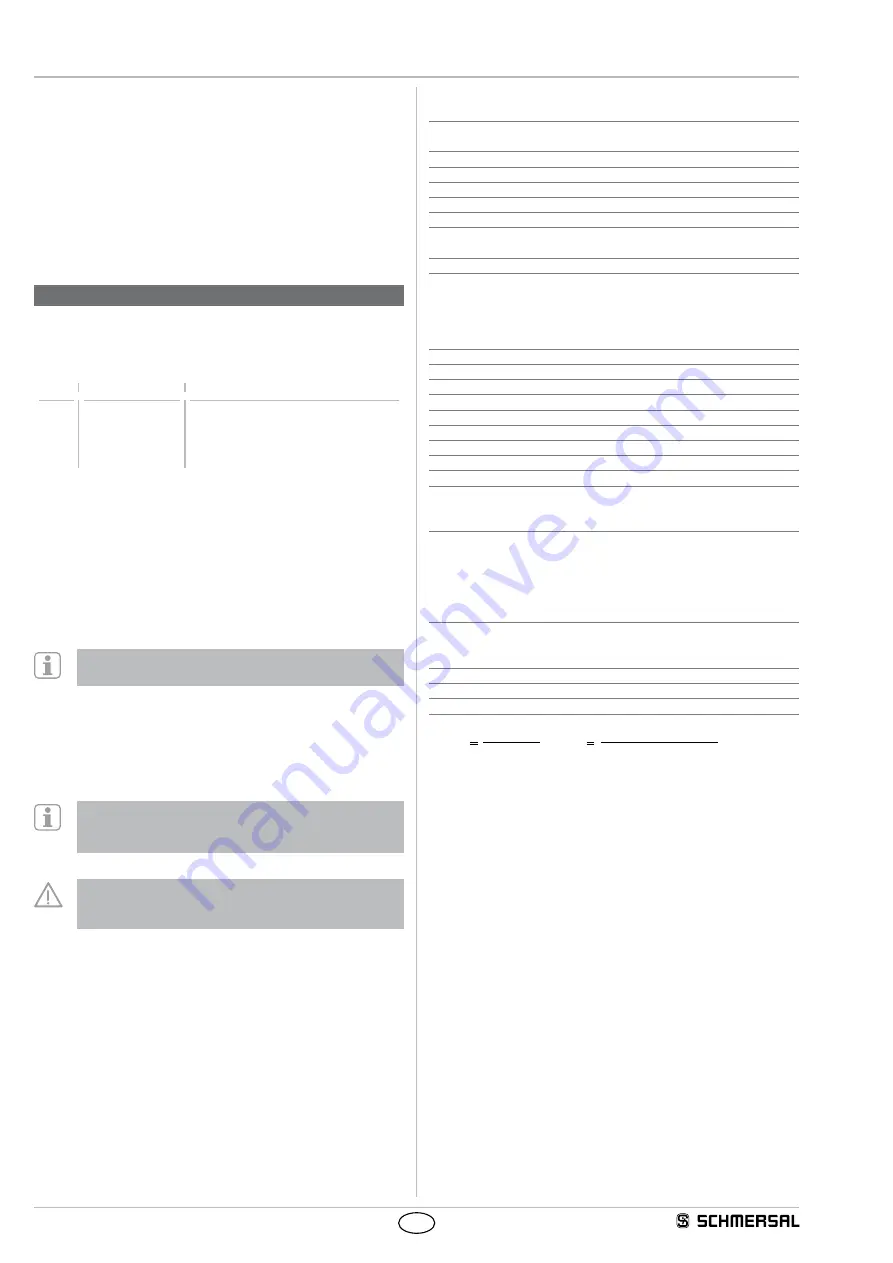
2
Operating instructions
Safety sensor
BNS 180
EN
1.7 Exclusion of liability
We shall accept no liability for damages and malfunctions resulting from
defective mounting or failure to comply with this operating instructions
manual. The manufacturer shall accept no liability for damages result-
ing from the use of unauthorised spare parts or accessories.
For safety reasons, invasive work on the device as well as arbitrary re-
pairs, conversions and modifications to the device are strictly forbidden;
the manufacturer shall accept no liability for damages resulting from
such invasive work, arbitrary repairs, conversions and/or modifications
to the device.
2. Product description
2.1 Ordering code
This operating instructions manual applies to the following types:
BNS 180-
➀
Z-
➁
No.
Option
Description
➀
11
1 NO / 1 NC
12
1 NO / 2 NC
02
2 NC
➁
2187-2
individual contact outlet
2.2 Special versions
For special versions, which are not listed in the order code below 2.1,
these specifications apply accordingly, provided that they correspond to
the standard version.
2.3 Destination and use
The safety sensor is designed for application in safety circuits and is
used for monitoring the position of movable safety guards to ISO 14119
and IEC 60947-5-3. To actuate the safety sensors, only the BP 6, BP 8,
BP 10 or BP 15 SS actuators can be used.
The safety switchgears are classified according to
ISO 14119 as type 3 switching devices.
The safety switches are used for applications, in which the hazardous
situation is terminated without delay when the safety guard is opened.
Only the entire system consisting of the safety sensor (BNS), the actu-
ator (BP) and the safety-monitoring module (AES/SRB/AZR) meets the
requirements of the standard IEC 60947-5-3.
The user must evaluate and design the safety chain in
accordance with the relevant standards and the required
safety level.
The entire concept of the control system, in which the safety
component is integrated, must be validated to the relevant
standards.
2.4 Technical data
Standards:
IEC 60947-5-3; BG-GS-ET-14
Enclosure:
glass-fibre reinforced thermoplastic
tightening torque A/F 24 max. 500 Ncm
Protection class:
IP67 to IEC 60529
Connection:
Boflex cable
Connecting cable:
4 x 0.25 mm²
Ordering suffix -2187-2:
6 x 0.25 mm²
Operating principle:
magnetic
Actuator:
BP 6; BP 8; BP 10;
BP 15 SS; not coded
Coding level according to ISO 14119:
none
Switching distances:
- Assured switching distance s
ao
:
10 mm (BP 6, BP 8);
20 mm (BP 10, BP 15 SS)
- Assured switch-off distance s
ar
:
22 mm (BP 6, BP 8);
32 mm (BP 10, BP 15 SS)
Switching voltage:
max. 100 VAC/DC
Switching current:
max. 250mA
Switching capacity (UL):
max. 3 W
Required short-circuit current:
100 A
Ambient temperature:
−25 °C ... +70 °C
Storage and transport temperature:
−25 °C ... +70 °C
Max. switching frequency:
5 Hz
Resistance to shock:
30 g / 11 ms
Resistance to vibration:
10 ... 55 Hz, amplitude 1 mm
2.5 Safety classification
Standards:
ISO 13849-1
Safety contacts:
- NC / NC combination:
21-22 and 11-12 or
21-22 and 31-32 or
C-22 and C-32
- NC / NO combination:
21-22 and 13-14 or
C-22 and C-14
Intended structure:
- 2-channel usage:
usable to cat. 4 / PL e
with suitable logic unit
B
10d
NC contacts at 20 % contact load:
25.000.000
B
10d
NO contacts at 20 % contact load:
25.000.000
Service life:
20 years
MTTF
B
d x
x
h
s/h
3600
d
10d
op
op
op
n
0,1 x n
op
t
cycle
(Determined values can vary depending on the application-specific
parameters h
op
, d
op
and t
cycle
as well as the load.)
If multiple safety components are wired in series, the Performance
Level to ISO 13849-1 will be reduced due to the restricted error
detection under certain circumstances.