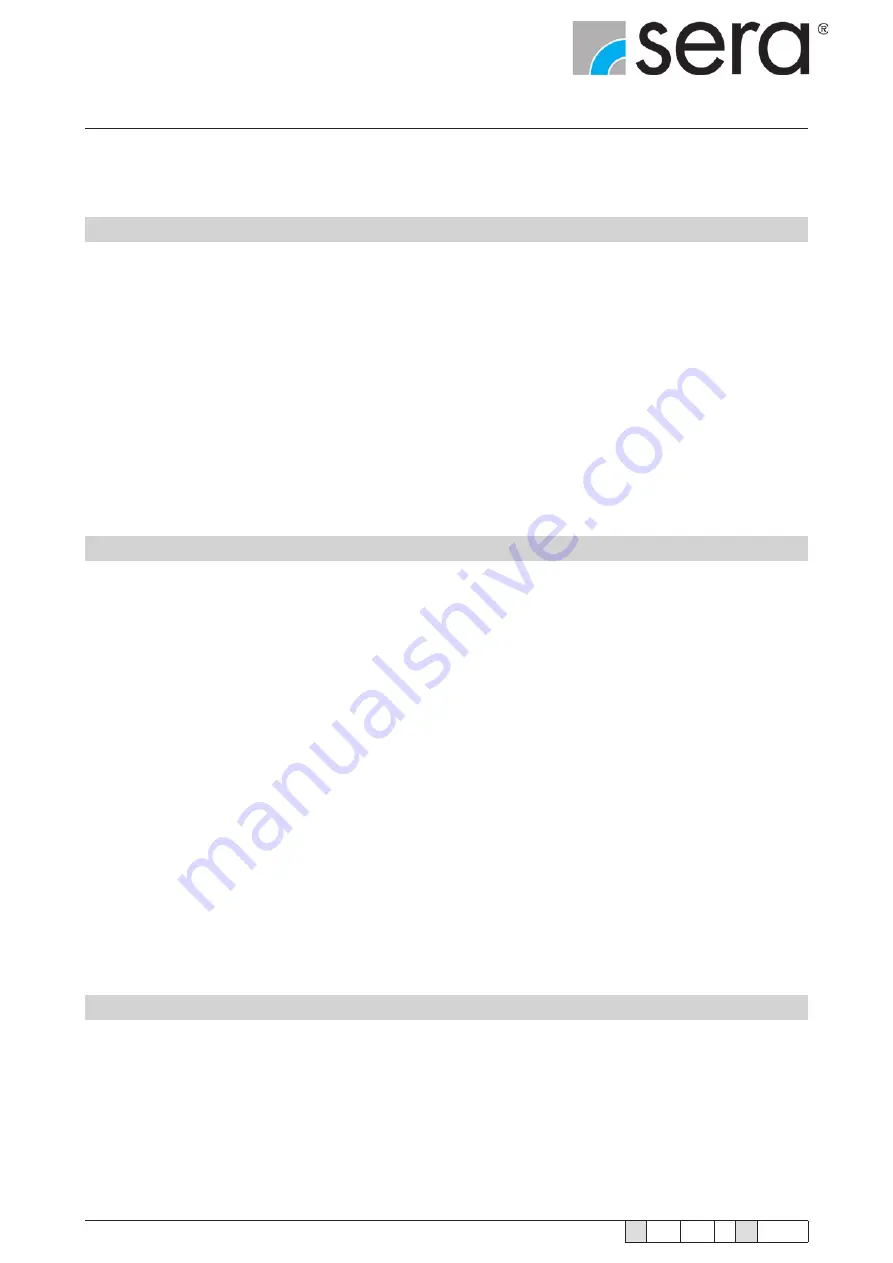
16
www.sera-web.com
Subject to technical modifications!
TA 414
Rev.
11
en 06/2016
Controllable diaphragm pump
C/CS 409.2
Operating instructions
2.11.6 Cleaning
2.11.4 Operation
2.11.5 Maintenance / Repair
■
Control cables too long >> 30m ► malfunctions due to EMC.
■
Control cable and power cable laid in parallel ► malfunctions due to EMC.
■
If the screw-in depth of the setscrew for the integrated overflow valve is not noted, this may lead to dan
-
gerous consequences, i.e. rupture of the pressure pipe or leaking medium. …).
■
Works carried out which are not described in the operating instructions (works on the stroke mechanism and
the assembly pump, electronics opened).
■
Prescribed maintenance schedules ignored.
■
Use of wrong spare parts/oils (e.g. no sera original spare parts, wrong viscosity).
■
Improper mounting of spare and wearing parts (e.g. wrong tightening torque for pump body).
■
Oil level not checked.
■
Use of cables with damaged insulation.
■
No shut down / no protection against a restart before maintenance work.
■
Pumped medium or utilities during an oil change insufficiently removed.
■
Restart without sufficient fastening.
■
Valves confused.
■
Sensor pipes confused.
■
Pipes not connected (e.g. suction- and pressure pipes, gas pipes).
■
Gaskets damaged, medium is leaking.
■
Gaskets not fitted, medium is leaking.
■
Wearing of unsuitable protective clothing / no protective clothing at all.
■
Operation of an uncleaned system.
■
Pumped medium contaminated with oil.
■
Poorly ventilated room.
■
Integrated overflow valve misadjusted.
■
No free return flow of the integrated overflow valve.
■
Fault message ignored ► faulty dosing / process error.
■
Pipes hit, pulsation damper not used ► damage to the pipes, medium is leaking.
■
Pumped medium contains particles or is contaminated.
■
External fuse bridged ► no cut off in case of an error.
■
Ground wire removed ► no cut off by fuse in case of an error, supply voltage directly at the housing.
■
Insufficient lighting of the working place.
■
Suction height too high, pump capacity too low ► process error.
■
Arbitrary modification of the pump (valves, internal fuse, …).
■
No supervision of leakages ► MBE opening.
■
Diaphragm rupture is not indicated when the MBE plug was disconnected. Medium can escape into the envi-
ronment through the vent hole “Danger to the operator and the environment”.
■
Wrong rinsing medium (material changed, reaction with the medium).
■
Wrong cleaning agent (material changed, reaction with the medium).
■
Cleaning agent remains in the system (material changed, reaction with the medium).
■
Protective clothing insufficient or missing.
■
Use of unsuitable cleaning utensils (material changed, mechanical damage by high pressure cleaner).
■
Untrained personnel.
■
Vent openings clogged.
■
Parts torn off.
■
Sensors damaged.