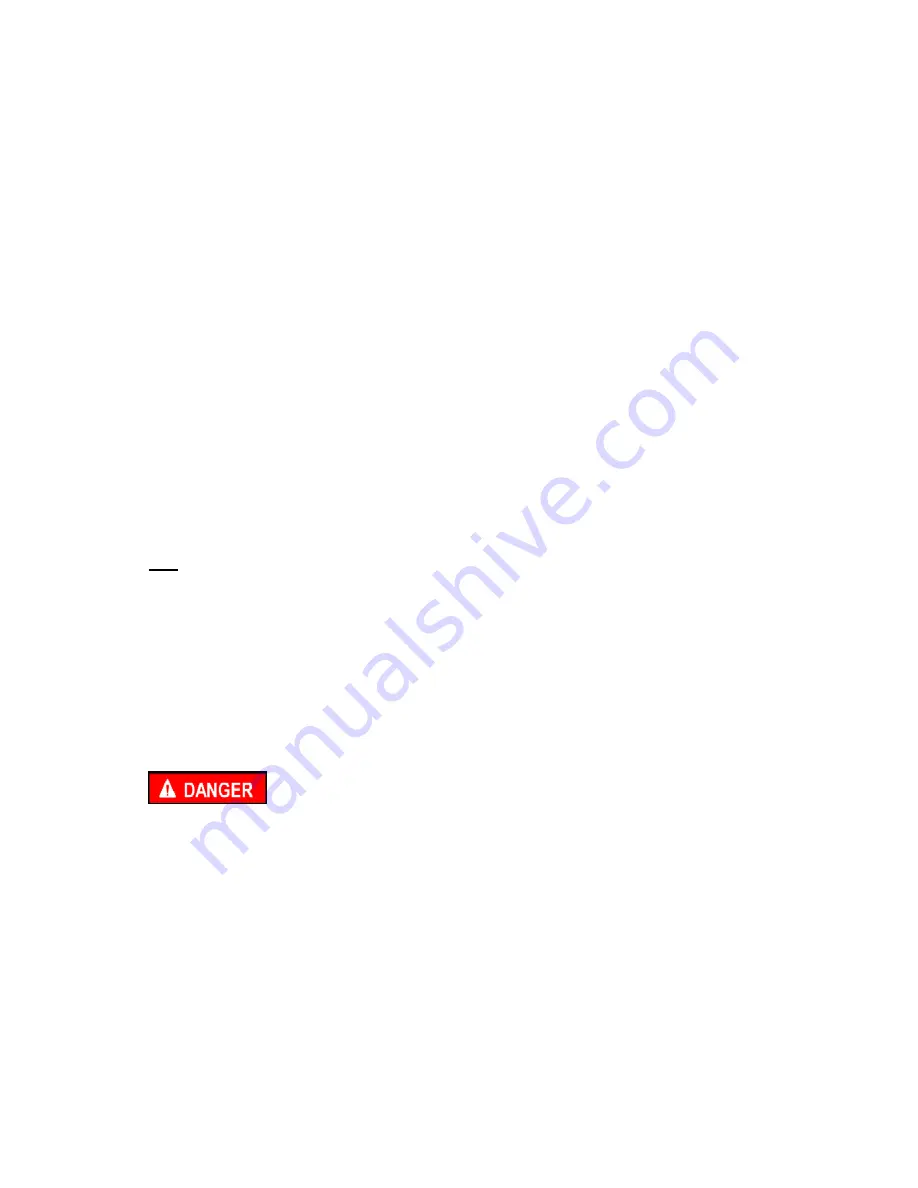
Copyright © 2021 Axxiom Manufacturing, Inc.
3
3.1
DISASSEMBLY PROCEDURE.
Refer to Figure 3.1 on the previous page.
The tools required for this procedure include: 3/32” allen wrench, 7/16” and 9/16” wrenches, #2 phillips screwdriver, and pliers.
3.1.1
Remove both the 1/4" and 1/8” hex nipple fittings (#15, #16) and 90
swivel fittings (#18, #19) from the trigger module
body (#8).
3.1.2
Remove the (3) phillips head screws (#12) to unfasten the trigger module assembly from the deadman handle (#2).
3.1.3
Remove the (2) phillips head screws (#11) to detach the right module plate (#10).
3.1.4
Remove the trigger (#1) and the attached trigger pin (#4), safety button (#6), and both springs (#7).
3.1.5
Remove the cartridge set screw (#5) from the trigger module body (#8) and pull out the cartridge assembly (#3).
3.1.6
Discard the old cartridge assembly (#3), cartridge set screw (#5), and both springs (#7).
3.2
REASSEMBLY PROCEDURE.
Refer to Figure 3.1 on the previous page
.
The tools required for this procedure include: 3/32” allen wrench, 7/16” and 9/16” wrenches, #2 phillips screwdriver, and pliers.
3.2.1
Clean the module body (#8) by removing all debris from the cartridge cavity and adjacent 1/8” and 1/4" cavities.
3.2.2
Check deadman handle (#2), trigger (#1), and cartridge cavity for cracks or defects. Replace if needed.
3.2.3
Rotate the cartridge assembly (#3) until the set screw hole is facing upwards. The set screw hole on the cartridge
assembly should align with the set screw hole on top of the module body (#8). Insert the beveled end of the cartridge
assembly first and push until it bottoms.
3.2.4
Install cartridge set screw (#5) to lock the cartridge assembly (#8) in place. Tighten firmly, but do not over tighten.
3.2.5
Place a spring (#7) over each end of the safety button shank (#6).
3.2.6
Insert one end of the safety button shank (#6) with spring (#7) into the safety button hole on the left module plate (#9).
3.2.7
Check to ensure that the trigger pin (#4) is centered with the trigger (#1) and adjust accordingly. It may be necessary to
loosen the phillips screw on the trigger to reposition the trigger pin. Retighten the phillips screw, but do not over tighten.
3.2.8
Insert the left end of the trigger pin (#4) (with attached trigger) into the trigger pin cavity on the left module plate (#9).
3.2.9
Align the holes in the right module plate (#10) with the safety button (#6), trigger pin (#4) and hex fitting cavities.
3.2.10
Press down on the right module plate (#10) to compress springs (#7) and loosely install the phillips head screws (#11).
3.2.11
Check to ensure that the trigger pin (#4) remains positioned within the trigger pin cavity on both the left and right module
plates (#9, #10) and adjust if necessary. Tighten the phillips head screws (#11), but do not over tighten.
3.2.12
Fit the trigger module assembly onto the deadman handle (#2). The (3) phillips head screws (#12) must first be inserted
through the mating holes in the left module plate (#9) before tightening. Do not overtighten as it may strip the threads
in the right module plate (#10).
3.2.13
Reinstall the 1/4" and 1/8” hex nipple fittings (#15, #16) making sure that the ball seat end is facing outward. Use thread
sealant tape on the opposite (non-ball seat) end to mitigate air leaks.
Note:
The hex nipple fittings (#15, #16) and socket plugs (#13, #14) can be installed on the opposite side for left-handed
operation.
3.2.14
Reinstall the 1/4" and 1/8” 90
swivel fittings (#18, #19). No thread sealer is required since fittings are flared.
3.2.15
Proceed to Section 3.3 for installation instructions.
3.3
INSTALLATION.
Refer to Figure 3.1 on the previous page
.
3.3.1
The
pneumatic
G2 Trigger Deadman works in junction with a twinline hose assembly. The twinline hose assembly
consists of two color coded 3/16” air lines. The air supply line is orange and the signal/vent line is black. Each hose
contains a male flared swivel fitting on one end and a female flared rigid fitting at the other. The supply (orange) line of
the twinline has 1/4” fittings, and the signal/vent (black) line has 1/8” fittings. The G2 Trigger Deadman has matching
1/8” and 1/4” male fittings (#15, #16). It is important that the hoses have the correct sized fittings to help mitigate the
deadman valve from being installed incorrectly. Connecting the air supply to the incorrect port of the G2 Trigger
Deadman will stop the signal from venting and will not allow the blast operation to stop when the deadman trigger (#1)
is released.
Incorrect connection of the twinline hose to the G2 Trigger Deadman can result in the inability to stop the blast operation
which can result in serious injury or death.
3.3.2
Disconnect the twinline hose from the blast system and remove the existing deadman from the twinline.
3.3.3
Secure the G2 Trigger Deadman to the blast nozzle holder or the blast hose using the (2) adjustable hose clamps (#17).
3.3.4
Connect the 1/4" swivel fitting of the twinline to the 1/4” 90
swivel fitting (#19) on the G2 Trigger Deadman. No thread
sealer is required since fittings are flared. The opposite end of the twinline connects to the blast system air supply.
3.3.5
Connect the 1/8” swivel fitting of the twinline to the 1/8” 90
swivel fitting (#18) on the G2 Trigger Deadman. No thread
sealer is required since fittings are flared. The opposite end of the twinline is the signal air which starts the blast.
3.3.6
Reconnect opposite ends of the twinline hose to the mating connections on the abrasive blast system.
3.3.7
To test the G2 Trigger Deadman, press in the safety button (#6) and pull the trigger (#1) to activate the deadman valve
and start the blast operation. Release the trigger to stop blasting.
3.3.8
Follow the setup and pre-operating instructions provided with the blast system, then retest the operation of the G2 Trigger
Deadman. Check for air leaks at all applicable connections and repair as required.
3.4
MAINTENANCE AND INSPECTION.
Refer to Figure 3.1 on the previous page
.
3.4.1
Dirty air supply and/or back flow situations can result in an accumulation of debris in the twinline and trigger module
body (#8) which can result in malfunctions. Periodically disassemble and clean the G2 Trigger Deadman. Refer to
Sections 3.1 and 3.2 for assembly and disassembly instructions; and Section 5.0 for troubleshooting procedures.
3.4.2
Excessive abrasive found in the trigger module body (#8) indicates problems in the blast control system. Follow the
troubleshooting procedures included in the blaster operation and maintenance manual under Section 11.0.