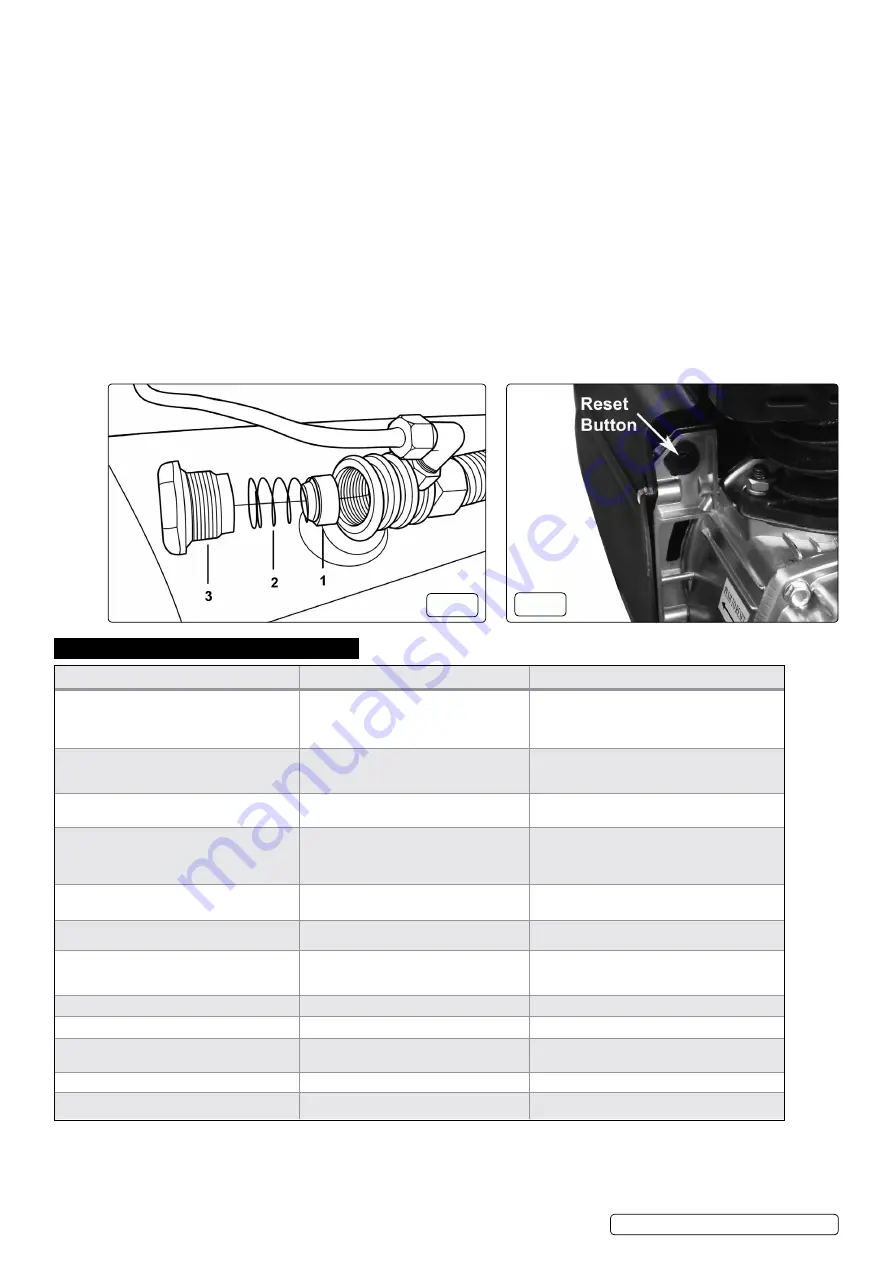
7.4.
OPERaTIONS TO BE CaRRIED OUT EVERY 200 HOURS:
a)
Replace the lubricating oil. For oil specifications see below. Remove the oil filler plug (fig.2A) and undo the drain bolt (fig.2C), draining
the oil into a container. Drain when the compressor is hot so that oil drains rapidly and completely. Incline compressor to ensure complete
drainage. Replace the drain bolt and refill with fresh oil through the filler aperture.
DO NOT
overfill. Replace plug (fig.2A).
Recommended oil for compressors, Suitable for room temperatures ranging from +5ºC to +25ºC. SEALEY CPO or equivalent SAE 40
compressor oil.
Room temperature below +5ºC: SAE 20 compressor oil.
WaRNING!
Never mix different oils and do not use non-detergent/low quality oils as the compressor may be damaged. Dispose
of waste oil only in accordance with local authority requirements.
b)
Check the automatic cut-out at max. pressure and the automatic cut-in at 2 bar below.
7.5.
OPERaTIONS TO BE CaRRIED OUT EVERY 500 HOURS:
a)
Replace air filter.
b)
Check all tube fittings and electrical connections.
IMPORTaNT! Failure to carry out maintenance tasks may invalidate the warranty on your compressor.
Inspection of pressure tank both inside and out.
7.6.
Under the
PRESSURE SYSTEMS SaFETY REGULaTIONS 2000,
it is the responsibility of the owner of the compressor to initiate a
system of inspection that both defines the frequency of the inspection and appoints a person who has specific responsibility for carrying
out the inspection.
IMPORTaNT WaRNING
- Air contaminants taken into the compressor will affect optimum performance. Example: Body filler dust or
paint overspray will clog the pump intake filter and may cause internal damage to pump/motor components. Please note that any parts
damaged by any type of contamination will not be covered by warranty.
8. TROUBLESHOOTING
FaULT
CaUSE
REMEDY
1A) Pressure drop in the tank
Air leaks at connections
Run compressor to max. pressure, switch off
Brush soap solution over connections and look for
bubbles. Tighten connections showing leaks
If problem persists contact Authorised Service Agent
1B) Pressure drop in the tank
Air leaks from safety valve
Operate the safety valve manually by pulling on the
ring. If valve continues to leak when in the closed
position it should be replaced
1C) Pressure drop in the tank
Air leaks from cylinder head gasket
Check tightness of head bolts. If leak continues
contact Authorised Service Agent
2) Pressure switch valve leaks when
compressor is idle
Non-return valve seal defective
Empty the air tank. Referring to fig.6, remove the
non-return valve cap (3), spring (2) and seal (1)
Clean the seal and its seat, or if necessary replace
the seal
3) Air leaks from tank body or tank welds
Internal corrosion caused by infrequent tank
draining or non permitted modifications to tank
Tank could rupture or explode. Cannot be repaired
DISCONTINUE USE IMMEDIaTELY
4A) motor stops and will not restart
Thermal cut out has operated
Allow unit to cool for 30 minutes, then press reset
see fig.7.
4B) motor stops and will not restart
Supply fuse has tripped
Reset fuse and restart unit. If repeated tripping
occurs replace the check valve or contact
authorised service agent
5) Compressor stops and does not restart
motor failure
Contact Authorised Service Agent
6A) Compressor does not stop at max. pressure Pressure switch fault
Contact Authorised Service Agent
6B) Compressor does not stop at max. pressure Filter clogged
Head gasket or valve fault
Replace filter element.
Contact Authorised Service Agent
7) Compressor noisy with metallic knock
Bearing or piston damage
Contact Authorised Service Agent
8) Excessive moisture in discharged air
High humidity environment
Drain tank after each use
Original Language Version
© Jack Sealey Limited
SAC5020E110V.V3 | Issue:1 14/06/19
fig.6
fig.7