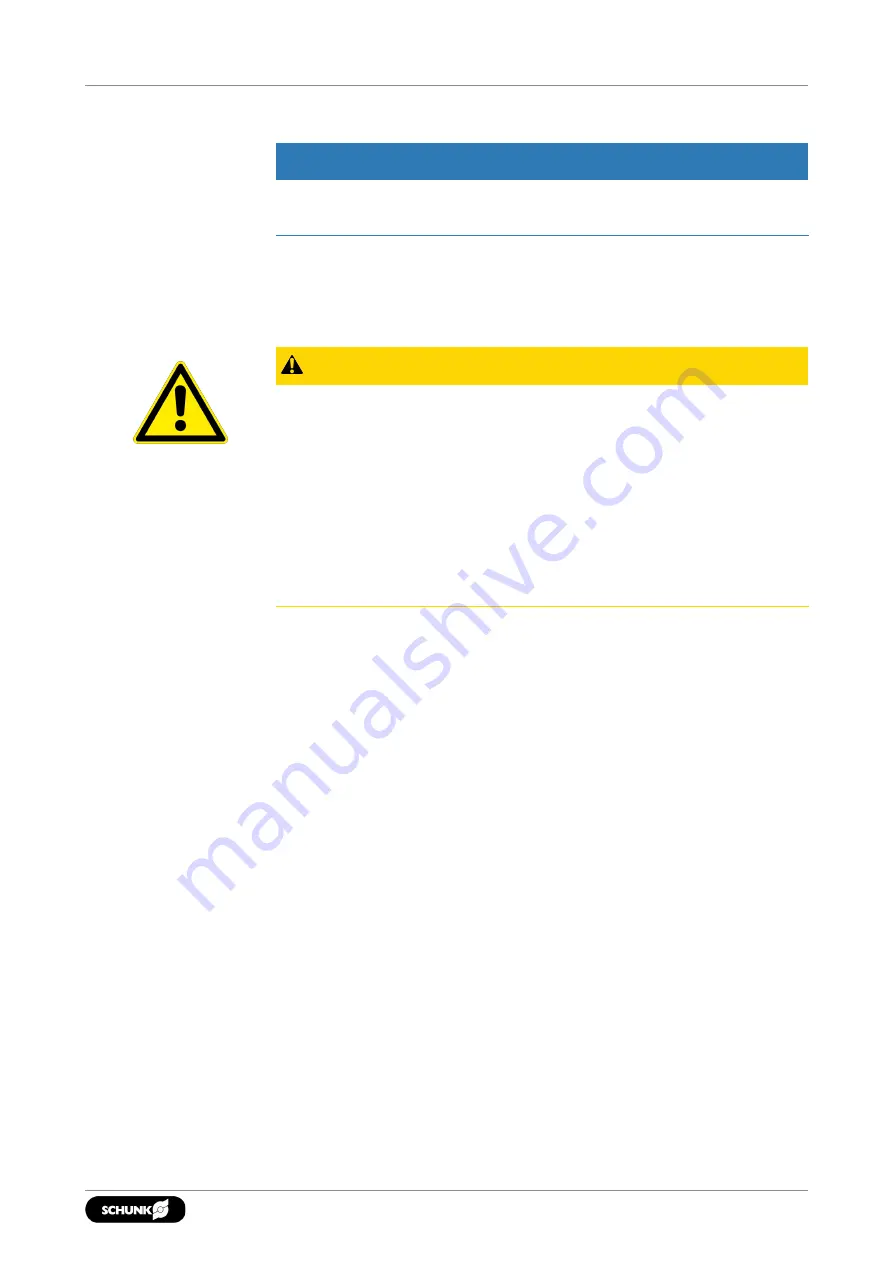
Maintenance and care
9 Maintenance and care
NOTICE
A separate maintenance unit with oiler must be used for the air
supply.
To ensure the quick-change pallet system operates perfectly, the
following instructions are to be observed:
Pressure medium: Compressed air, compressed air quality
according to ISO 8573‐1: 7:4:4
CAUTION
Risk of injury and risk of damage to the clamping module when
opening the housing cover.
If the clamping module has to be disassembled, send the
module to SCHUNK for repair.
The back cover of the clamping module is spring preloaded and
must only be removed by trained specialist personnel. The
cover can only be disassembled and assembled using a special
assembly tool and by observing the corresponding disassembly
and assembly instructions.
• Check the units at regular intervals (at least every two weeks or
after 1000 clampings).
The system is functioning correctly if the clamping slides move
smoothly at minimum system pressure (5 bar).
• Carry out regular visual/functional checks. In case of visible
damage or signs of malfunction, shut down the quick-change
pallet system immediately.
The system may only be commissioned again once the faults
have been removed. For example, by replacing the damaged
unit.
37
05.00 | NSE-A3 | VERO-S quick-change pallet system | en | 1376941
Содержание VERO-S NSE3-A3 138
Страница 44: ...Assembly Drawings 44 05 00 NSE A3 VERO S quick change pallet system en 1376941 12 2 Cone seal KVS3 138...
Страница 49: ......
Страница 50: ......
Страница 51: ......