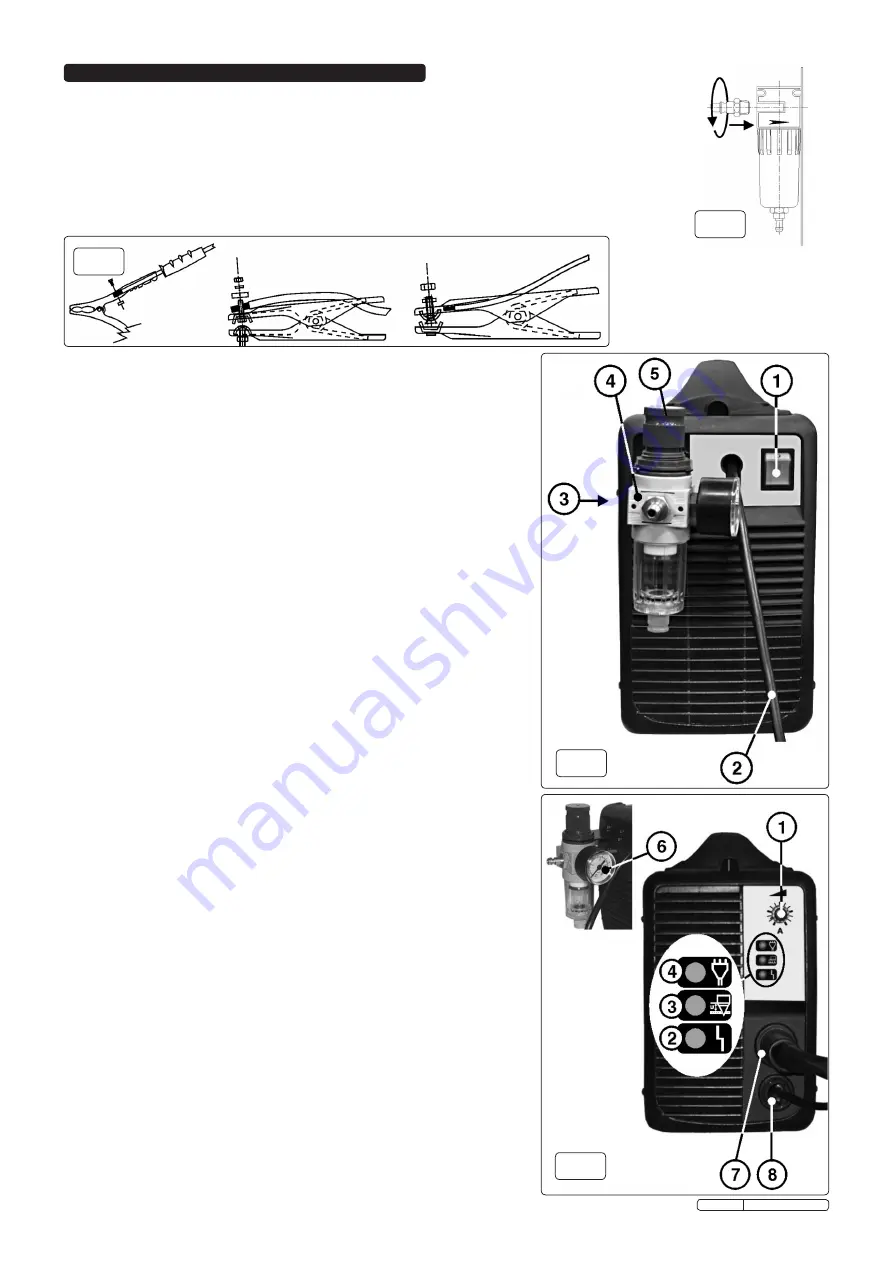
4. CONTROL INSTRUCTIONS
WARNING!
Before operating the machine ensure that you read, understand and apply Section 2 safety instructions. Ensure that
the machine is disconnected from the power supply before moving or changing accessories.
4.1.
Locating the cutter
4.1.1. Ensure that the work area has a good airflow and that there is no dust, smoke or gas present.
4.1.2. Ensure that there is a minimum clearance of 500mm around the machine and that there are no obstacles to prevent a cool airflow.
Also check to ensure that the front outlet and rear grills are not blocked.
4.1.3. When moving the machine, disconnect from the mains power supply and gather all cables safely.
4.2.
Connecting the earth cable clamp
4.2.1. Attach the earth clamp supplied to the end of the earthing cable as shown in fig.2.
4.2.2. Connect the work clamp to the workpiece or to the metal workbench as follows:
1. Check that there is a good electrical contact. Caution: Ensure that you have
made good contact on oxidised or coated sheets.
2. Make the earth connection as close to the cutting area as possible.
3. DO NOT connect to structures or objects, other than the metal workbench
which is supporting the workpiece. To do so may damage the safety system
and will give a poor cut.
4 DO NOT make the earth connection to the part of the workpiece that will be
removed.
4.3.
ON/OFF switch
The on/off switch is located at the rear of the machine (fig.4-1). When the
switch is in the “O” position the machine is turned off. When switched to
the “I” position the machine is turned on.
A green LED (fig.5-4 ) will also show on the front panel indicating that
mains power is present and the machine is in the ‘ready’ condition.
The control and duty circuits are now live but the torch will remain in
‘stand-by’ mode until the torch button is pressed.
4.4.
Cutting regulator
The cutting current is regulated by the knob/potentiometer on the
front panel (fig.5-1).
4.5.
Air pressure
4.5.1. Unlock the pressure regulator knob (fig.4-5) by pulling it upwards. Adjust
the regulator to give the required air pressure (fig.5-6). Always adjust
up
to
the required pressure.
4.5.2. Push the pressure regulator knob downwards to lock it.
4.6.
Torch control
When the machine is turned on the green indicator light (fig.5-4) will show that
the torch is in “Stand-By” mode.
4.6.1. When the torch button is pressed the machine is activated and a yellow LED
will illuminate (fig.5-3) indicating the presence of the pilot arc.
As a safety feature, should the following situations arise the torch will
automatically de-activate and the LED will go out:
a) During Post-Air (>30sec) phase.
b) If the pilot arc is not moved to the workpiece within 2 seconds.
c) If the cutting arc is interrupted because the torch is held too far from the
workpiece, or if the electrode is worn out, or if the torch has been forced
away from the workpiece.
d) If the warning LED illuminates indicating either mains voltage fluctuation
or overheating.
4.7.
Thermal or mains voltage fault
If the yellow LED (fig.5.2) on the front panel illuminates this indicates a mains
voltage or thermal problem and the machine will be automatically shut down
as a result of one of the following:
a) The power transformer has overheated.
b) There has been a decrease or increase in the mains voltage supplied
to the machine.
When the safety cut-out is activated in this way the problem is normally
self-rectifying and within a few seconds the switch will re-set and the LED
will go out. The machine is then ready for use again.
4.8. Torch
Although the machine and torch may be fully powered, the torch button is the
only way to activate the cutting process.
4.8.1. To turn the cutting process on, the torch button must be fully depressed.
4.8.2. Release the button and the cutting cycle will stop immediately. The cooling
air (post-air) will continue to flow for a further 30 seconds.
Note:
To minimise the possibility of accidental starting, the button must be pressed for
at least half a second before the cutting operation will start.
fig.4
fig.5
fig.2
fig.3
Original Language Version
PP35.V2 Issue: 3 - 15/05/12