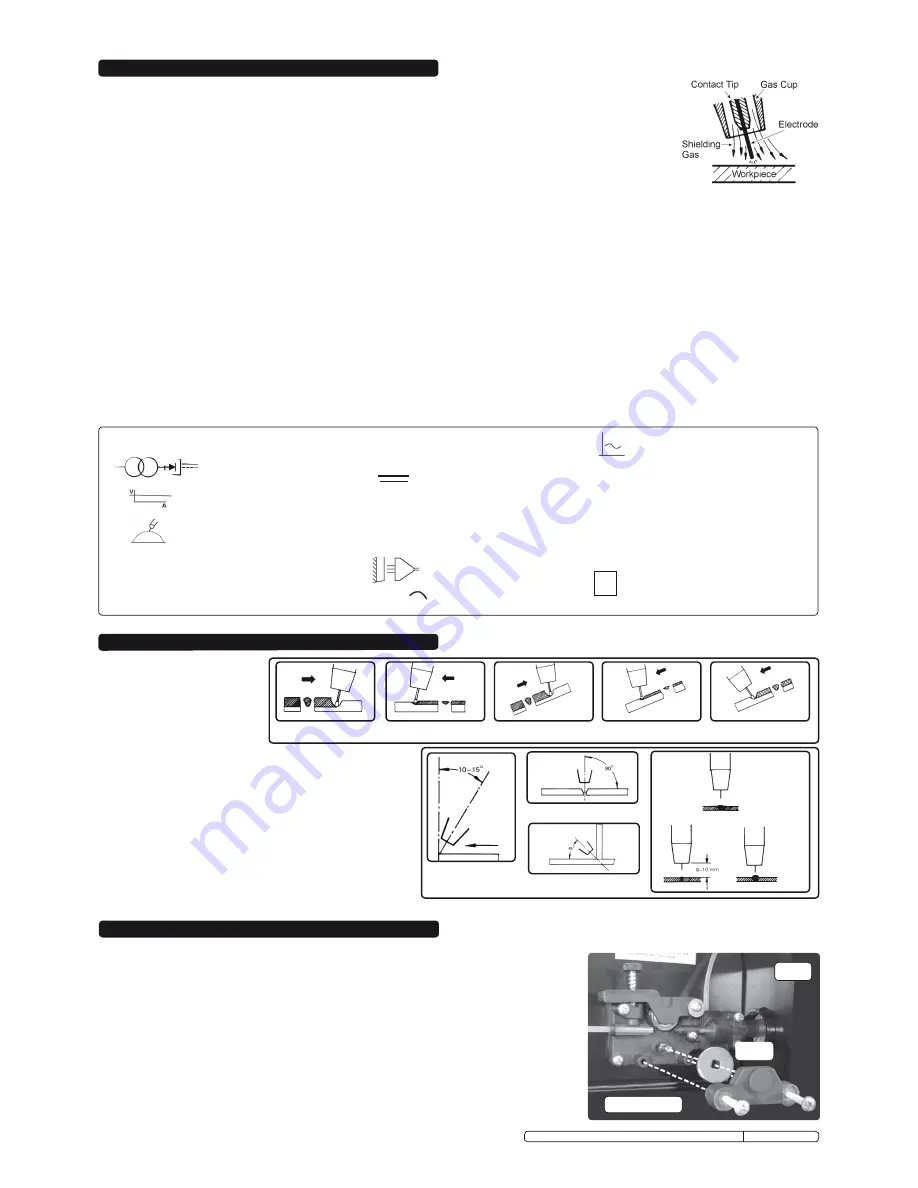
Alternating current & the rated
frequency in hertz i.e. 50hz
P
max
... kW
Maximum power consumption in case
of a rotating welding power source. This
value will only be given when it is not
combined with a prime mover.
U
1
... V/...hz
Rated values of the supply voltage
and the frequency.
/
1
Rated supply current.
IP
Degree of protection, i.e. 21 or 23.
Welding power sources which are suitable
for supplying power to welding operations
carried out in an environment with increased
hazard of electric shock.
s
6. 1.
Wire feed unit
Check the wire feed unit at regular intervals. The feed roller wire guide plays an important part in
obtaining consistent results. Poor wire feeding affects welding. Clean the rollers weekly, especially
the feed roller groove, removing all dust deposits.
6. 2.
Torch
Protect the torch cable assembly from mechanical wear. Clean the liner from the machine forwards
by using compressed air. If the liner is clogged it must be replaced.
6. 3.
Turning or Changing the Feed Roller
IMPORTANT:
Adjust the feed roller to the corresponding wire size.
There are two grooves on the feed roller, 0.6mm and 0.8mm. Always use the groove on the
outside of the roller, (the groove nearest to you). To remove the feed roller, undo the two screws
and remove the plastic cover (fig 7). Clean and turn, or if damaged change the feed roller and
replace plastic cover accordingly.
6. MAINTENANCE
MEANINGS OF MARKINGS, ANd SYMBOlS
Single-Phase transformer
Flat Characteristic
MIG/MAG welding
...A/ ... V to ...A/ ... V
Range of output, rated min
& max welding current and
their corresponding conventional
load voltage.
Rated on-load voltage
u
°
in
V
a) Peak value in case of direct current;
b) Peak & r.m.s. value in case of alternating current.
Direct current
X
Duty cycle (Factor)
1
2
Rated weld current
U
2
Conventional load voltage
Mains supply and number of phases
(i.e. 1 or 3) with symbol for
alternating current.
(1)3
4.1.
Mig/Mag Welding.
A spool of welding wire is positioned on the welder’s spool holder and automatically fed through an insulated liner in the
torch to the tip. The torch assembly consist of a switch, liner, gas hose, and control cable. The switch activates the wire
feed roller and the gas flow. Conversely, releasing the switch stops the wire feed and gas flow. The weld current is
transferred to the electrode (the wire) from the contact tip at the end of the torch. A gas cup fits over the contact tip to
direct the gas flow towards the weld ensuring that the arc welding process is shielded from oxidising air contaminates.
The shielding gas also assists heating of the weld materials.
The torch is connected to the positive side of a DC rectifier, and the negative clamp is attached to the workpiece.
4.2.
Spot Welding.
Remove the gas cup and fit a spot welding gas cup (120/722150). Turn the voltage to the highest setting allowed by your machine. Drill a small hole in
the top plate. Push the spot gas cup onto the material to be welded. The castelations on the cup keep it the correct distance from the weld pool and
allow you to push the two pieces being welded together. Press the torch trigger and hold it for 2 to 3 seconds. The wire will feed through during the
allotted time and create the weld.
4.3.
Preparation for Welding.
IMPORTANT:
BEFORE YOU COMMENCE, MAKE SURE THE MACHINE IS SWITCHED OFF AT THE MAINS. IF WELDING A CAR, DISCONNECT
THE BATTERY OR FIT AN ELECTRONIC CIRCUIT PROTECTOR. WE RECOMMEND THE USE OF SEALEY PROSAF/12V OR 24V IN ORDER TO
PROTECT SOPHISTICATED ELECTRONICS. ENSURE YOU HAVE READ AND UNDERSTOOD THE ELECTRICAL SAFETY INSTRUCTIONS IN
CHAPTER 1.
4.3. 1.
Connecting the Earth Lead
To ensure a complete circuit, the earth lead must be securely attached to the work piece that is to be welded.
a) Best connection is obtained by grinding the point of contact on the workpiece before connecting clamp to the workpiece.
b) The weld area must also be free of paint, rust, grease, etc.
c) If welding a vehicle, disconnect the battery or fit a PROSAF/12 “Electronic Circuit Protector” available from your Sealey dealer.
4.3. 2.
Wire feed switch controls the speed of the wire feed. In principle, the lower the amperage number the slower the wire speed.
4.3. 3.
To weld mild steel, CO2 gas is suitable for most tasks where spatter and the high build up of weld do not pose a problem.
To achieve a spatter free and flat weld however,
you must use an
Argon/CO2 mixture.
4.3. 4.
To weld aluminium use:
Argon gas,
0.8mm contact tip (AK957),
0.8mm aluminium wire, (MIG/2/KAL08).
Note: Ensure you feed the wire through the correct sized groove in the feed roller (see section 6.3).
4. WEldING PRINCIPlES & PREPARATION
5. WEldING
1. Direction of
Welding
4. Fillet Weld
3. Butt Weld
Normal
Welding
Arc
Short
Welding
Arc
Long
Welding
Arc
IMPORTANT.
Should you have no welding
experience, we recommend you seek
training from an expert source to
ensure your personal health & safety.
You must familiarise yourself with
welding applications and limitations,
and specific potential hazards
peculiar to welding. Good Mig welding may be achieved only with
continued, supervised practice.
For example: Correct torch angle and direction of travel in relation to
the workpiece is essential for the appearance and quality of the weld.
Illustrations demonstrate various positions and directions.
Rightward Welding
Leftward Welding
Vertical Rightward
Downhard leftward
Down Rightward
Welding with a long arc reduces penetration and widens the arc. This
in turn results in more spatter. A long welding arc can be appropriate
for welding butt joints in thin materials. Welding with a short arc
(at the
same weld settings
) results in greater penetration and a narrower
weld and reduces the amount of spatter.
We recommend expert training and supervised practice.
Fig 7
Plastic cover
Roller
Original Language Version
SUPERMIG150.V2, SUPERMIG160.V2, SUPERMIG180.V2 Issue: 3 - 09/04/10