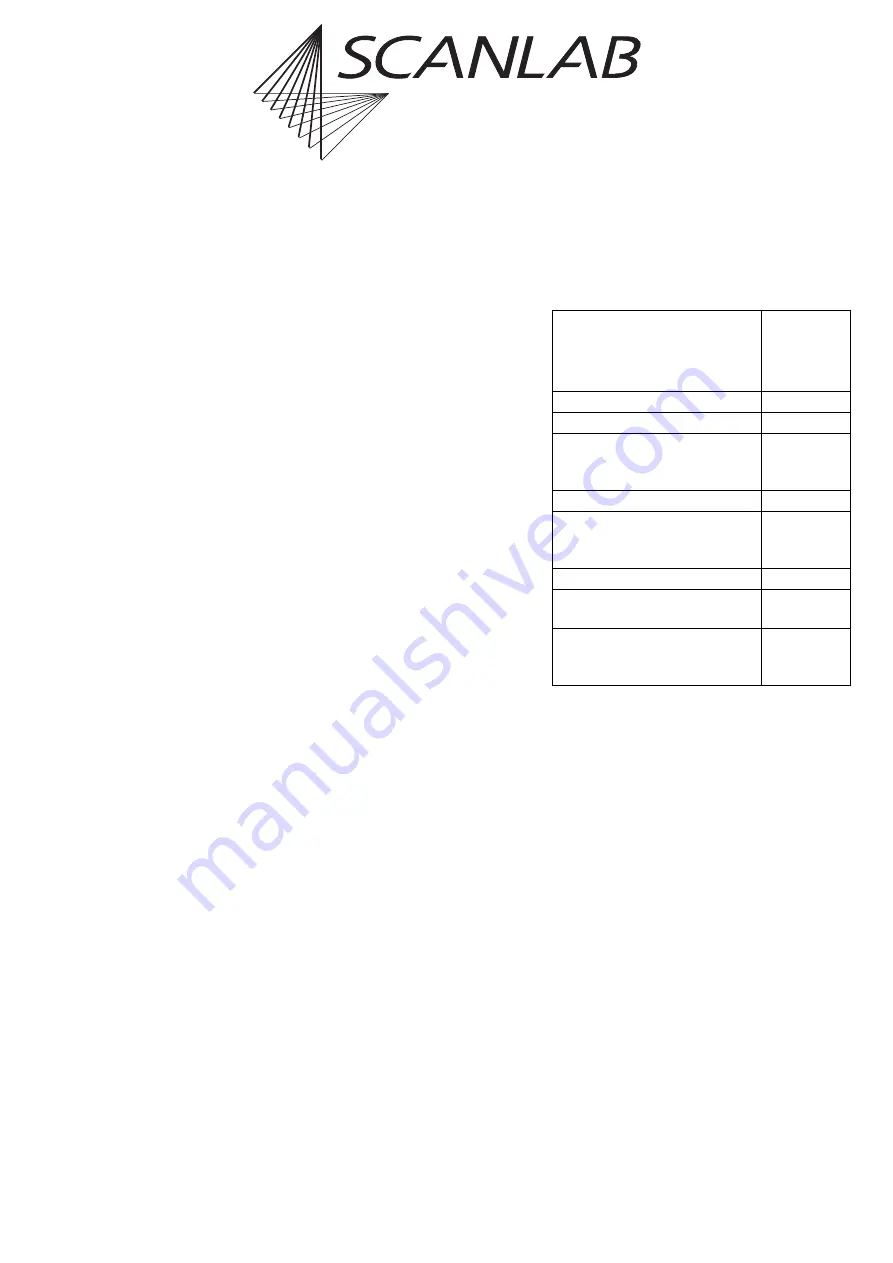
RTC
®
5 PC Interface Board
Rev. 1.9 e
8 Advanced Functions for Scan Head and Laser Control
154
innovators for industry
8.1.3 Position Monitoring
For some applications, it’s important to monitor scan
system positioning even when processing, and, if
necessary, with documentability.
For this purpose, the actual positions of the scan axes
(hence the galvanometer scanners and/or the scan
system’s Z axis) must be selected to be returned from
the scan system via the command
. The returned actual position
values can be queried via
or recorded via
/
(1)
.
If returned actual positions of the scan axes need to
be compared with cartesian coordinate values (X, Y,
Z) (which are the call parameters for RTC
®
5
commands), then it must be additionally taken into
account that these coordinate values generally –
depending on the selected settings – undergo various
corrections and transformations (e.g. an image field
correction, a coordinate transformation and/or a
Processing-on-the-fly correction) before they are
outputted as control values to the scan system (also
see
). To facilitate such comparability of the
scan system’s returned actual position values with
original cartesian coordinate values (X, Y, Z), the
RTC
®
5 command set provides commands for
backward transformation of position values.
For runtime reasons, the backward transformation
needs to subsequently be performed by the PC rather
than on the RTC
®
5 board itself. For this, all correction
and transformation settings currently assigned to the
scan system can be transferred from the RTC
®
5 board
to the PC via the
command.
Afterwards, an individual XY value pair or an indi-
vidual Z value can be backward transformed via
(also see
), you can backward transform an
entire series of XY value pairs or Z values previously
recorded via
.
Notes
• Wobbel transformations, Processing-on-the-fly
corrections and eventual clipping during forward
transformation can never be backward trans-
formed (see following table).
Likewise, backward transformation isn’t possible
if a noninvertable transformation matrix was
defined during forward transformation (note:
clipping to ±50 for each individual matrix coeffi-
cient while taking into account a factor defined
via
). The noninvertability
will already be reported by the
command.
If forward transformation included a clipping to
the edges of the positionable image field or to the
edges of the maximum possible range of control
values, then backward transformation will
(ideally) calculate the cartesian coordinates of
these edge values instead of the original values.
, four freely specifiable signals can
be queried simultaneously (example: galva-
nometer 2’s actual position via StatusAX, galva-
nometer 1’s actual position via StatusAY, the
actual Z-axis position via StatusBX, plus an
additional desired signal such as LaserOn). In
contrast, the
command (without the
‘s’ in the command name) isn’t useful for
(1) However, transfer times to/from the scan head will cause the
most recently returned actual position to lag the most recently
outputted control signal by a few clock cycles.
Forward
transformation
Backward
trans-
formation
possible
Wobbel motion
no
Processing-on-the-fly correction
no
Coordinate transformations
(total matrix and offset) to the X
and Y coordinates
yes
Offset to the Z coordinate
yes
Clipping to the edge of the
positionable (20-bit real)
image field range
no
Image field correction
yes
Gain and offset correction of
automatic self-calibration
yes
Clipping to the edge of the
maximum possible range of
control values.
no