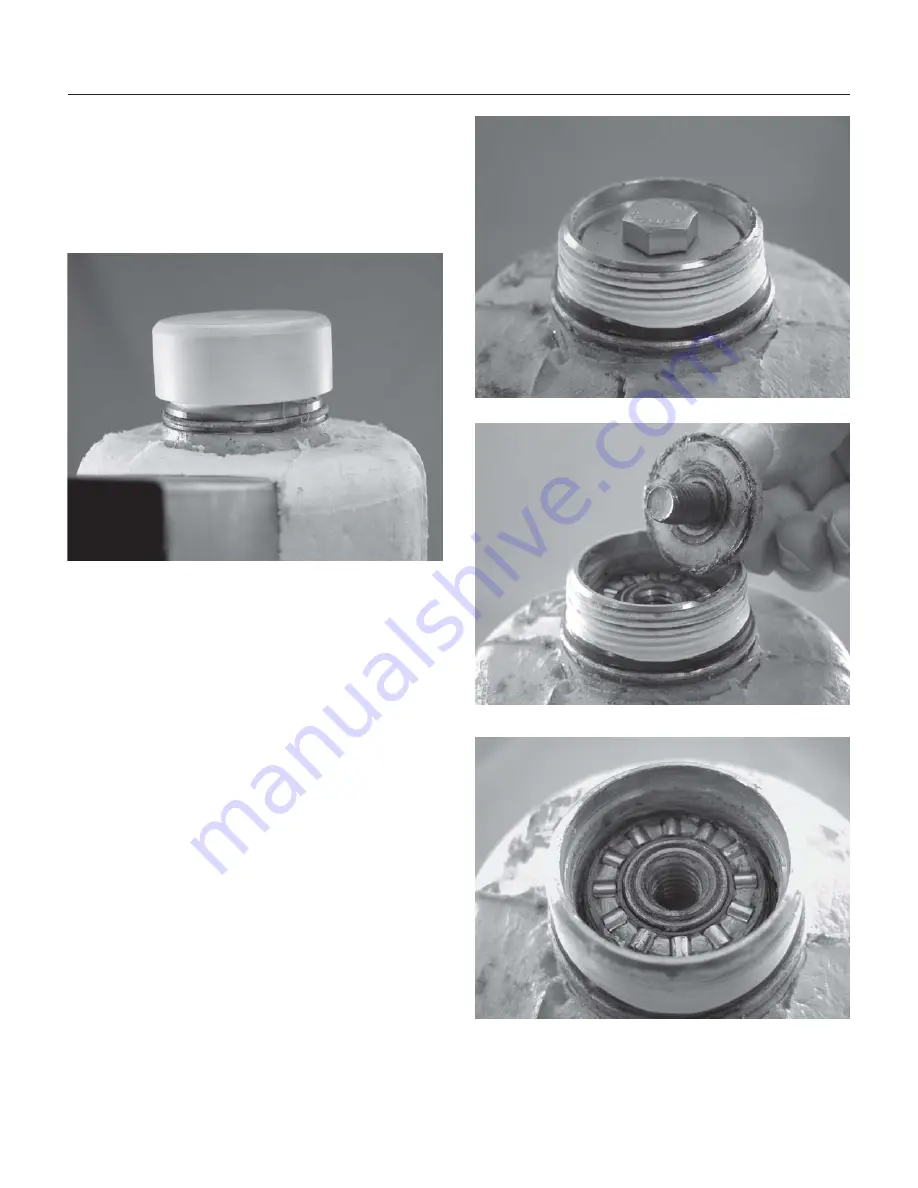
Inspection: Top Bearing
This procedure applies to machines produced after
April 2010.
1.Shut machine off by disconnecting electrical
power.
2. Remove top panel.
3. Unscrew and remove bearing sealing cap
4. Check the top bearing. The top of the thrust
washer will be visible. It should be clean, as seen
in the photo.
5. Remove the bolt and thrust washer and check
the bearing surface for adequate grease. Grease
should just cover the bearing surface. Wipe out
any contaminated grease. Add new grease,
Scotsman part number 19-0662-02. If water or rust
is present, replace the bearing.
6. Check the bottom of the evaporator for water
leaks. Some condensation is normal, however
visible water may be a sign of a water seal leak.
7. Reverse all of the above to reassemble
Note; The bottom bearing must be removed from
the evaporator when replacing the water seal. See
page 25.
MDT3F & MDT4F
April 2010
Page 17
Sealing Cap
Top of Bearing Thrust Washer
Thrust Washer and Bearing
Thrust Bearing Surface