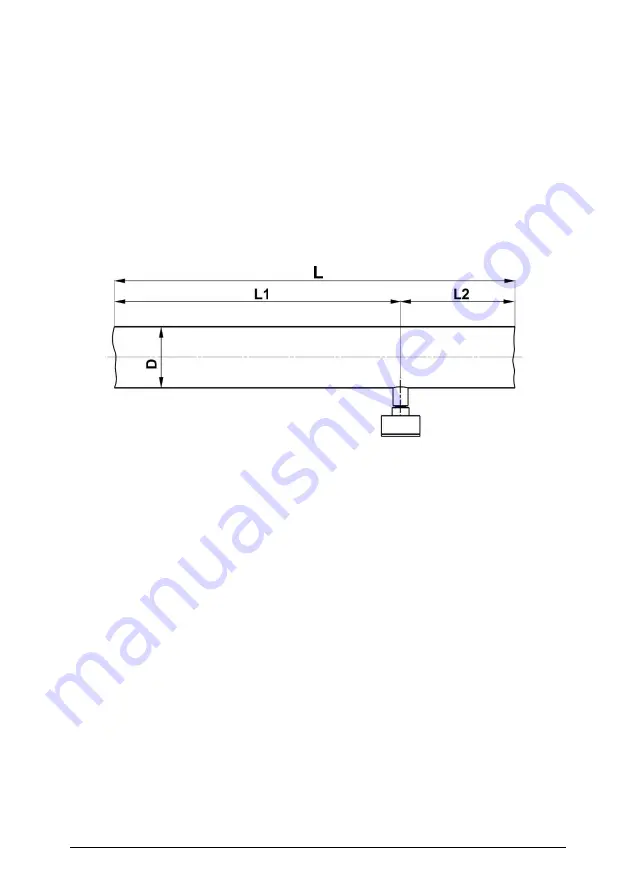
Instructions for Use
– SCHMIDT
®
Flow Sensor SS 20.500
Page 8
Mounting in pipes with circular cross-section
The mounting in a flow guiding pipe is carried out by means of a through-
bolt joint (for details refer to subchapter
"Mounting with through-bolt joint"
).
The installation of the sensor must be performed at the point with laminar
(low turbulence) flow profile to guarantee correct measurement results.
The easiest method to achieve this is to provide a sufficiently long and
straight distance without disturbances (such as edges, seams, bends etc.)
in front (inlet) and behind the sensor (outlet; see installation drawing Fig-
ure 3-3). It is also necessary to pay attention to the design of the outlet
distance because disturbances also generate turbulences against flow di-
rection.
Figure 3-3
L
Length of whole measuring distance
L1
Length of inlet distance
L2
Length of outlet distance
D
Inner diameter of measuring section
The absolute length of the corresponding distance is defined by the inner
diameter of the pipe because the flow abatement depends directly on the
aspect ratio of the measuring distance to diameter. Therefore, the required
abatement distances are specified as a multiple of the pipe diameter D.
Furthermore, the degree of turbulence generated by the respective inter-
ference object plays a major role. A slightly curved bend directs the air
with relative low disturbance level compared to a valve generating mas-
sive turbulences with its abrupt change of the flow-guiding cross-section
requiring a relatively long distance for abatement.
The required abatement distances (in relation to the pipe inner diameter
D) for different disturbances are shown in Table 1.