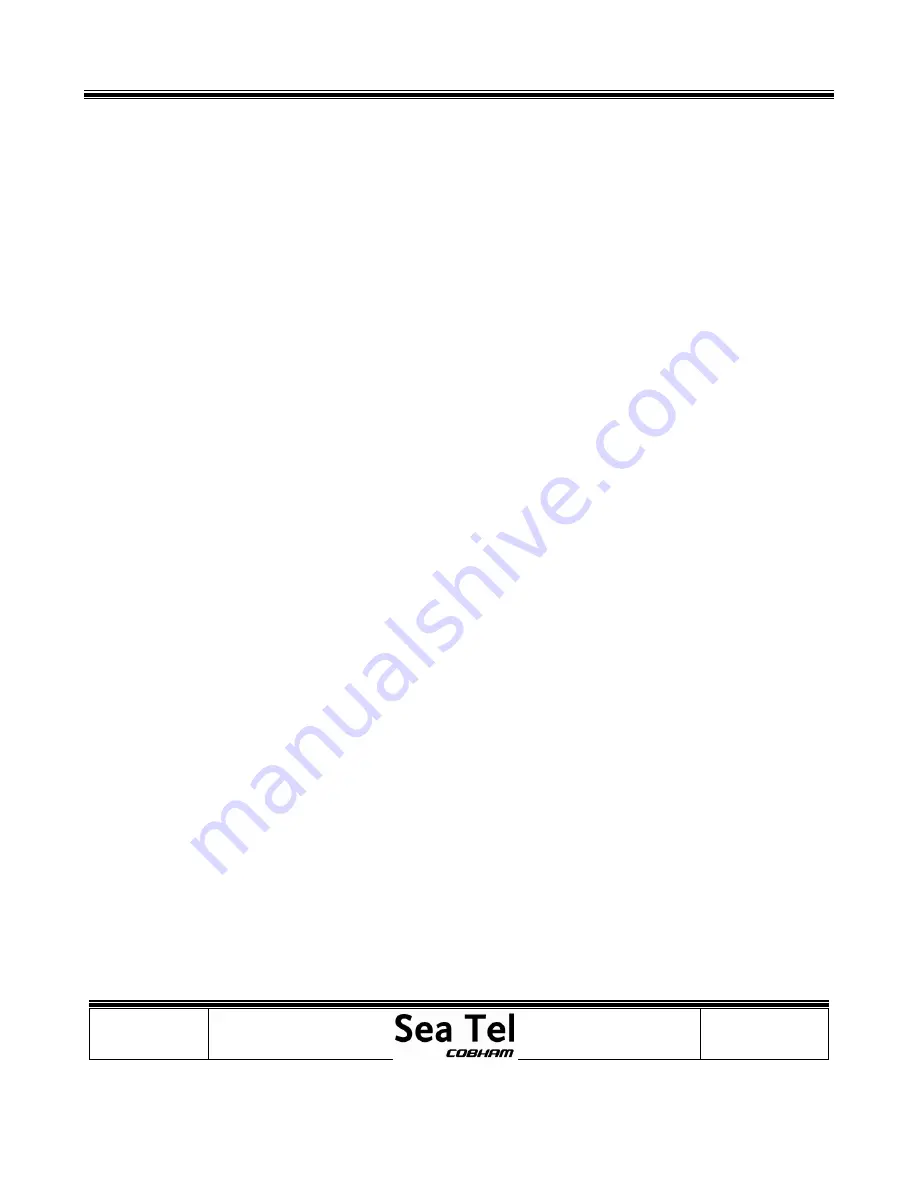
Field Service Procedure – Replacement PCU Kit, ST88, ST94 & ST144
Page
5
of
22
Document No
137738 Rev A
Copyright © Sea Tel, Inc 2012 - The information contained in this document is proprietary to Sea
Tel, Inc. This document may not be reproduced or distributed in any form without prior written
consent of Sea Tel, Inc.
8.
Test
The
Motor:
Check
continuity
between
ground
(the
motor
connector
back
shell)
and
the
3
driver
outputs
on
pins
1,
2
and
3
of
the
harness.
Now
check
continuity
between
pins
4,
5,
6,
7,
8
and
the
ground
(the
motor
connector
back
shell).
Or
this
might
be
steps
in
a
procedure
that
does
not
require
a
table.
Also
check
between
the
individual
pins
1,
2,
3
and
the
rest
of
the
pins
(i.e.
test
pin
1
to
pin
4,
5,
6,
7,
8
and
so
on,
not
between
pins
1
and
2,
1
and
3
or
2
and
3).
If
there
is
any
continuity
measured
on
the
steps
mentioned
above,
the
motor
is
defective
(which
would
be
highlighted
by
the
diagnostic
LEDs
on
the
MDE).
The
antennas
operation
should
be
verified
with
a
replacement
motor.
If
normal
operation
doesn’t
return
the
MDE/PCU
will
require
further
troubleshooting.
9.
Verify
Stabilization:
The
purpose
of
this
procedure
is
to
physically
move
the
systems
axis
under
static
conditions,
introducing
error
into
the
PCU’s
control
loop,
and
then
verify
the
system
is
able
to
return
to
its
level
position
(stabilize
itself).
These
tests
can
be
performed
by
monitoring
the
sensor
outputs
on
DacRemP
or
also
by
physically
moving
the
antenna
and
observing
how
it
responds.
1.
Turn
tracking
off
and
open
the
DISP_V
screen
of
DacRemP.
The
software
will
now
plot
the
level
position
of
the
LV
and
CL
MEM
sensors.
Observe
for
any
abnormalities.
2.
Verify
Cross
Level
response:
Standing
behind
the
system,
push
the
cross
level
beam
down
to
the
left
and
hold
it
in
position.
Verify
that
the
CL
trace
on
DacRemP
moves
down
an
equal
amount
to
the
movement
exerted
on
the
axis.
Release
the
axis
and
verify
the
DacRemP
trace
and
system
axis
both
return
back
to
their
original
positions
instantly,
without
deviating
or
taking
time
to
settle.
Now
push
the
cross
level
beam
down
to
the
right
and
hold
it
in
position.
Verify
that
the
CL
trace
on
DacRemP
moves
up
an
equal
amount
to
the
movement
exerted
on
the
axis.
Release
the
axis
and
verify
the
DacRemP
trace
and
system
axis
both
return
back
to
their
original
positions
instantly,
without
deviating
or
taking
time
to
settle.
3.
Verify
Level
(Elevation)
response:
Push
the
reflector
up
in
elevation
and
hold
it
in
position.
Verify
that
the
LV
trace
on
DacRemP
moves
down
an
equal
amount
to
the
movement
exerted
on
the
axis.
Release
the
axis
and
verify
the
DacRemP
trace
and
system
axis
both
return
back
to
their
original
positions
instantly,
without
deviating
or
taking
time
to
settle.
Push
the
reflector
down
in
elevation
and
hold
it
in
position.
Verify
that
the
LV
trace
on
DacRemP
moves
up
an
equal
amount
to
the
movement
exerted
on
the
axis.
Release
the
axis
and
verify
the
DacRemP
trace
and
system
axis
both
return
back
to
their
original
positions
instantly,
without
deviating
or
taking
time
to
settle.
4.
In
DacRemP,
the
trace
should
look
similar
to
the
below
image.
Note
how
after
each
movement
the
system
returns
to
its
level
position
efficiently
without
taking
time
to
settle.
Содержание ST144
Страница 1: ......