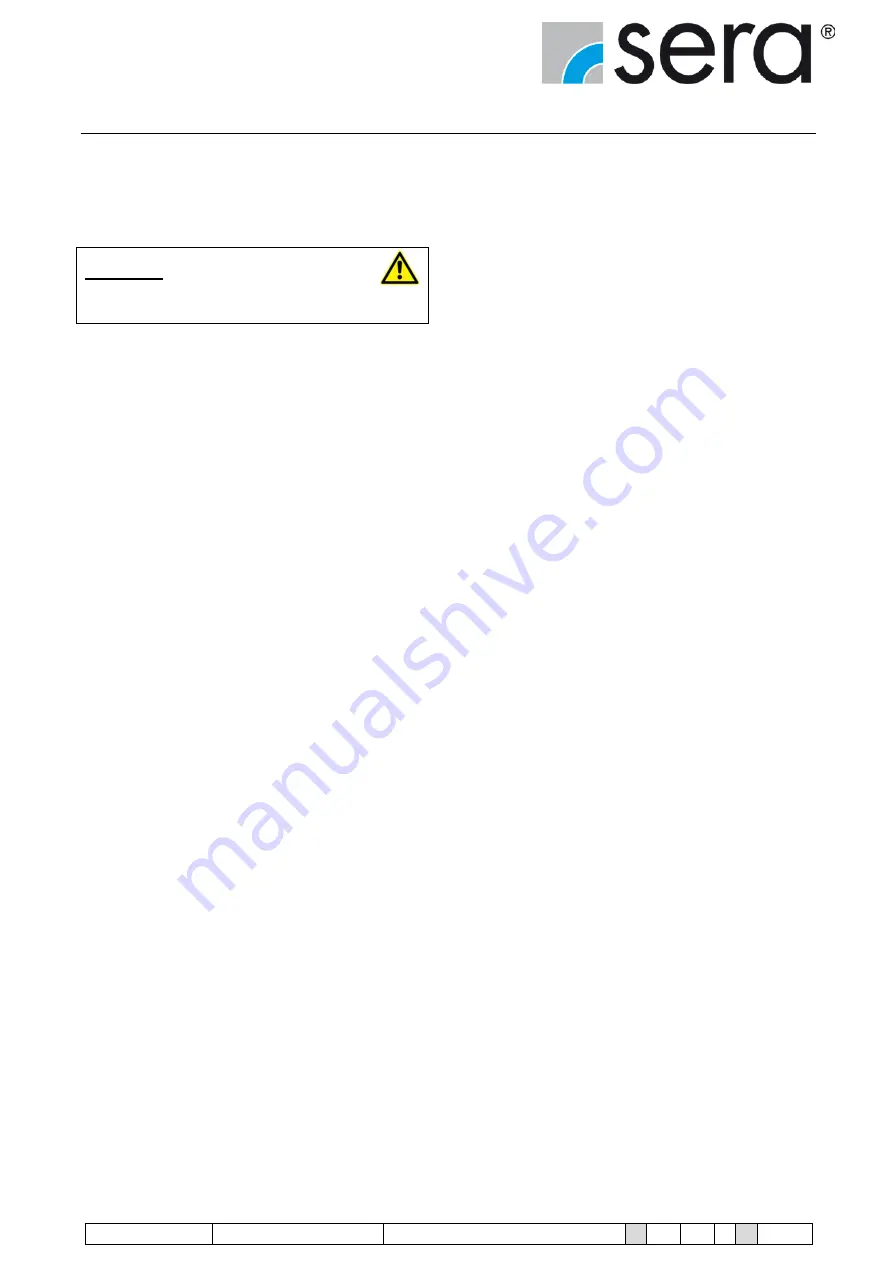
Multi-layer diaphragm pump
Serie 409.2 ML
Operating instruction
34
www.sera-web.com
Technical modifications reserved!
TA 431
Rev.
8 en
06/2015
13
Foreseeable misuse
The following misuse is assigned to the life cycles of the ma-
chine.
CAUTION !
Misuse can result in danger to the operating personnel!
13.1 Transport
•
Tipping behavior during transport, loading and unloading
ignored.
•
Weight for lifting underestimated.
13.2 Assembly and installation
•
Power supply not fuse protected (no fuse/fuse too large,
power supply not conforming to standards).
•
No or improper fastening material of the pump.
•
Improper connection of the pressure pipes, wrong mate-
rial i.e. PTFE tape and unsuitable connection pieces.
•
Liquid pipes confused.
•
Threads overturned/damaged.
•
Pipes bent during connection in order to compensate for
alignment errors.
•
Supply voltage connected without earthed conductor.
•
Socket for safe disconnection of the power supply diffi-
cult to reach.
•
Wrong connecting cables for supply voltage (cross-
section too small, wrong insulation).
•
Parts damaged (e.g. vent valve, flow meter broken off).
•
Wrongly dimensioned pressure and suction pipe.
•
Incorrect dimensioned and improperly fastened pump
panel (panel broken off).
13.3 Start-up:
•
Cover on vent openings (e.g. motor).
•
Suction or pressure pipes closed (i.e. foreign matters,
particle size, stop valves).
•
Start-up with damaged system.
13.4 Operation
•
Fault message ignored
faulty dosing / process error.
•
Pipes hit, pulsation damper not used
damage to the
pipes, medium is leaking.
•
Pumped medium contains particles or is contaminated.
•
External fuse bridged
no cut off in case of an error.
•
Ground wire removed
no cut off by fuse in case of an
error, supply voltage directly at the housing.
•
Suction height too high, pump capacity too low
pro-
cess error.
13.5 Maintenance/Repair
•
Works carried out which are not described in the operat-
ing instructions (works on the stroke mechanism and the
assembly pump, electronics opened).
•
Prescribed maintenance schedules ignored.
•
Use of wrong spare parts/oils (e.g. no
sera
original spare
parts, wrong viscosity).
•
Improper mounting of spare and wearing parts (e.g.
wrong tightening torque for pump body).
•
Oil level not checked.
•
Use of cables with damaged insulation.
•
No shut down / no protection against a restart before
maintenance work.
•
Pumped medium or utilities during an oil change insuffi-
ciently removed.
•
Restart without sufficient fastening.
•
Valves confused.
•
Sensor pipes confused.
•
Pipes not connected (e.g. suction- and pressure pipes,
gas pipes).
•
Gaskets damaged, medium is leaking.
•
Gaskets not fitted, medium is leaking.
•
Wearing of unsuitable protective clothing / no protective
clothing at all.
•
Operation of an uncleaned system.
•
Pumped medium contaminated with oil.
•
Poorly ventilated room.
Содержание 409.2 ML Series
Страница 1: ...a v a i l a b l eu n t i l 3 1 1 2 2 0 1 6...