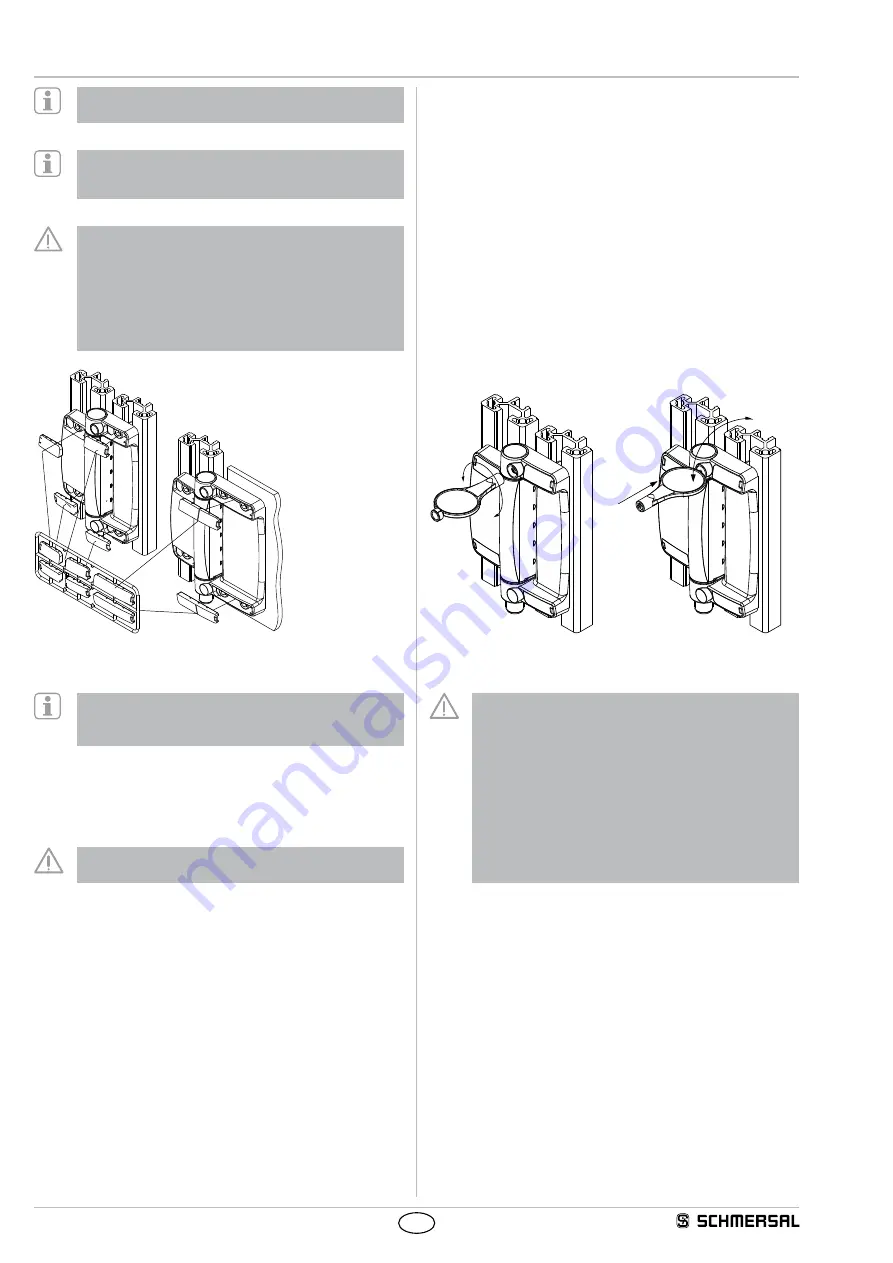
4
Operating instructions
Hinge safety switch
TESK
EN
The minimum bending radius must be observed for versions
with a cable connection!
Please note the load information "Determining the
permissible forces as a function of door size and number
of hinges" (see Section 7.3 Load details)
The hinge safety switch must not be used as an end stop.
For applications in which heavy doors are used and for use
on hoods, especially if these can close with little or no braking
effect, further measures are to be implemented to prevent the
securing bolts from working loose. A reduction in the service
life is also expected. The use of hydraulic struts on hoods
is not permitted as otherwise the hinge switch would be
damaged beyond repair.
Fig. 4
Please observe the relevant requirements of the standards
ISO 12100, ISO 14119 and ISO 14120. Also observe the
safety distances to the standards ISO 13857 and EN 349.
3.2 Adjustment and inspection of the switching angle
After the switch has been fitted, the switching function and the opening
angle of the safety guard must be checked. The switching angle of the
NC contacts set in factory is approximately 3°.
Caution: for the TESK...-U version, the following paragraph
"Special instructions for the on-site setting" must be observed!
Special instructions for the on-site setting (version TESK...-U)
We recommend a setting including the following steps:
1. Open guard system up to maximum permissible door gap
(see table chapter 7.2 Determining door gap).
2. Use the adjustment tool to set the normally-closed contacts in such
a way that they are securely opened with the maximum permissible
door gap. Turning clockwise results in a smaller switch angle while
turning anticlockwise results in a larger switch angle (fig. 6); this is
the opposite when mounted inside. To decrease the switching angle,
turn counterclockwise to increase the switching angle (Fig. 6); when
mounted inside accordingly reversed.The positive break angle is 7°
larger than the set switching angle.
3. After the switch is set, the compliance of the switch with the
safety-technical requirements of the application must be checked
(see Section 7.2 Door gap calculation).
4. After the switching angle has been set and checked, the blanking
plug for the adjustment opening located at the rear of the adjustment
tool must be inserted in the adjustment opening (1) and torn down
by making lateral movements (2) with the tool (Fig. 7).
-
+
1
2
Fig. 6
Fig. 7
After the desired switching point is set, the opening of the set-
ting option imperatively must be sealed with a blanking plug.
This measure prevents tampering at the set switching point
within the meaning of ISO 14119 paragraph 5.7 and therefore
avoids any loss of the safety function of the device.
The blanking plug is injected to the special adjustment tool
with a predetermined breaking point.
We recommend an additional painting or glueing of the
blanking plug.
Securing the setting screw by means of the blanking plug is a
mandatory instruction for the user, which must be oberved in
order to maintain the CE-Conformity of the component.