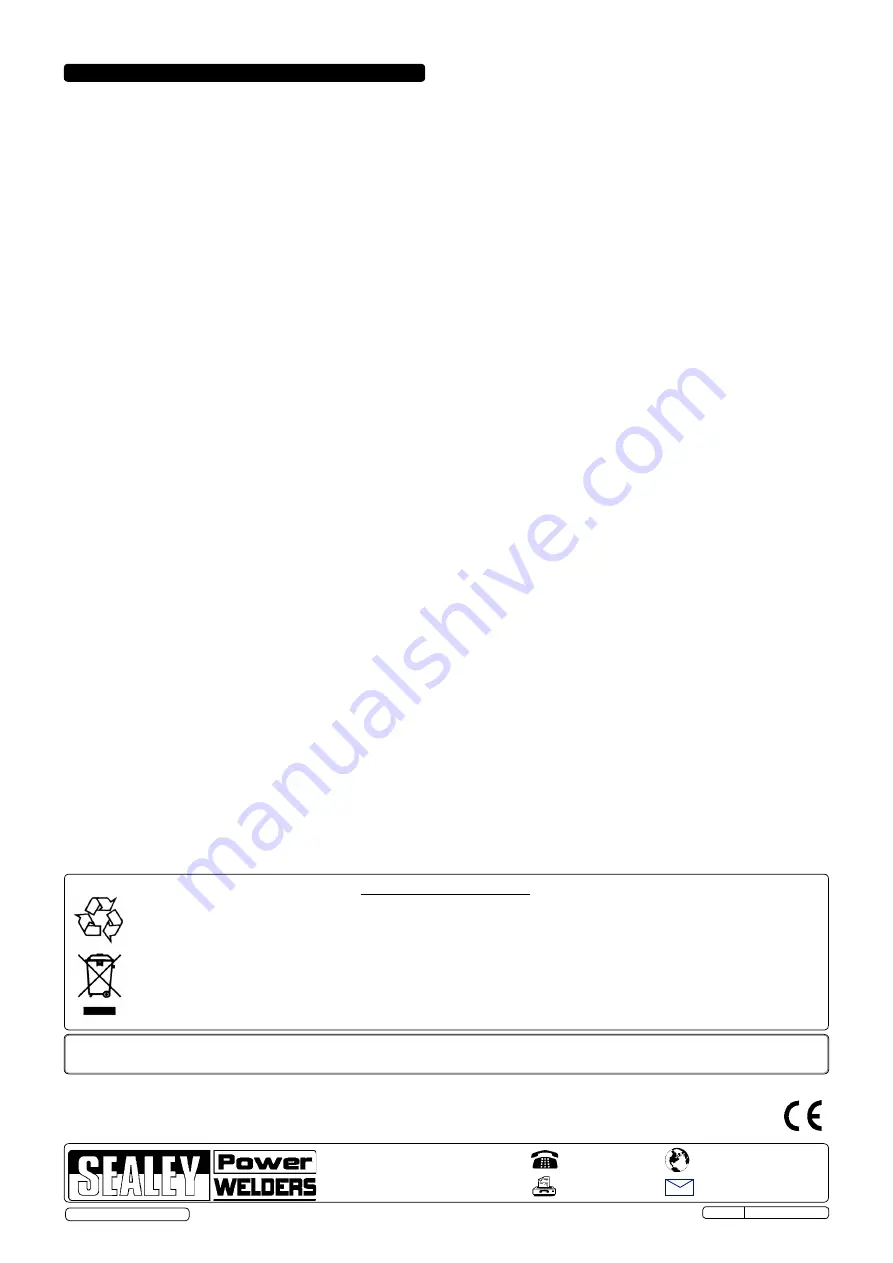
10. ELECTROMAGNETIC COMPATIBILITY
10.1.
THIS EQUIPMENT IS IN CONFORMITY WITH THE EUROPEAN STANDARD ON THE ELECTROMAGNETIC COMPATIBILITY
OF ARC WELDING EQUIPMENT AND SIMILAR PROCESSES (e.g. ARC AND PLASMA CUTTING)
10.2.
Protection against interference. (E.M.C.)
The emission limits in this standard may not, however, provide full protection against
interference to radio and television reception when the equipment is used closer than 30m to the receiving antenna. In special cases,
when highly susceptible apparatus is being used in close proximity, additional mitigation measures may have to be employed in order
to reduce the electromagnetic emissions. At the same time there could occur some potential difficulties in having electromagnetic
compatibility in a non-industrial environment (e.g. in residential areas). Therefore it is most important that the equipment is used and
installed according to the following instructions.
10.3.
Installation and use.
The user is responsible for installing and using the equipment according to these instructions. If electromagnetic
disturbances are detected, then it shall be the responsibility of the user of the equipment to resolve the situation with the technical
assistance of the supplier. In some cases this remedial action may be as simple as earthing the circuit (see
Note:
). In other cases it
could involve constructing an electromagnetic screen, enclosing the welding power source and the work, complete with associated
input filters. In all cases the electromagnetic disturbances shall be reduced to the point where they are no longer troublesome.
Note:
The welding/cutting circuit may or may not be earthed for safety reasons. Changing the earthing arrangements should only be
authorised by a person who is competent to assess whether the changes will increase the risk of injury, e.g. by allowing parallel
welding/cutting circuit return paths which may damage the earth circuits of other equipment. Further guidance is given in IEC 974-13
’Arc Welding Equipment - Installation and Use.’
10.4.
Assessment of area.
Before installing the equipment the user shall make an assessment of potential electromechanical problems in
the surrounding area. The size of the surrounding area to be considered will depend on the structure of the building and other
activities that are taking place. The surrounding area may extend beyond the boundaries of the premises.
The following shall be taken into account:
a) Other supply cables, control cables, signalling and telephone cables, above, below and adjacent to the welding equipment.
b) Radio and television transmitters and receivers.
c) Computer and other control equipment.
d) Safety critical equipment, e.g. security monitoring of industrial equipment.
e) The health of people in the vicinity, e.g. persons fitted with a pacemaker or hearing aid.
f) Equipment used for calibration or measurement.
g) The immunity of other equipment in the environment. The user shall ensure that other equipment being used in the environment is
compatible. This may require additional protective measures.
h) The time of day that welding and other activities are to be carried out.
10.5.
Mains supply.
The equipment should be connected to the mains supply according to these instructions. If interference occurs, it may
be necessary to take additional precautions such as filtering of the mains supply. Consideration should also be given to shielding the
supply cable of permanently installed equipment in metallic conduit or equivalent. This shielding should be connected to the power
source so that good electrical contact is maintained between the conduit and the welding power source enclosure.
10.6.
Maintenance of the equipment.
The equipment should be routinely maintained according to these instructions. All access and
service covers should be closed and properly fastened when the welding equipment is in operation. The welding equipment should not
be modified in any way except for those changes and adjustments covered in these instructions. In particular, the spark gaps of any
arc striking and stabilising devices should be adjusted and maintained according to the instructions.
10.7.
Cables.
The welding/cutting cables should be kept as short as possible and should be positioned close together, running at or close
to the floor level.
10.8.
Equipotential bonding.
Bonding of all metallic components in the welding/cutting installation and adjacent to it should be considered.
However, metallic components bonded to the workpiece will increase the risk that the operator could receive a shock by touching
these
metallic components and the electrode at the same time. The operator should be insulated from all such bonded metallic
components.
10.9.
Earthing of the workpiece.
It is important that the workpiece is separately bonded to earth in addition to the welder/inverter return
cable. Where the workpiece is not bonded to earth for electrical safety reasons or because of its size and position, e.g. ship’s hull or
building steelwork, a connection bonding the workpiece to earth may reduce emissions in some, but not all instances. Care should be
taken to prevent the earthing of the workpiece increasing the risk of injury to others or damage to other electrical equipment.
Where necessary, the connection of the workpiece to earth should be made by a direct connection to the workpiece, but in some
countries where direct connection is not permitted, the bonding should be achieved by a suitable capacitance, selected according to
national regulations..
10.10.
Screening and shielding.
Selective screening and shielding of other cables and equipment in the surrounding area may alleviate
problems of interference. Screening of the entire welding/cutting installation may be considered for special applications.
NOTE: It is our policy to continually improve products and as such we reserve the right to alter data, specifications and component parts without prior notice.
IMPORTANT:
No liability is accepted for incorrect use of this product.
WARRANTY:
Guarantee is 12 months from purchase date, proof of which will be required for any claim.
INFORMATION:
For a copy of our latest catalogue and promotions call us on 01284 757525 and leave your full name and address, including postcode.
01284 757500
01284 703534
Sole UK Distributor, Sealey Group,
Kempson Way, Suffolk Business Park
,
Bury St. Edmunds, Suffolk,
IP32 7AR
www.sealey.co.uk
Web
Environmental Protection.
Recycle unwanted materials instead of disposing of them as waste. All tools, accessories and packaging should be sorted,
taken to a recycle centre and disposed of in a manner which is compatible with the environment.
WEEE REGULATIONS.
Dispose of this product at the end of its working life in compliance with the EU Directive on Waste
Electrical and Electronic Equipment. When the product is no longer required, it must be disposed of in an environmentally
protective way.
Original Language Version
PP40H Issue: 1 - 08/05/13
Parts support is available for this product. To obtain a parts listing and/or diagram, please log on to www.sealey.co.uk,
email [email protected] or phone 01284 757500.
© Jack Sealey Limited 2013