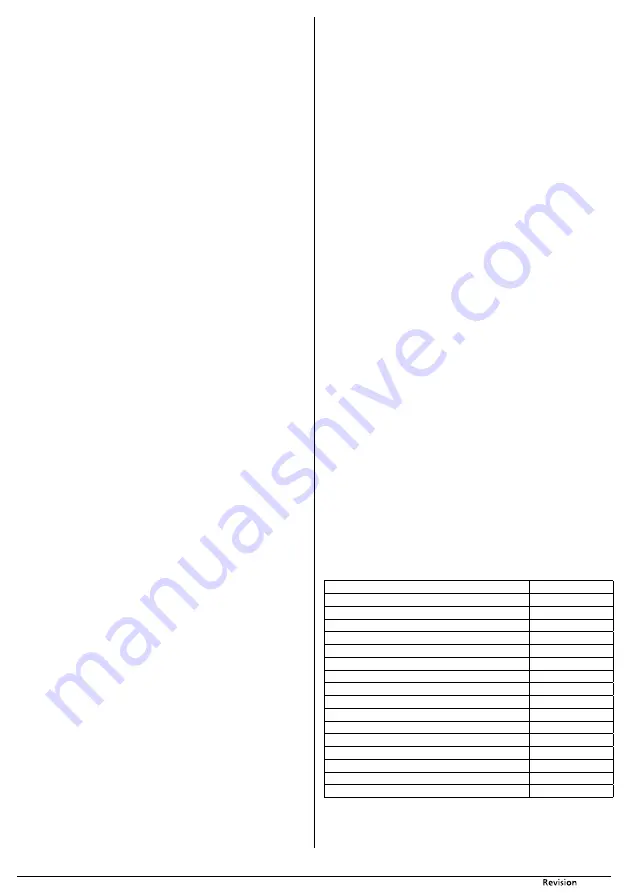
- 11 -
09/2020
Copyright © 2020, Fast ČR, a.s.
It is necessary to ensure that gaskets or sealing materials are not damaged in such
a way that they no longer serve to prevent the entry of a flammable atmosphere. Spare
parts must conform to the manufacturer‘s specifications.
NOTE The use of silicone gaskets and seals may suppress the efficiency of certain
type of leak detection devices. Intrinsically safe components do not need to be
disconnected prior to being worked on.
3. Repairs of intrinsically safe components
No permanently inductive or capacitative load may be placed on the circuit without it
being ensured that thereby the permitted voltage and current for the used appliance
is not exceeded.
Intrinsically safe components are the only type on which it is possible to work in
a flammable environment even while under live current. Testing equipment must have
correct specifications.
Parts are replaced using only parts specified by the manufacturer. Different parts could
result in ignition of refrigerant upon leakage into the environment.
4. Cabling
Check that cabling is not exposed to wear and tear, corrosion, excessive pressure,
vibrations, sharp edges or any other negative environmental effects. This check must
also take into consideration the effects of ageing and permanent vibrations from
sources such as compressors or fans.
5. Detection of flammable refrigerants
Under no circumstances may potential sources of ignition be used for locating or
detecting refrigerant leaks.
A halogen burner (or any other type of detector utilising an open flame) must not be
used.
6. Leak detection methods
The following leak detection methods are considered acceptable for systems
containing flammable refrigerants.
For the detection of flammable refrigerants, electronic leak detectors must be used,
however their sensitivity may not be appropriate or they may require recalibration.
(Detection equipment must be calibrated in an area without any refrigerant present).
It is important to ensure that the detector is not a potential ignition source and that
it is suitable for the used refrigerant. The leak detector must be set to a percentage of
LFL refrigerant and must be calibrated for the used refrigerant and the respective gas
percentage is confirmed (maximum 25 %).
Leak detection liquids are suitable for use on most refrigerants, however, detergents
containing chlorine must be excluded since chlorine may react with the refrigerant
and corrode copper pipes.
In the event of a suspected leak, all open flames must be removed/extinguished.
In the event that the refrigerant leak is found and requires hard soldering, then all
the refrigerant must be drained from the system or separated (by closing a valve) in
a part of the system distant from the leak. The system must then be cleaned out using
oxygen-free nitrogen (OFN) both before as well as after the hard soldering process.
7. Collection and pump discharge
In the event that the cooling circuit is breached due to repairs – or for any other reason
– conventional procedures must be followed. It is, however, important to adhere to the
best method due to flammability. It is necessary to adhere to the following procedure:
■
collect the refrigerant;
■
clean out the circuit using inert gas;
■
pump out;
■
again clean out using inert gas;
■
open the circuit by cutting or hard soldering.
The contents of the circuit must be collected into correct collection cylinders. The
system must be „flooded“ with OFN (oxygen-free nitrogen) for the unit to remain
safe. It may be necessary to repeat the procedure several times. For this task, neither
compressed air nor oxygen may be used.
Flooding may be achieved by disrupting the vacuum in the system with the use of
OFN, and by continued filling until the operating pressure is achieved, then venting
into the atmosphere and finally lowering to a vacuum. This process must be repeated if
refrigerant still remains in the system. When the last OFN cartridge is used, the system
must be ventilated to atmospheric pressure to enable work to be performed. This
activity is absolutely necessary if hard soldering is to be performed on the pipes.
It is necessary to ensure that the vacuum pump outlets are not nearby to any ignition
source, and ventilation must be provided.
8. Filling procedure
Apart from conventional filling procedures, also the following requirements must be
adhered to.
– It is necessary to ensure that no contamination by various refrigerants occurs when
the filling device is used. Hoses or pipes must be as short as possible to minimise the
amount of refrigerant contained inside of them.
– Cylinders must be held vertically.
– It is important to ensure that the cooling system is grounded prior to being filled
with refrigerant.
– When filling is complete, the system must be marked with a label (if it does not have
one already).
– It is necessary to pay extreme care to ensure that the cooling system is not overfilled.
A pressure test using OFN must be performed before refilling the system. In the case
of a leak, the system must be tested after being refilled but also before being put
into operation. A verification test must be performed before leaving the installation
location.
9. Taking out of operation
Prior to performing this procedure it is essential that the technician fully acquaints
him/herself with the device and all its particulars. Correct practice of safely collecting
all refrigerant is recommended. Prior to performing this activity, oil and refrigerant
samples must be taken if an analysis is required prior to using the using the
regenerated refrigerant for the first time. It is essential that prior to starting this activity
that electricity is available.
a) Acquainting one‘s self with the device and its activity.
b) Electrical disconnection of the system.
c) Prior to starting the procedure, ensure that:
■
if required, mechanical device for handling the cylinder with refrigerant is available;
■
all personal protective devices are available and used correctly;
■
the collection process is constantly under the supervision of a competent person;
■
the collection device and cylinders comply with respective norms.
d) Pump out the cooling system if possible.
e) If achieving vacuum is not possible, collection pipes are created to enable the
collection of refrigerant from various parts of the system.
f) Ensure that the cylinder is placed on the scale before the collection of refrigerant is
started.
g)
The collection device is turned on and runs according to the
manufacturer‘s instructions.
h) Cylinders are not overfilled. (No more than 80 % of liquid content capacity).
i) The maximum operating pressure of the cylinder is not exceeded, even temporarily.
j) When the cylinders are properly filled up and the procedure is complete, ensure that
the cylinders and devices are immediately removed from the installation location
and that all the separation valves on the device are closed.
k) The collected refrigerant must not be filled into a different cooling system until it is
cleaned and checked.
10. Marking with a label
The appliance must be marked with a label indicating that it has been put out of
operation and is without refrigerant. The label must be dated and signed. It is ensured
that there are labels on the appliance indicating that it contains flammable refrigerant.
11. Collection
When the refrigerant is collected from the system, either due to servicing or when it is
put out of operation, it is recommended to adhere to proper practice and safely collect
all the refrigerant.
When the refrigerant is transferred into the cylinders, it is necessary to ensure that
appropriate cylinders for collecting refrigerant are used.
It is necessary to ensure that there is a sufficient number of cylinders available to
contain the complete contents of the system. All the cylinders that are to be used must
be intended for collecting refrigerant and be marked with a label for this refrigerant
(i.e. special cylinders for collecting refrigerant). The cylinders must be complete with
a safety valve and associated closing valves in good working condition. The empty
collection cylinders are pumped empty and if possible cooled prior to collecting
refrigerant.
The collection device must be in good operating condition with a set of manuals
relating to the device, which are on hand and it must be suitable for collecting
flammable refrigerants. Apart from this, a set of calibrated scales in good operating
condition must also be available. Hoses must be complete with couplers without
seepage and in good condition. Prior to using the collection device, check that it is in
satisfactory operating condition, has been properly maintained and all the associated
electrical components are sealed to prevent ignition in the event of refrigerant being
released. If in any doubt, consult the manufacturer.
The collected refrigerant must be returned to the refrigerant supplier in the correct
collection cylinder and with a respectively arranged waste transport letter. Refrigerants
are not to be mixed in the collection units and especially not in the cylinders.
In the event that compressors or compressor oils are to be collected, ensure that they
are pumped out to an acceptable level in order to ensure that flammable refrigerant
does not remain in the lubricant. The pump discharge process must be performed
before the compressor is returned to the supplier. To speed up this process, only
electrically heated compressor elements may be used. When the oil is drained from
the system, it must be disposed of safely.
TECHNICAL SPECIFICATIONS
Power supply
220 - 240 V ~ 50 Hz
Dehumidification capacity
10 l / 24 h
Rated input power
340 W
Rated current
1,9 A
Energy factor EEV
1.8 l / kWh
Starting current
5.5 A
Fuse type and current value
T3.15A
Condensate tank capacity
2.1 l
Refrigerant type and weight
R290 / 45 g
GWP (global warming potential)
3
Equivalent CO
2
0.000135 tonnes
Air flow volume
107 m
3
/h (high)
Noise level
54 dB (A)
Dimensions
320 x 215 x 420 mm
Weight net / gross
11.3 / 12 kg
Operating temperature
5 - 32 °C
Recommended room area
16 - 31 m
2
The declared noise emission level of the appliance is 54 dB(A), which represents a level
A of acoustic power with respect to a reference acoustic power of 1 pW.
We reserve the right to change text and technical specifications.