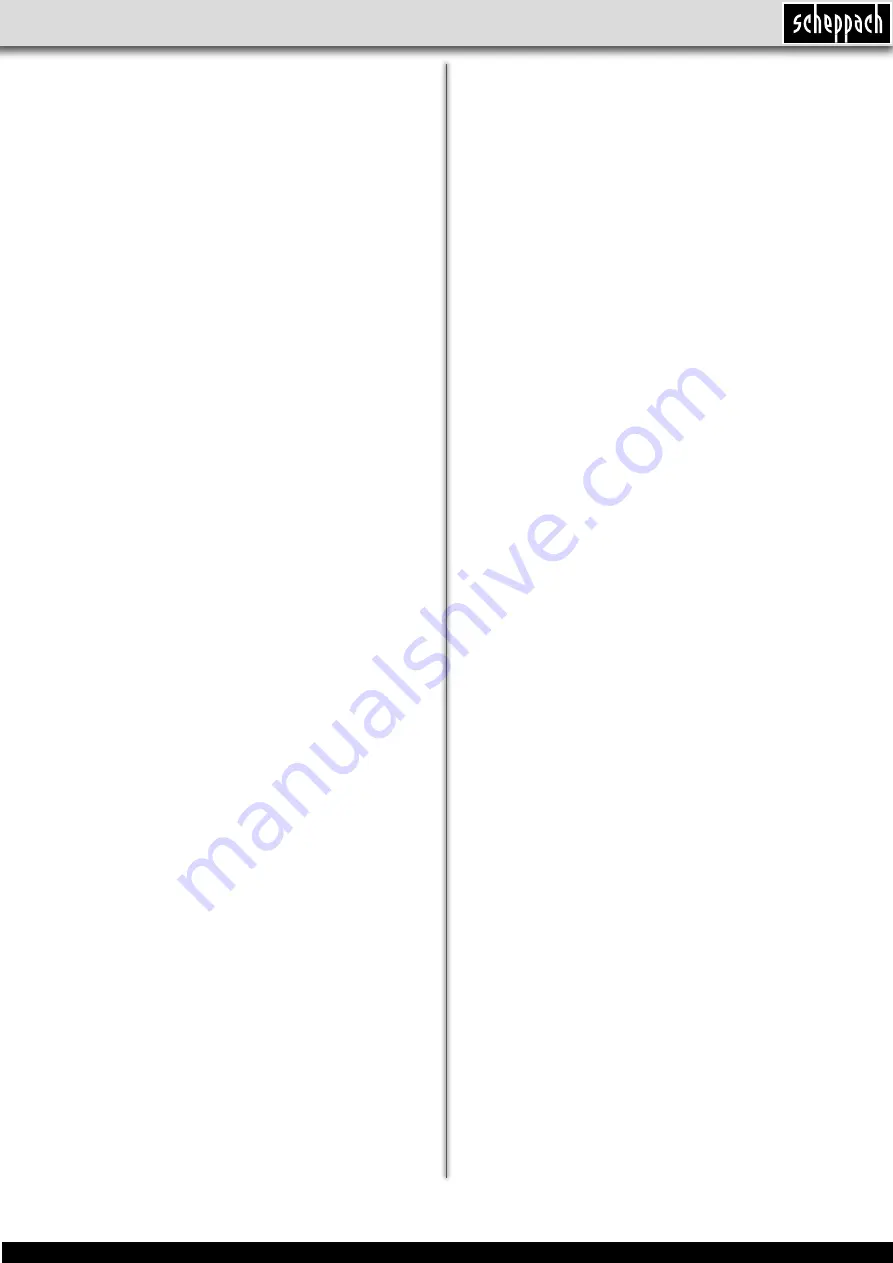
www.scheppach.com
+(49)-08223-4002-99
+(49)-08223-4002-58
21 І 80
www.scheppach.com
+(49)-08223-4002-99
+(49)-08223-4002-58
•
Ensure that the machine can run without interrup
-
tion (i.e. remove workpieces, drill bits, etc.).
Use the speed control lever (6) to infi nitely adjust the
speed. The set speed is shown on the digital display (8)
in revolutions per minute.
Important!
Never let the pillar drill run when the V-belt
cover is open. Always pull power plug before opening
the cover. Never touch the V-belt when it is rotating.
Drill depth stop (Fig. 16)
The drilling spindle has a swivelling scale ring (26) for
setting the drill depth. Only adjust the setting when the
equipment is at a standstill.
• Press the drilling spindle downwards until the tip of
the drill bit touches the workpiece.
•
Slacken the clamping screw (25) and turn the scale
ring (26) forwards until it stops.
•
Turn the scale ring (26) back to the desired drill depth,
then lock this setting into place using the clamping
screw (25).
Important!
When setting the drill depth of a cylindrical
hole you must add the length of the drill tip.
Setting the angle of the drill table (Fig. 1/17)
•
Slacken the carriage bolt (27) under the drill table (4).
•
Set the drill table (4) to the desired angle..
•
Tighten down the carriage bolt (27) in order to lock the
drill table (4) into this position.
Setting the height of the drill table (Fig. 18/19)
•
Slacken the tightening screw (3).
• Set the drill table to the desired position with the help
of the hand crank (17).
•
Screw the tightening screw (3) back down again.
Drill table and roll base (Fig. 20)
•
Slacken the clamping screw (3) to turn the drill table
(4).
•
Slacken the thumb screws (21) to extend the roll base
(13).
Clamping the workpiece
As a general rule, use a machine vice or another suita-
ble clamping device to secure a workpiece in position.
Never hold the workpiece in place with your hand! When
drilling, the workpiece should be able to travel on the
drill table (4) for selfcentering purposes. Ensure that
the workpiece cannot rotate. This is best achieved by
placing the workpiece /machine vice on a sturdy block.
Caution!
Sheet metal parts must be clamped in to
prevent them from being torn up. Properly set the height
and angle of the drill table for each workpiece. There
must be enough distance between the upper edge of the
workpiece and the tip of the drill bit.
Using the laser (Fig. 21)
To switch on:
Move the ON/OFF switch (28) to the
“I” position to switch on the laser. Two laser lines are
projected on the workpiece and intersect at the center of
the drill tip contact point.
To switch off
: Move the ON/OFF switch (28) to the “0”
position.
Working light operation (Fig. 21/22)
Note:
Always ensure good lighting at the work station
Switching on:
Move the on/off switch (29) into the “I”
position to switch the working light (30) on.
Switching off:
Move the on/off switch (29) into the “0”
position.
degreased using an environmentally friendly solvent.
This ensures optimal transmission of power.
Installing the machine
Before you use the drill for the first time it must be
mounted in a stationary position on a firm surface. Use
both mounting holes in the base plate to do this. Ensure
that the machine is freely accessible for operation,
adjustment and maintenance.
Important:
The fixing screws may only be tightened to a
point where they do not distort or deform the base plate.
Excessive tension can lead to fracture.
Prior to starting
Ensure that the voltage of the mains supply complies
with the specifications on the rating plate. Connect the
machine only to a socket with the properly installed
earthing contact. The table drill is equipped with a no-
volt trip that is designed to protect the operator from an
undesired restart following a drop in voltage. Should this
occur, the machine must be manually restarted.
Using the saw
General (Fig.14)
To switch on the machine, push in the green On button
“I” (23); the machine starts up. To switch off , press the
red Off button “O” (24); the device shuts down.
Ensure that you do not overload the device.
If the sound of the motor drops in pitch during operation,
it is being overloaded.
Do not overload the device to the point where the motor
comes to a standstill. Always stand in front of the machi
-
ne during operation.
Inserting the tool (Fig. 1)
Make sure that the power plug is removed from the
socket-outlet before changing tools. Only cylindrical
tools with the stipulated maximum shaft diameter may
be clamped in the scroll chuck (12). Only use a tool that
is sharp and free of defects. Do not use tools whose
shaft is damaged or which are deformed or flawed in
any other way. Use only accessories and attachments
that are specified in the operating instructions or have
been approved by the manufacturer. If the pillar drill
should become jammed, switch off the machine and
return the drill to its starting position.
Handling the keyless chuck
Your pillar drill is equipped with a keyless chuck. This
enables tools to be changed without the need for an
additional chuck key. To do so, insert the tool in the
quick-change drill chuck and tighten by hand.
Using tools with tapered shanks (Fig. 15)
The pillar drill comes with a spindle taper. To use tools
with tapered shanks (MK2), proceed as follows:
• Move the drill chuck to the lower position.
•
Eject the tapered shank using the supplied drill drift
(b), taking care as you do so to ensure that the tool
does not land on the floor.
• Insert the new tool with tapered shank in the spindle
taper with a jolt and then check that the tool is correct
-
ly seated.
Setting the speed (Fig. 1)
The operating speed of the machine is infi nitely adjusta
-
ble.
Important!
•
Speed adjustments are allowed only when the
motor is running.
•
Slowly and steadily move the speed control lever
(6) while the machine is in idle mode.