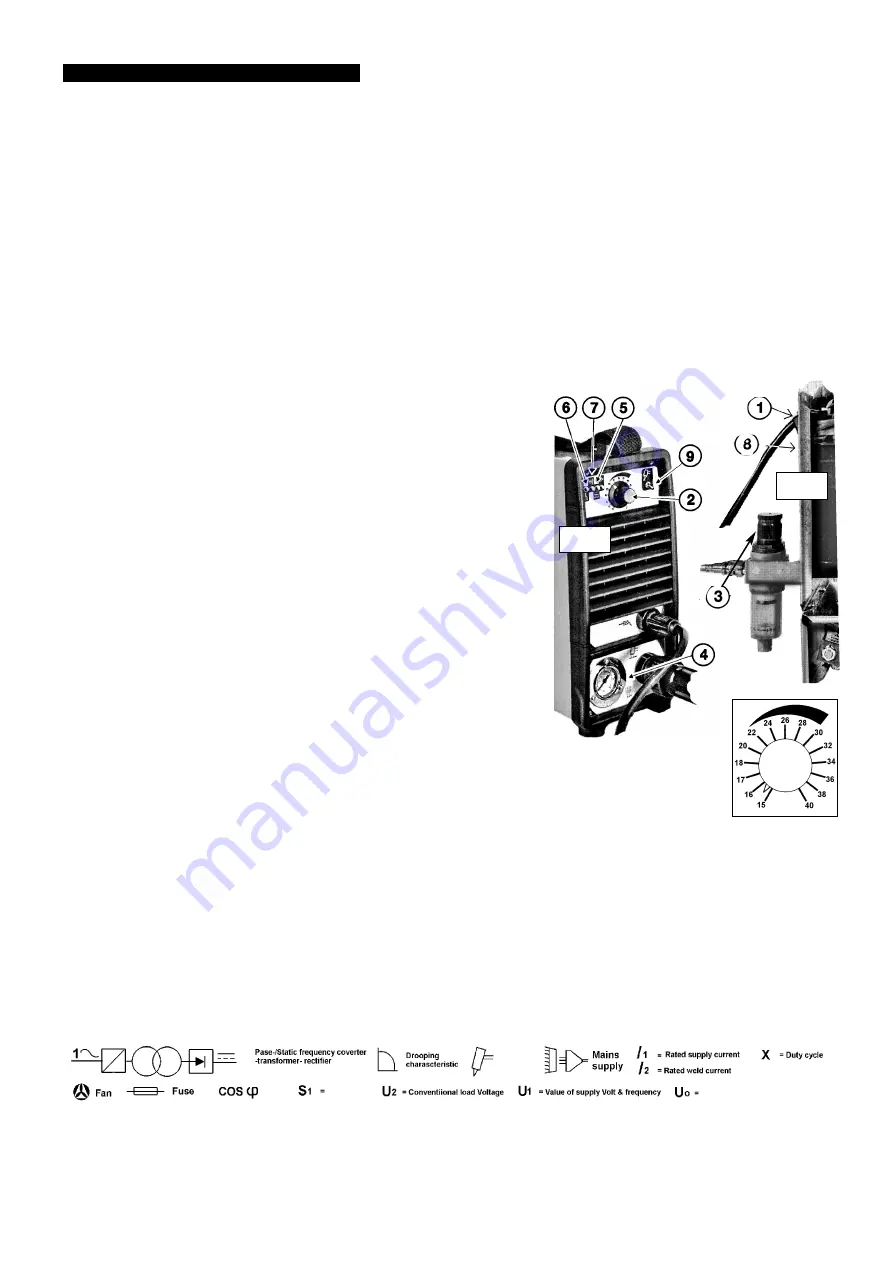
p
WARNING!
before operating the machine ensure that you have read, understand and apply chapter 2 safety instructions. Ensure the machine
is disconnected from the power supply before moving or changing accessories.
5.1.
Locating the Machine.
5.1.1. Ensure your work area has a good airflow and that there is no dust, smoke or gas present.
5.1.2. Ensure that there is a minimum clearance of 500mm around the machine, and there are no obstacles to prevent a cool air flow.
Also check to ensure the front outlet and rear inlet grills are not blocked.
5.1.3. When moving the machine disconnect the unit from the mains power supply, and gather all cables safely.
5.2.
Connecting the Earth cable.
Connect the work cable clamp to the piece to be cut or to the metallic workbench as follows:
5.2.1. Check that there is a good electrical contact. Caution: Ensure you have made good contact on oxidised or insulate coated sheets.
5.2.2. Make the Earth connection as close to the cutting area as possible.
5.2.3. DO NOT use metallic structures or objects to make contact (i.e. return cable), other than the metallic workbench which is holding
workpiece. To do so may endanger the system safety and will give a poor cut result.
DO NOT make Earth connection to the off cut, or piece that will be removed.
5.3.
Connecting the Plasma Cutter.
5.3.1. Insert the male connector of the torch into the centralised connector on the front panel of the machine. Check to ensure the polarisation
keys match.
5.3.2. Screw the ring nut tightly clockwise to ensure air flow without leaks.
5.3.3. Before cutting, check the head of the torch to ensure it is correctly assembled.
5.4.
ON / OFF Switch.
The on/off switched is located at the rear of the machine (fig 3.1). When the
switch is in the O position the machine is turned off. When switched to the I
position the machine is turned on, which will be indicated by two green lights.
One light being the ready indicator, and the other confirmation that the mains
power is on. When switched on, the machine control and duty circuits are live
but the torch will remain in a Stand-By mode until the torch button is pressed.
5.5.
The Cutting Regulator.
The cutting current is regulated by switch (fig 2.2 & fig 4). This switch regulates
the supply of current required to cut various thickness of metal at various speeds
according to the machines technical data.
5.6.
Air Pressure Gauge
5.6.1. Check torch and view technical data to determine what pressure you will require.
5.6.2. Pull and turn the pressure regulator knob ON (fig 3.3). Flick switch (fig 2.9) down
and read pressure gauge (4) to check when the required psi value is registered.
5.6.3. Push the pressure regulator knob to lock it.
5.7.
The Torch Control.
When the machine is turned on the green indicator light will show that the torch
is in a Stand-By mode.
5.7.1. Press the torch button to activate and note the pilot arc on signal is displayed by
a yellow light (fig 2.5).
5.7.2. As a safety feature, should the following situations arise the torch will automatically
de-activate.
a) During PREAIR (0.3s) and POSTAIR (>30s) phases.
b) If the pilot arc is not moved to the workpiece within 2 seconds.
c) If the cutting arc is interrupted because it is held too far from the torch-part, or the electrode is worn out,
or the torch has been forced away from the workpiece.
d) Should the alarm security switch activate (see fig 3.8).
5.11.
The Torch
Although the machine and torch may be fully powered, the torch button is the only device that will activate the cutting process.
5.11.1. To turn the cutting process on, the torch button must be fully depressed
5.11.2. Release the button and the cutting cycle will stop immediately. The cooling air (post-air) will continue to function.
NOTE:
To minimise the possibility of accidental starting, the on button must be pushed to at least 300ms before the cutting operation will start.
5.8
The Thermal Switch & Mains Voltage Fault.
If the thermal, and mains fault switch illuminates as a RED LED and an alarm sounds, this will indicate one of the following:
a) The power transformer has overheated.
b) There has been a decrease or increase in the mains voltage power supplied to the machine.
The activation of this switch is automatic and will stop the all functions.
The problem that had caused this switch to activate is self rectifying, and within a few seconds the switch will re-set and the RED LED
light will go out. The machine is now ready to use once again.
5.9
Air Pressure Fault Signal.
If YELLOW LED together with the RED LED, (fig 2. 6 & 7), and alarm activate, this will indicate that air pressure is too great or too low.
This activation will automatically stop the machine operating.
Make any necessary adjustments to the air pressure.
Once the air pressure is correct the fault signal will return to normal, the LED displays will go out, and the machine is ready to use again.
5.10.
Technical Data.
On the rear of the machine you will find technical data as follows:
5. CONTROL INSTRUCTIONS
fig 2.
fig 4.
fig 3.
MW100, MW140, MW165 - 0051 - (1) - 010399