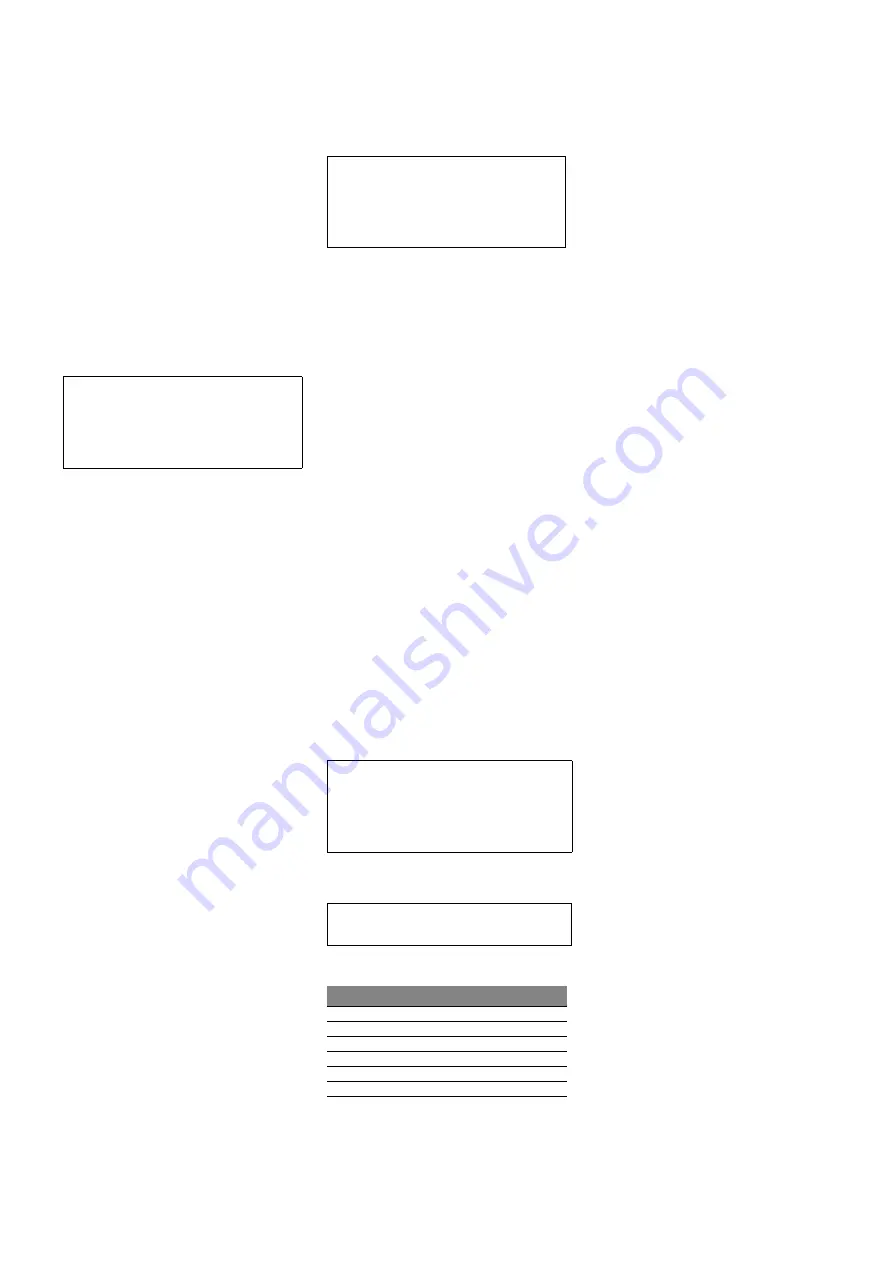
5
causes, if the limits are exceeded. Refer to
ISO 14694.
For variable speed fans the maximum
vibration level is likely to be exceeded at
certain speeds. Continuous operation at
these speeds must be avoided. A curve
showing vibration levels at different
speeds is part of the fan documentation
for variable speed fans and should be
reviewed by the user.
Notice:
The vibration levels depend on
the installation and should be
measured after completing the
installation.
6.4 Fan casing
The fan casing requires no maintenance
other than ordinary cleaning.
If the casing is painted, the surface
should be checked regularly and
repaired where necessary.
6.5 Rotor
The rotor is manufactured with the
blades mounted to the pitch
corresponding to the desired operating
point based on pressure, airflow and fan
speed. To ensure vibration free operation
the rotor has been carefully balanced.
Vibrations occurring during operation
may be due to accumulation of dust and
dirt on the hub and blades. These
disappear after cleaning. If vibrations
persist, expert assistance should be
called for immediately. Continued
vibrations shorten the life of the motor
bearings.
6.6 Motor
Refer to the motor manual for service
information such as the number of
running hours before inspection and
replacement of bearings.
It is recommended to check the motor
bearings after 20,000 running hours and
replace them when signs of wear and
tear begin to show. Subsequently, the
bearings must be checked after every
10,000 running hours.
6.7 Dismounting of motor
Refer to figure 8 in the following.
Dismounting motor
1 Dismount any ducts on the inlet and
outlet sides.
2 Remove the screws (pos. 1) holding
the hub cap and remove the cap (pos.
2) itself.
3 Remove the rotor centre screw (pos. 3)
and the centre disc (pos. 4).
4 Dismount the rotor by means of a
puller fastened in the threaded holes
of the hub boss (pos. 5).
5 Depending on the length of the
installed motor cable; draw the cable
free of the fan casing in order to
handle the motor.
6 Support the motor. See table 3 for
max. motor weights.
7 Detach the motor from the motor shell
by removing the nuts and bolts (pos.
7a and 7b).
Notice:
Nuts holding motors
mounted in rear motor
shells are accessed through
the front motor shells.
8 Remove the motor (pos. 8).
6.8 Mounting of motor
Refer to figure 8 in the following.
Mounting motor
1 Mount the motor (pos. 8) and make
sure the motor shaft is concentrically
placed in the fan casing.
2 Insert and tighten the nuts and bolts
(pos. 7a and 7b). See table 7. “Motor
and flange bolt tightening torques”.
Notice:
Nuts holding motors
mounted in rear motor
shells are accessed through
the front motor shells.
3 Mount the rotor (pos. 6) on the motor
shaft by means of a tool fastened in
the threaded hole of the motor shaft.
The rotor hub must rest against the
motor shaft collar. Check that the
rotor can rotate freely, i.e. that the
blade clearance is the same
throughout the circumference of the
casing. Adjust the motor position if
necessary.
4 Use a feeler gauge to check that the
clearance between the rotor blade tips
and fan casing is the same throughout
the circumference and meets the
following requirements.
• Minimum 2 mm
• 10% of the motor shaft diameter
• Maximum 13 mm
Refer to the motor manufacturer’s
documentation for the shaft diameter.
5 Adjust the motor position with
reference to step 4.
6 Mount the centre disc (pos. 4) and the
rotor centre screw (pos. 3).
7 Mount the hub cap (pos. 2) and mount
the screws (pos. 1).
8 Connect the motor cable in the
terminal box and connect the ducts.
To start the fan follow the procedure
described in section “5. Start of
operation”.
6.9 Troubleshooting
In case of breakdowns, the following
checklists should be completed, before
calling for service.
Lacking performance
• Damper closed
• Ducts clogged
• Supply fan, if any, stopped
• Motor defective
• Motor disconnected
• Wrong direction of rotor rotation
Important:
Constant vibration
monitoring is mandatory
for ATEX category 2D
fans, i.e. fans operating in
zone 21.
Important:
Switch off the power and
disconnect the motor
cable in the terminal box,
before beginning work
on the rotor and motor.
Important:
When working with the
fan, avoid exposing parts
to shocks. Motor bearings
and other fan components
are vulnerable parts.
Important:
Replace lock washers and
nuts during fan assembly.
Size
Torque [Nm]
M6
12
M8
30
M10
60
M12
100
M16
230
M20
470
Table 7.
Motor and flange bolt tighten-
ing torques