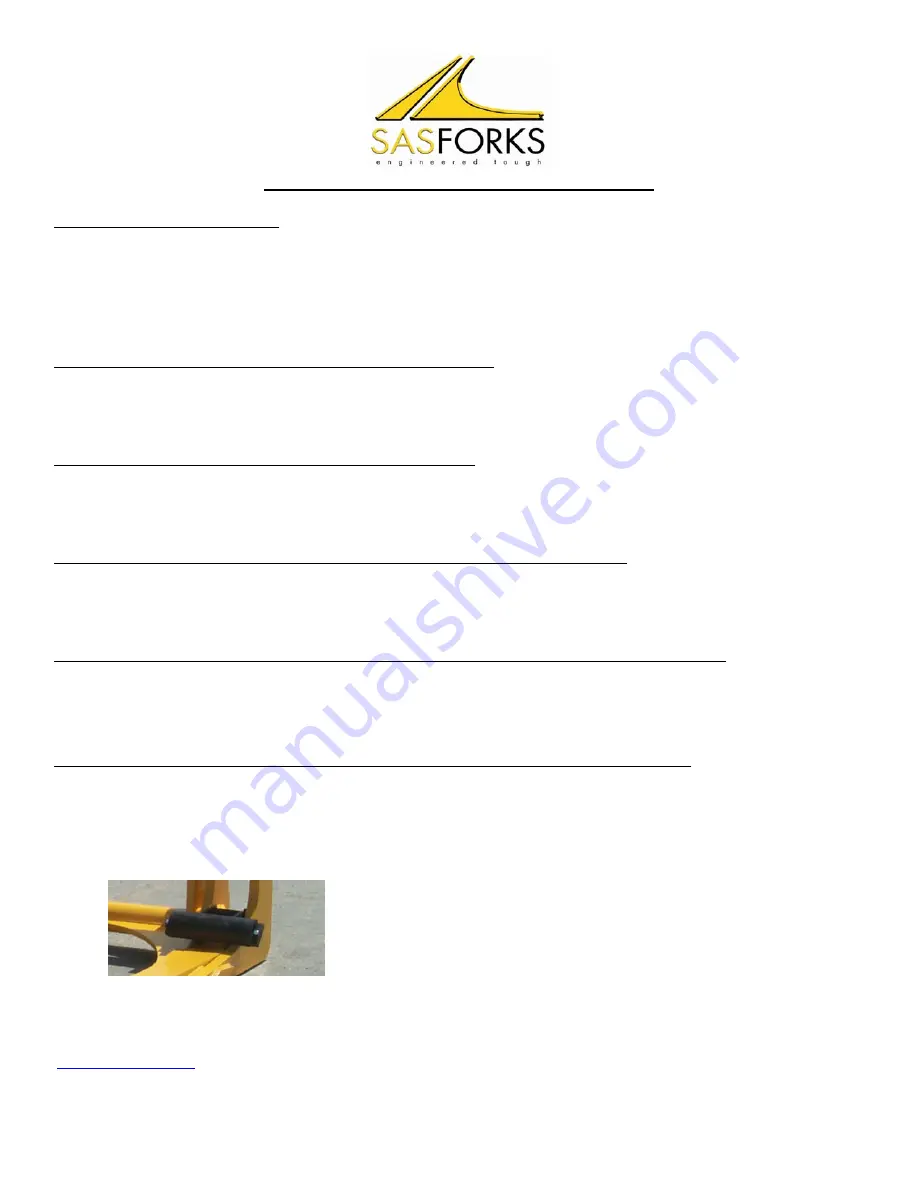
DAILY PRE-OPERATION INSPECTION
Daily, pre-operation inspection is recommended to help the operator safely use SAS FORKS™. The list below
is a general summary. This is not meant to be an exhaustive list of items to inspect. Refer to the machine
manufacturer’s operator manual for additional items that may need to be inspected prior to machine operation.
It is the responsibility of the Owners and Operators to ensure safe operation of equipment in the field. Any
unsafe items should be professionally repaired prior to operation of machine. This pre-operation inspection
should be done on level ground, with the parking brake on.
1) CHECK YOUR HYDRAULIC FITTINGS AND HOSES.
Inspect each hydraulic fitting & hose to ensure it is not worn, kinked, cracked, swelling, or leaking.
Have any damaged part(s) replaced immediately.
Do not operate the machine if damage is found.
2) GREASE AND INSPECT ALL THE LINKAGE PINS.
Inspect each linkage pin to ensure properly fastened and the condition.
Grease each linkage pin and joint to ensure smooth operation and to reduce wear.
Do not operate machine if linkage pin or retaining plate of bolt is worn, loose or missing.
3) CHECK THE WELDS ATTACHING THE BLADES TO THE CARRIAGE.
There are four welds attaching each blade to the carriage (two on each side of each blade).
Each weld should be smooth with no cracks. Do not operate machine if a weld is showing any signs of
cracking. Refer to this manual for repair instructions.
4) CHECK THE SKID PLATES ON THE BOTTOM OF THE SAS FORKS™ CARRIAGE.
Please see page 4 for details
.
Replace if less than 1/8” thick.
Order replacement skid plates by calling: U.S.A. Phone: 920-845-2198 or 1-877-SAS-FORK.
5) CHECK ROCKER PANEL BUMPER PADS ON THE SAS CRUSHING FORKS.™
IF SO EQUIPPED.
Replace if severely cracked, torn or missing.
To order replacement pads call SAS Forks @ USA Phone :920-845-2307 or 1-877-SAS-FORKS
Operations/Procedures/forks/ Engine Puller Claw Operator Manual//03-PRE-OPERATION INSPECTION.doc 4/16/08
www.sasforks.com
© 2004, 1987 S.A.S. of Luxemburg, Ltd.
1-877-SAS-FORK
Page
3