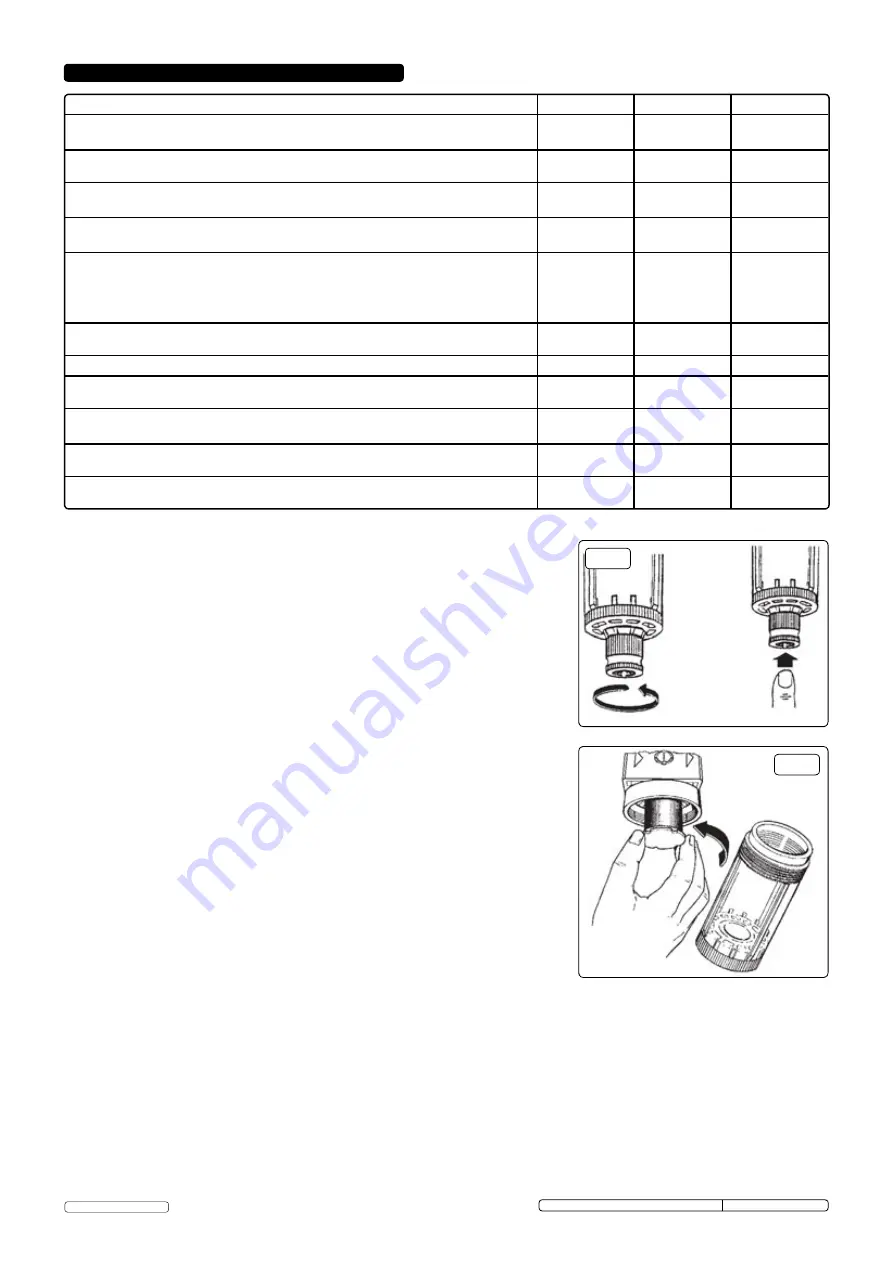
WARNING!
Before performing any maintenance operation, switch off the
compressor, disconnect from electricity supply and release all air from the tank
(except where a pressurised system is needed). In order to keep the compressor in
good working condition, periodical maintenance is essential.
6.1
Oil Replacement
6.1.1 remove the oil filler cap (fig.1a) and unscrew sight glass (fig.1B), draining the oil
into a container. Drain when the compressor is hot so that oil drains rapidly and
completely. Incline compressor to ensure complete drainage.
replace sight glass and refill. Do not overfill. replace filler cap (fig.1a).
6.1.2 recommended oil for compressors:
synthetic oil suitable for temperatures ranging from -5°c to 45°c, viscosity 5W50.
We do not recommend using mineral oil in these compressors.
Part No. Qty.
Description
fso1
1ltr x 12 compressor oil - fully synthetic
fso1s
1ltr x 1 compressor oil - fully synthetic
fso5
5ltr x 1
compressor oil - fully synthetic
WARNING! Never mix different oils and do not use non-detergent/low quality
oils as the compressor may be damaged.
Dispose of waste oil only in accordance with local authority requirements.
6.2
IMPORTANT WARNING
- air contaminants taken into the compressor will affect
optimum performance. Example: Body filler dust or paint overspray will clog the pump
intake filter and may cause internal damage to pump/motor components. Please note
that any parts damaged by any type of contamination will not be covered by warranty.
6. MAINTENANCE
Maintenance Procedure
Once a Week
Once a Month
Once a Year
check the oil level is in the middle of the sight glass. add more synthetic compressor
oil if needed.
4
Drain the water collected in the air outlet filter. To be done under pressure (fig.6).
4
Drain the condensation that has collected in the air tank. Pressurise the tank, tip the
tank forward and open the drain tap.
4
Check all connections, pressure hose wear, all fixing are tight and all electrical
connections are secure and clean.
4
check the condition of the air filter (fig.1). If necessary remove the filter element and
clean by blowing through with an air line at low pressure, from the clean side or wash
in soapy water, rinse and dry. Do not operate the compressor without the filter as
foreign bodies or dust could seriously damage the pump.
Every 3 months
clean the compressor to prevent overheating.
4
Replace the cartridge in the outlet filter (fig.7).
Every 6 months
check the automatic cut-out at max. pressure and the automatic cut-in at 2 bar below.
4
Check the filter reducer and its parts to
optimise efficiency.
4
check the safety valve - pull the ring when the tank is pressurised.
4
replacement of oil. see instructions below.
4
fig.7
fig.6
Original Language Version
ssQc0903P, ssQc2405P, ssQc2409 Issue: 3 (sP) - 22/07/13
© Jack sealey limited