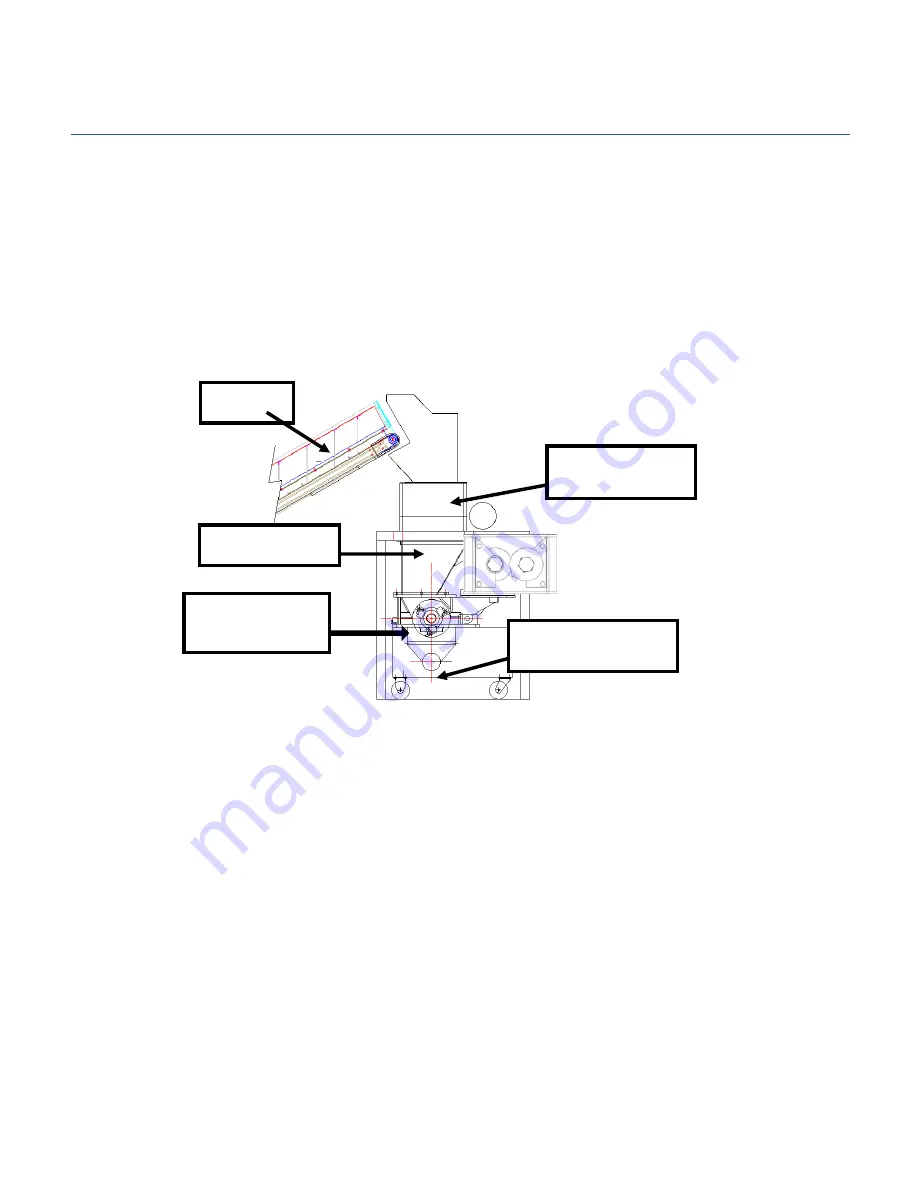
508.366.1488 | www.semshred.com
4
1. Introduction
The Model 3000 dual stage industrial disintegrator is comprised of four basic units:
1.
An inclined conveyor to feed materials on a cleated belt to the feed hopper of the pre- shredder. This
allows for easy loading and control of feed lots as well as operator safety
2.
A first stage pre-shredder, a unit with counter-rotating shafts with cutters turning at low
speed and high torque, for reducing bulk materials.
3.
A second stage disintegrator / knife mill for reduction of shredded bulk into a smaller
particle using interchangeable security screens.
4.
A fan-based waste evacuation unit that conveys the end waste particles through ductwork to
collection bags or a briquettor press system. The air pressure is exhausted through a filter.
General Description
SEM disintegrators are designed to uniformly and consistently reduce the size of waste products through a user
selected sizing screen.
The rotor on which the cutting knives are mounted is a fabricated, steel unit supported by bearings mounted
outside the cutting chamber. The rotor is driven by a motor which is capable of producing high torque loads.
The disintegrator is equipped with a magnetic starter that is protected by manually resettable overload
heaters. The slanted rotor knives and counter slanted bed knives produce a scissor cutting action which
reduces the possibility of feedstock jamming in the cutting chamber.
Motors have overload heaters for maximum protection in compliance with the NEC.
The control enclosure houses all of the necessary wiring, circuit breakers, overload heaters, and motor
starter coils, along with the 115V control transformer and disintegrator operating controls. The control
enclosure is built to meet NEC regulations.
First Stage Cutting
Chamber
Second Stage
Cutting Chamber
Waste Material
Evacuation
Conveyor
Mid-Hopper