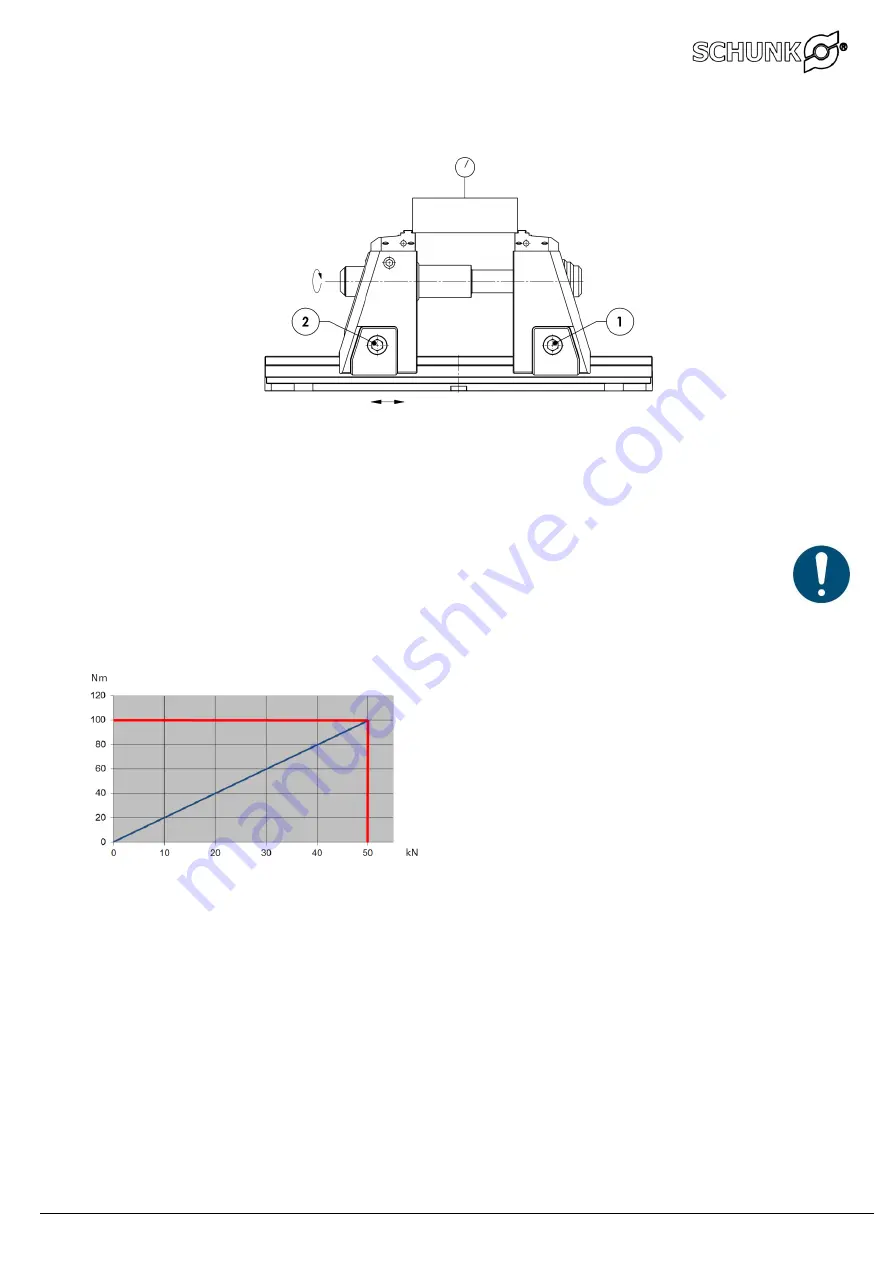
_________________________________________________________________________________________
XND.00041.002_B – 05/2022
33
Raw workpiece clamping (with lift-off)
5.2
With the raw part clamping it is possible to clamp with simpler set-up and greater clamping forces.
Position fixed support jaw and tighten the cylinder screw 1 with a torque of 140 Nm.
Cylinder screw 1 at the movable support jaw remains loose and workpiece is clamped with the
desired clamping force.
Important:
Significantly higher clamping forces are achieved with the raw workpiece clamping.
Make sure that the torque of 100 Nm is not exceeded to overload the clamping system in
the long run.
Raw part clamping KSX-C2 125 and KSX-C2 125-L