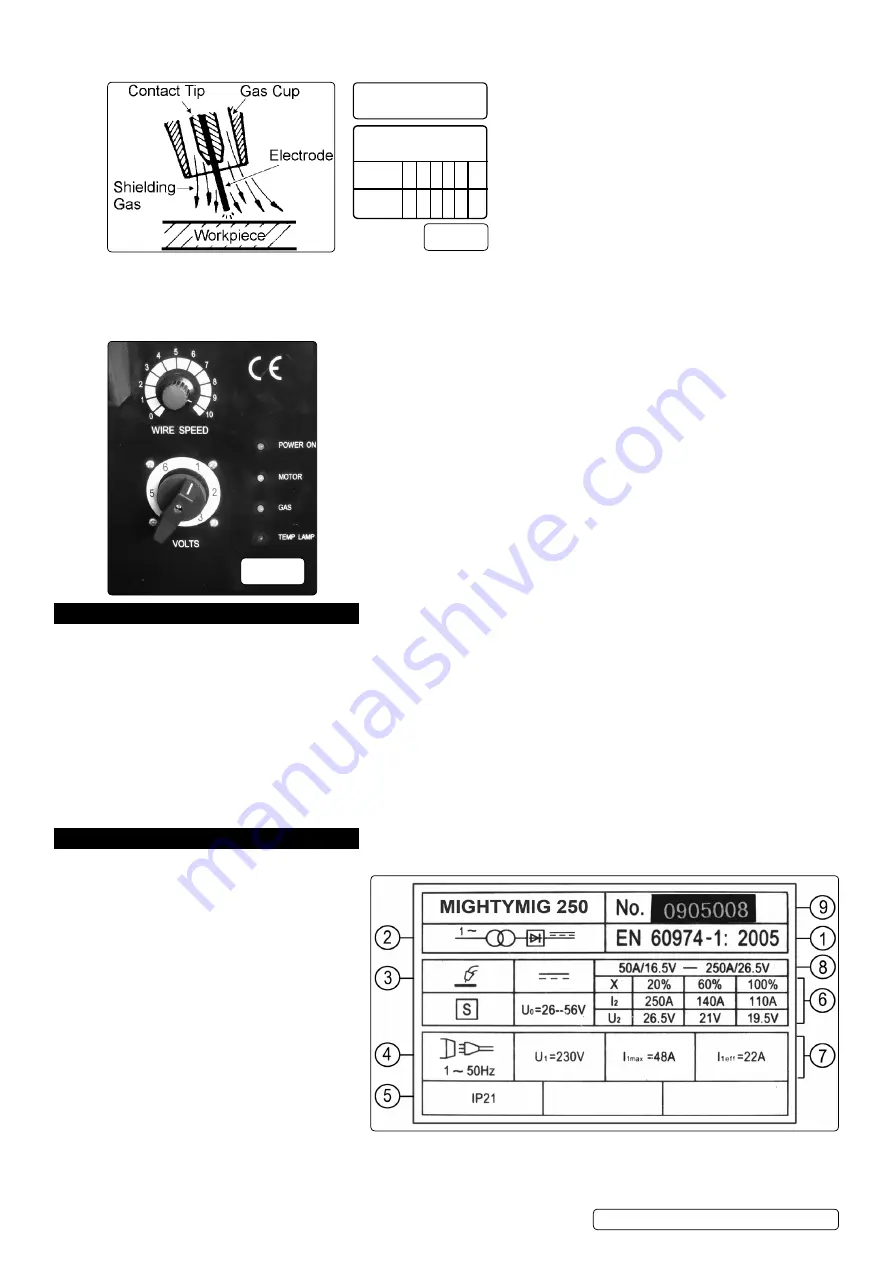
5.1.3.
setting the welder controls.
In principle, the lower the amperage required, the slower the wire speed. See setting chart for voltage and
corresponding wire speeds (see fig.14). note: these settings are only a guide and will vary according to the operator’s experience.
5.1.4.
Welding mild steel
To weld mild steel you can use Co² gas for most tasks where spatter and the high build up of weld do not pose a problem. Welding with
a long arc reduces penetration and widens the arc. This in turn results in more spatter. A long welding arc can be appropriate for welding
butt joints in thin materials. Welding with a short arc, at the same weld settings, results in greater penetration and a narrower weld and
reduces the amount of spatter. To achieve a consistent spatter free and flat weld, you must use an Argon/Co² mixture.
5.1.5.
To weld aluminium use:
Argon gas,
0.8mm Contact Tip (MIG917),
0.8mm Aluminium Wire, (MIG/2KAl08).
5.1.6.
overload Protection
. Thermostatic overload protection is provided. When an
overload occurs the TeMP lAMP on the front panel will light. See fig.15. When an
overload has occurred, leave the unit to cool. The thermostat will automatically reset
the unit when the temperature has returned within limits.
6. MainTenanCe
6.1.
Wire feed UniT
Check the wire feed unit at regular intervals. The feed roller wire guide plays an important part in obtaining consistent
results. Poor wire feed affects welding. Clean the rollers weekly, especially the feed roller groove, removing all dust deposits.
6.2.
TorCH
Protect the torch cable assembly from mechanical wear. Clean the liner from the machine forwards by using compressed air. If
the liner is clogged it must be replaced.
6.3.
CHanGinG feed roller
(See Section 4.13)
6.4.
ConTaCT TiP
The contact tip is a consumable item and must be replaced when the hole becomes enlarged or oval. The contact tip
MUST be kept free from spatter to ensure an unimpeded flow of gas. Refer to fig.10 and section 4.10 for removal and replacement.
6.5.
Gas CUP
The gas cup must also be kept clean and free from spatter. Build up of spatter inside the gas cup can cause a short circuit
at the contact tip which will result in either the fuse blowing on the printed circuit card, or expensive machine repairs. To keep the contact
tip free from spatter, we recommend the use of Sealey anti-spatter spray (MIG/722308) available from your Sealey stockist. Refer to
fig.10 and section 4.10 for removal and replacement.
6.6.
rePlaCinG THe liner
Wind the wire back on to the spool and secure it. Unscrew the torch from the machine and undo the brass
nut. The liner should now be visible. Pull it out and replace with a new one.
7. raTinGs PlaTe
on the front of the welder is the ratings plate, giving the
following data:
1 -
The standard relating to the safety and
construction of arc welding and associated
equipment.
2
-
Single phase transformer - rectifier.
3 -
Welding with a continuous flow of welding wire.
4 -
Single-phase AC supply.
5 -
Rating of internal protection provided by casing.
6 -
output
U0: Rated minimum & maximum no load
voltage.
I2, U2: Current and corresponding voltage.
X: Welding ratio based on a 10 minute cycle.
20% indicates 2 minutes welding and 8 minutes
rest, 100% indicates continuous welding.
7 -
Mains SupplyU1: Rated supply voltage and frequency. Imax: Maximum current.I1eff: Maximum effective current.
8 -
Welding current range.
9 -
Serial number. Specifically identifies each welder.
fig.14
seTTinGs sHoWn
as GUide onlY
Wire 0.8mm steel
argon / Co2 Mix
Voltage
Step:
1 2 3 4 5 6
Wire
Speed:
4 5 6 7 8 9
fig.15
MIGHTYMIG250 Issue 2 (HF) 15/05/18
Original Language Version
© Jack Sealey limited