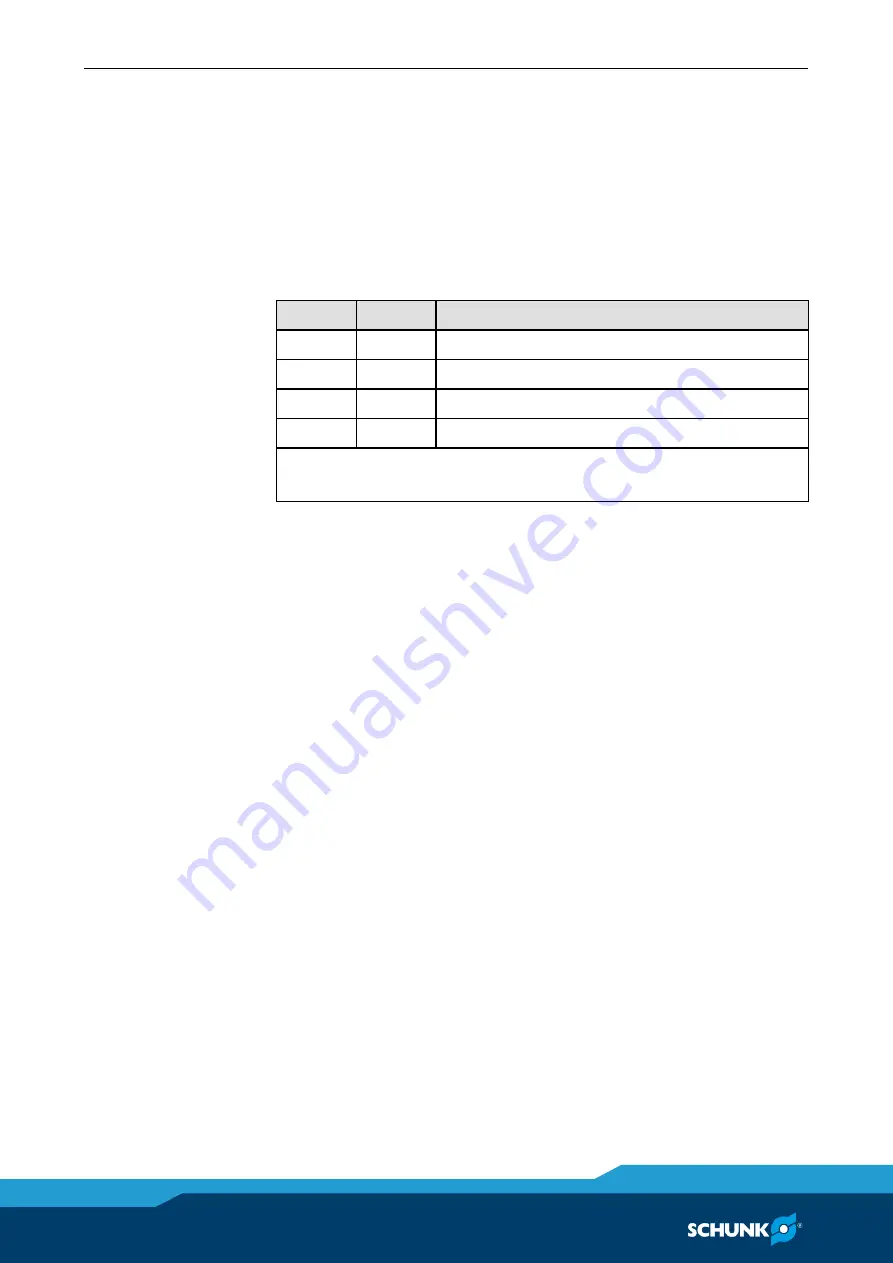
Commands
20
01.00|WSG |en
JOG+ and JOG- - Jog Mode in positive and negative direction
This command is used to move the gripper fingers manually to set
up a process.
The Jog Flags are evaluated level-sensitive and allow a constant
speed drive of the fingers using two switches on the PLC.
Interpretation of the Flags
JOG+
JOG-
Movement direction
0
0
Jog Mode is disabled*
1
0
positive with SPEED
0
1
negative with SPEED
1
1
Stop
*If the Jog flags change to both 0, the Jog mode is left and the
drive is stopped.
The force limit (current controlled only) as well as the speed can
be passed as parameters.
You may consider using a hand wheel to control them. Be aware that
high movement speed may interfere with a low force limit setting.
NOTE
In contrast to other motion-related commands, the SPEED Para-
meter can be set to 0 resulting in an internal clamping of the value
to the minimum gripper speed.
NOTE
The Jog Mode is intended only to set up a process. Do not use the
Jog Mode in normal operation of the gripper!
Command Flag Position:
Bit 6 and 7
Parameters used:
SPEED, FORCELIMIT
Status Code
The status code register is set to E_CMD_PENDING upon start of
the movement and set to the command’s result when it has fi-
nished.
4.7