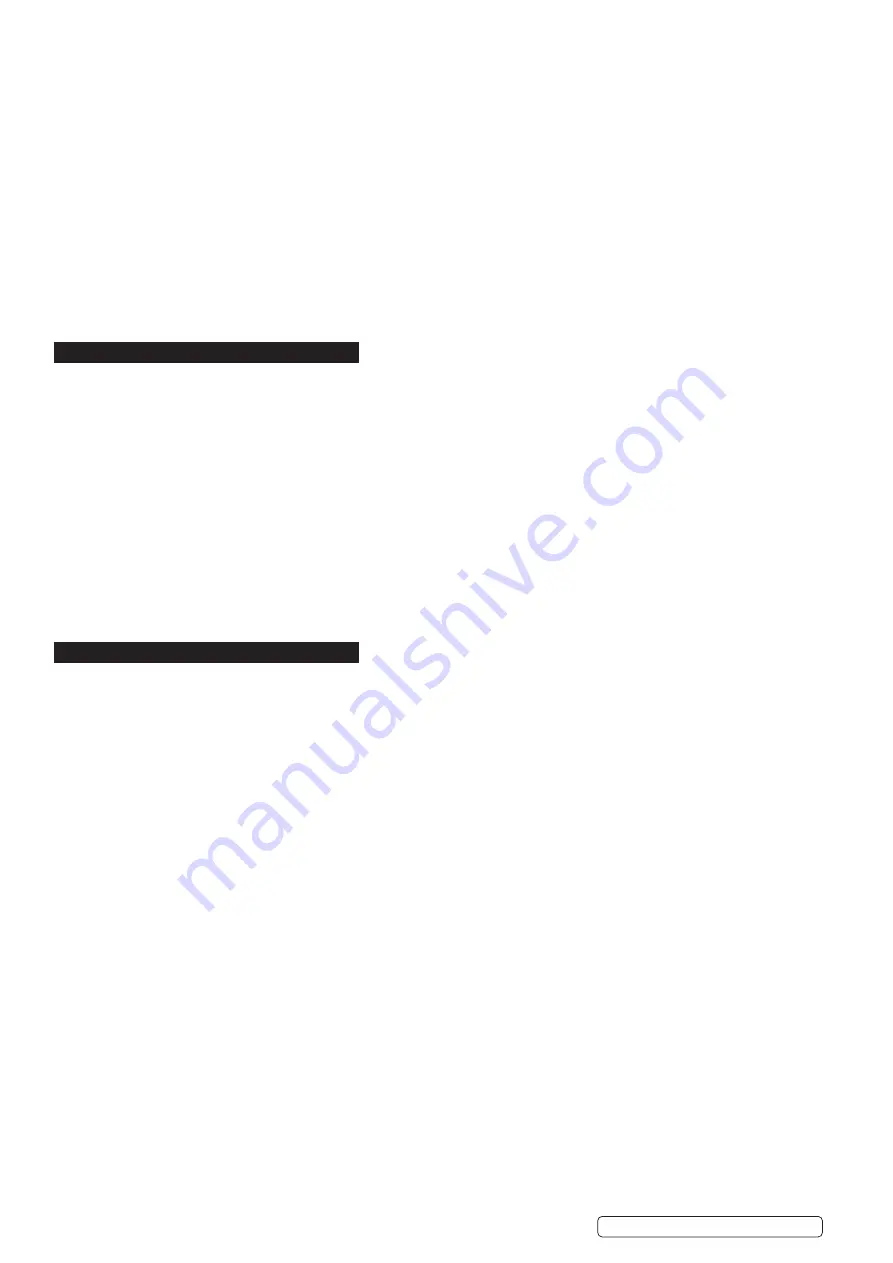
5.6.1.
Remove oil tank dipstick (fig.1.12) and wipe it with a clean cloth.
5.6.2.
Replace and re-tighten the dipstick.
5.6.3.
Remove the dipstick again and check the oil level. It should be at the top of the full (H) indicator on the dipstick.
5.6.4.
If low, add oil slowly into the oil tank.
DO NOT
overfill. After adding oil, wait one minute and then recheck the oil level.
5.6.5.
Replace and re-tighten the dipstick.
5.7.
ADDING FUEL
9
Fill the fuel tank outdoors or in well-ventilated areas.
9
Make sure there is enough fuel in the fuel tank before operating the pressure washer.
9
Use only clean, fresh, unleaded fuel. Use a minimum of 87octane/87 AKI (91 RON).
9
Keep fuel away from sparks, open flames, pilot lights, heat, and other ignition sources.
9
Check fuel hoses, tank, caps, and fittings frequently for cracks or leaks. Replace if necessary.
9
If fuel spills, wait until it evaporates before starting engine.
8
DO NOT
use old petrol, and
DO NOT
mix oil with petrol.
5.7.1.
Stop the engine (Section 5.3 Shut Down Procedure) and let it cool at least two minutes before removing the fuel tank cap (fig.1.5).
5.7.2.
Clean the fuel cap area of dirt and debris. Remove the fuel tank cap and make sure the fuel filter is in place.
5.7.3.
Fill the fuel tank (fig.1.15
) with fuel. Never overfill the fuel tank. Fill tank to no more than ½″ (13 mm) below the bottom of the filler neck
to provide space for expansion caused by the engine heat.
5.7.4.
Replace the fuel tank cap.
6. MAINTENANCE - WASHER
WARNING!
Maintenance should only be performed with the engine turned off, the spark plug cap removed and the unit disconnected
from the mains water supply.
6.1.
WINTER STORAGE
6.1.1.
Fill the pump with an antifreeze mixture before storing in a frost free, safe, dry area for the winter. Introduce the antifreeze by the following
method.
1.
Shut off the water supply and disconnect the supply hose. Relieve pressure within the pump by squeezing the gun trigger. Remove the
high pressure hose and let all water drain from it. Hold gun/lance with nozzle downwards and pull trigger until all water has drained out.
2. Disconnect the ignition lead from the spark plug.
3. Connect a short length of garden hose to the water inlet and using a funnel pour an antifreeze mixture into it.
4. Pull the recoil starter several times to circulate the antifreeze through the pump. Continue to add antifreeze and pull the recoil until
antifreeze is expelled from the pump.
6.2.
CLEANING WATER INLET FILTER
WARNING!
DO NOT
operate this pressure washer without the water inlet filter in place, as deposits could build up internally and
affect the functioning of the unit.
6.2.1.
This pressure washer is equipped with a water inlet filter.
6.2.2.
The water inlet filter must be kept clean at all times, otherwise it can restrict the water flow to the pump unit and damage it.
6.2.3.
Remove the quick-connect coupler from the water inlet, then carefully remove and clean the water inlet filter.
7. MAINTENANCE - ENGINE
7.1.
Change engine oil after the first 8 hours of operation. Thereafter, change oil monthly or every 50 hours of operation. Change oil more
often if engine is operated under heavy load, or in high ambient air temperatures. During normal operation, partially burned fuel, small
particles of metal from the cylinder walls, pistons, bearings and combustion deposits will gradually contaminate the oil. If the oil is not
changed regularly, these foreign particles can cause increased friction and a grinding action which shortens the life of the engine. Fresh
oil also assists in cooling. Old oil gradually becomes thick and loses its cooling ability as well as its lubricating qualities.
7.2.
CHECKING THE OIL LEVEL.
Ensure the unit is on a level surface.
7.2.1.
Unscrew the dipstick (fig.5) and wipe it clean of oil. Note that the maximum oil level should be just below the opening of the filler neck.
7.2.2.
Check the oil level by seating the dipstick into the hole without screwing it in. If there is no oil on the dipstick when it is removed the level
is too low and should be topped up immediately with an SAE10W - 30 oil.
7.2.3.
Top up oil if necessary and recheck level.
7.2.4.
Screw dipstick fully home to seal oil fill hole.
7.3.
DRAINING ENGINE OIL
7.3.1.
The engine oil should be replaced after the first 20 hours of operation, or after the first month of use. After that, it should be replaced
every 100 hours or every six months.
7.3.2.
To drain the engine oil:
1. Loosen the oil tank dipstick (fig.1.12).
2. Place an oil container underneath the opening at the base of the filler tube.
3. Remove the hex screw plug from the oil drain (fig.5) and drain the oil into the container.
4. Once the oil has been completely drained, replace the hex screw (fig.5) and oil tank dipstick.
7.4.
CHECKING AIR FILTER
IMPORTANT:
Clean air filter (fig.1.8) element after every 50 hours of use (every 10 hours under dusty conditions).
7.4.1.
To access the air filter element rotate cover (fig.1.8) anti-clockwise and remove the foam filter from the air intake base moulding.
7.4.2.
Wash the foam element with a household detergent or a high flash-point solvent and squeeze dry. When the element is thoroughly dry soak
it in clean engine oil. Squeeze out any excess oil, fit back over the air intake base moulding, locate and replace cover.
7.4.3.
The foam element should be replaced after every 300 hours of service.
7.5.
INSPECTING, REPLACING OR CLEANING THE SPARK PLUG
NOTE:
The spark plug should be checked after every 100 hours of operation or every six months.
7.5.1.
To replace or clean the spark plug:
1. Disconnect the spark plug wire by pulling it off the spark plug.
2. Using provided spark plug wrench, remove the spark plug by turning it counter-clockwise. If there is a carbon sediment build-up,
remove it. If there is too much carbon sediment, replace the spark plug.
3. Check the gap with a wire gauge. If necessary, reset the gap to 0.7-0.8 mm. Install and tighten the spark plug to the recommended
torque – 180 lb/in (20 Nm).
4. Reinstall the spark plug wire and protection cage in reverse order.
Original Language Version
© Jack Sealey Limited
PWM1300.V2 Issue 2 (2) 07/12/20