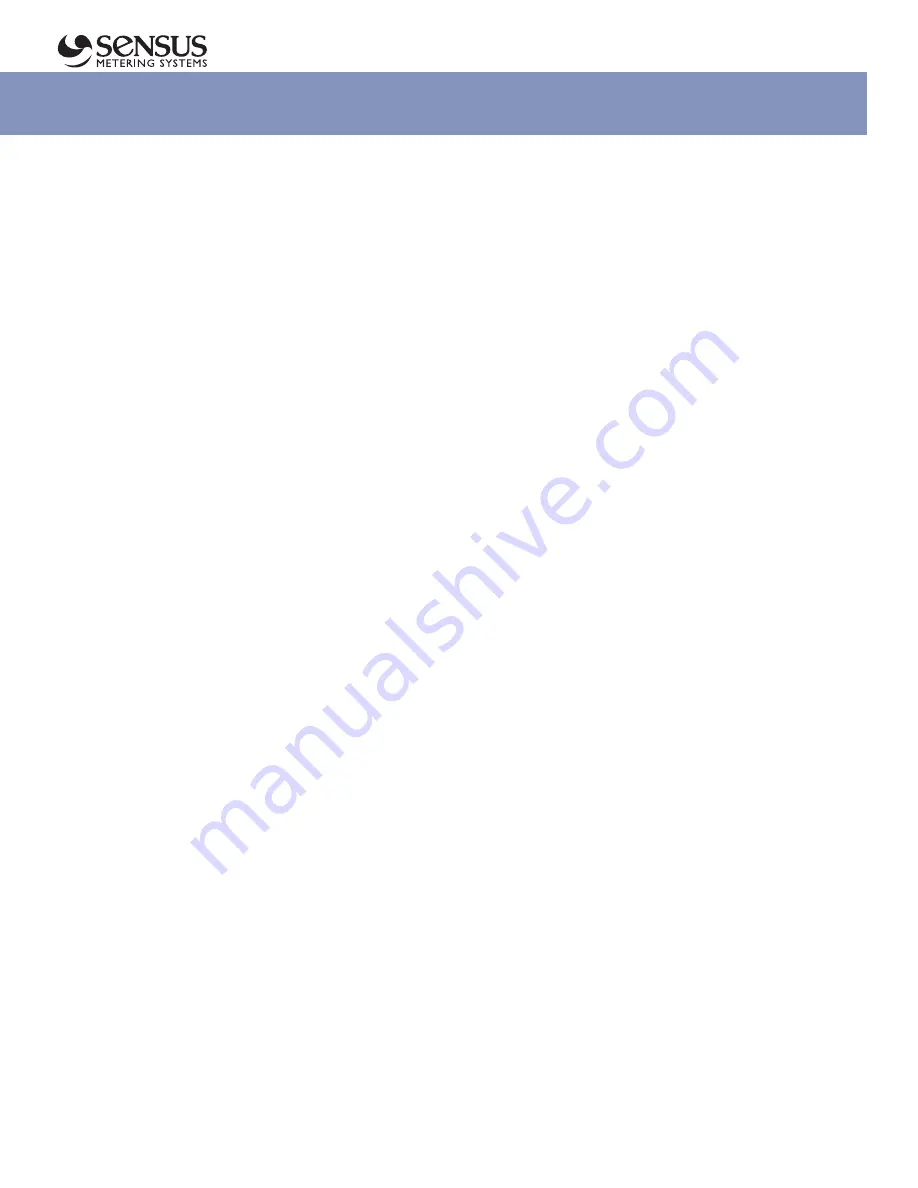
10
Installation and Maintenance
Model 121 Regulators
Servicing – 3/4", 1", 1-1/4"
Back Pressure Models General Instructions
1.
Make sure the regulator is entirely depressured before servicing.
2.
Carefully note location and position of all disassembled parts
to be certain reassembly is correct. Inspect each one carefully
and replace those that are worn or damaged or otherwise
unsatisfactory.
3.
A moderate application of lubricant to O-Ring
13
will help
assure free stem movement and a tight seal. Similar application
of lubricant to the other O-Rings or Tetraseals will help assure
their tightness. Do not use petroleum base lubricants.
4.
Bolted connections should be tightened evenly and firmly.
Carefully tighten diaphragms into place. Bolts must be tight
enough to prevent leakage, but not so tight that the diaphragm
material is crushed or damaged.
5.
Upon completion of servicing, make certain that regulator
installation is entirely free of leaks.
To Service Valve – 15
1.
Remove bolts 29 and remove upper case assembly.
2.
Remove Retaining Ring
16a
.
3.
Remove both halves of valve holder
16b
.
4.
Remove valve
15
(washer
14A
and holder
14B
will likely
remove with the valve. Retain for reassembly).
– To reassemble, replace parts in reverse sequence
.
To Service Main Diaphragm – 11d
1.
Remove top cap
1
, and release and remove adjustment
3
.
On high pressure model remove cap
1a
, release adjustment
3a
,
and remove cover
5
and button
7a
. Mark or measure position
of adjustment
3
or
3a
. Use this to return adjustment to
this setting during reassembly.
2.
Remove spring
9
.
3.
Remove bolts
22
, nuts
23
, and upper case
21
.
4.
Rotate diaphragm assembly
11
counterclockwise
(this unscrews
11h
from
12
) and remove.
5.
To disassemble diaphragm assembly, remove nut
11a
.
Carefully note location and position of all parts to be certain
of correct reassembly. Abrasive side of emery cloth washers
face against diaphragm.
– To reassemble, replace parts in reverse sequence.
Make sure the screwed connection between 11h and 12d is
loose by approximately 1/2 turn.
To do this, carefully rotate
diaphragm assembly
11
clockwise until this screwed connection
bottoms (do not jam it together). Then, back-off diaphragm
assembly
11
counterclockwise approximately 1/2 turn.
The
11h
to
12d
screwed connection must not be tight.
To Service Orifice – 20
1.
Remove top cap
1
, and release and remove adjustment
3.
On high pressure model remove cap
1a
, release adjustment
3a
, and remove cover
5
and button
7a
. Mark or measure
position of adjustment
3
or
3a
. Use this to return adjustment
to this setting during reassembly.
2.
Remove spring
9
.
3.
Remove bolts
38
and bottom cap
37
along with Tetraseal
32
.
4.
Unscrew orifice
20
using 1-5/8" hex socket wrench.
When replacing orifice use a moderate amount of pipe
dope on orifice threads.
– To reassemble, replace parts in reverse sequence.
To Service Seal Diaphragm – 12b
1.
Remove bolts
29
, upper case assembly, and then remove
seal diaphragm, and stem assembly
12
.
2.
To disassemble
12
, screw piston
12a
from stem
12d
.
Use a spanner wrench in notch in skirt of piston
(this can also be done by inserting a standard 7/32"
Allen wrench in the notch).
– To reassemble, replace parts in reverse sequence.
Make certain that fabric side of seal diaphragm
12b
faces
upward and “rubber” side faces downward toward body.
Do not pinch loop in seal diaphragm
12b
between
35
and centerpiece
27
.
Periodic Inspection:
Regulators are pressure control devices with numerous moving
parts subject to wear that is dependent upon particular operation
conditions. To assure continuous satisfactory operation,
a periodic inspection schedule must be adhered to with the
frequency of inspections, determined by the severity of service
and applicable laws and regulations.