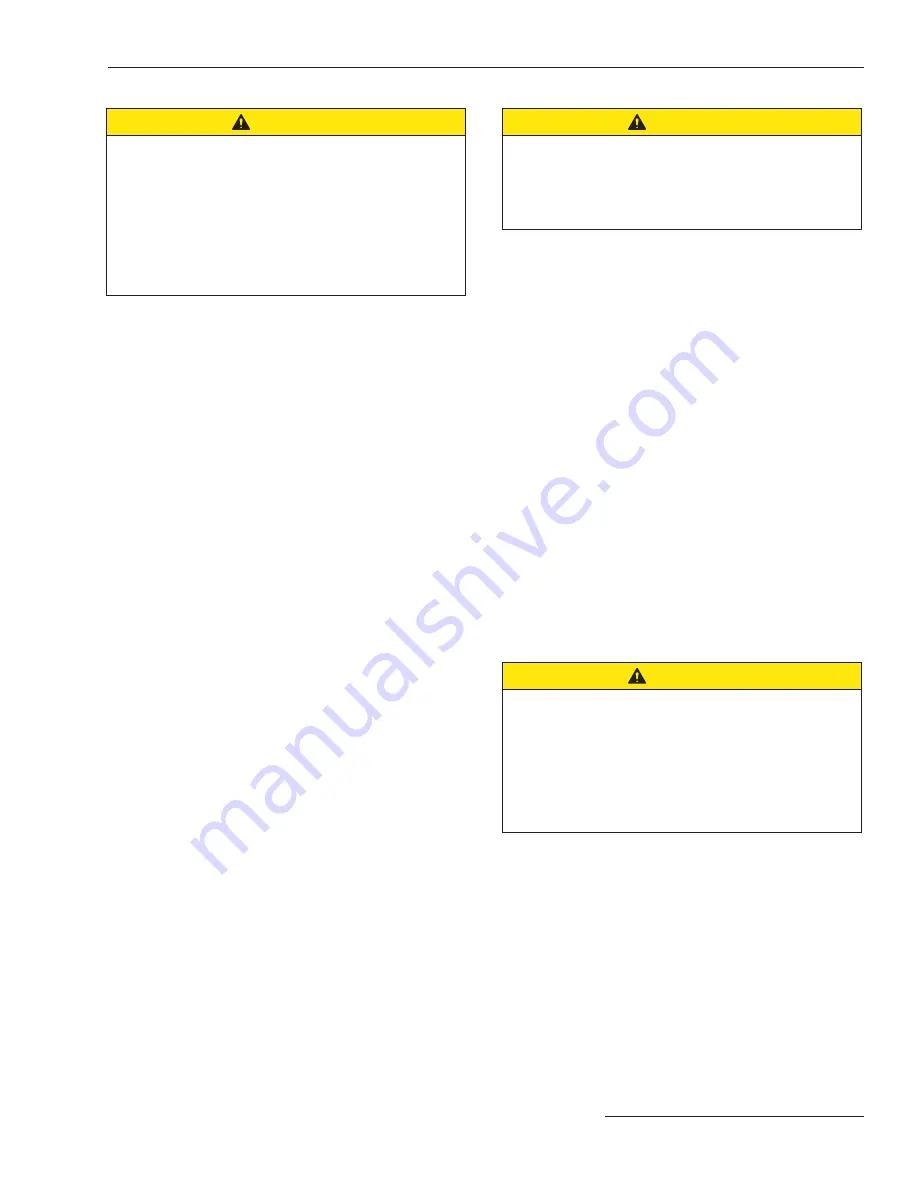
S&C Instruction Sheet 663-590
5
General
CAUTION
S&C recommends that switchgear be completely de-
energized and properly grounded according to the
user’s operating and safety procedures, and thoroughly
cleaned by hand . If it is not possible to de-energize the
gear, the use of pressure sprayed dry ice (solid CO2) is
an acceptable alternative cleaning method . The use of
pressure sprayed abrasives or solvents is specifically
not recommended because such abrasives or solvents
will damage the switchgear .
This publication contains inspection and maintenance
recommendations for Source-Transfer PMH Pad-Mounted
Gear equipped with the Micro-AT Source-Transfer Control or
the earlier vintage AT-12 Source-Transfer Control.
To successfully complete the inspection procedures involv-
ing the Micro-AT or AT-12 controls, the gear must be energized
with adequate voltage available on both power sources. It is
recommended that this inspection be performed at least every
year. Refer to Tables 1 and 2 on pages 6 and 8.
S&C generally recommends that the pad-mounted gear
enclosure and the components located in high-voltage com-
partments be inspected six months to a year after installa-
tion and then every five years thereafter to ensure continued
proper performance of the gear. Each user’s own experience
as well as environmental conditions at the installation will
determine whether more or less frequent inspections are
required. Refer to Table 3 on page 10.
A partial visual inspection of the gear for general cleanli-
ness and to confirm the proper alignment and condition of
the barriers and terminators may be performed with the gear
energized, if permitted by the user’s own operating practices
and provided standard precautionary practices are followed.
Such visual inspections may be performed for other reasons as
well. However, the more detailed inspection and maintenance
procedures outlined in this publication may only be completed
when the unit is completely de-energized and grounded.
If maintenance is required beyond the scope of this pub-
lication, or if replacement parts are necessary, contact the
nearest S&C Sales Office. Have the complete catalog number
of the gear and date of shipment (as shown on the nameplate)
available for reference.
Micro-AT Source-Transfer Control
Units of source-transfer pad-mounted gear shipped as of July
1992 are equipped with the Micro-AT control. This control
uses an electronic microprocessor to perform specific
control operations, as directed by settings programmed into
the control at the factory and in the field. These settings are
entered into the control by means of a keypad on the front
panel, and may be reviewed via a liquid-crystal display.
CAUTION
When following the inspection procedures involving the
Micro-AT control, decouple both switch operators from
their associated Mini-Rupter® Switches . Switching
operations will result in temporary service interruptions
if the operators are coupled .
Refer to S&C Instruction Sheet 663-503, “S&C Source-
Transfer PMH Pad-Mounted Gear:
With Micro-AT® Control
”
for operating instructions regarding barriers, fusing, and
switching—as well as for instructions on decoupling the
switch operators from the Mini-Rupter Switches. For field pro-
gramming and operation of the Micro-AT control, refer to S&C
Instruction sheet 515-500, “S&C Micro-AT Source-Transfer
Controls:
Field Programming and Operation
.” For instruc-
tions regarding operation of the optional test-panel feature
(catalog number suffix “-Y5”), refer to S&C Instruction Sheet
515-505, “S&C Micro-AT® Source-Transfer Controls:
Instruc-
tions for Operation of Test Panel
.” For Micro-AT control
troubleshooting, refer to S&C Instruction Sheet 515-520, “S&C
Micro-AT Source-Transfer Controls:
Troubleshooting Guide
.”
Applicable instruction sheets, drawings, and wiring dia-
grams are in an envelope entitled, “Installation and Operation
Information Kit,” which should be located in Compartment 1.
AT-12 Source-Transfer Control
Units of source-transfer pad-mounted gear shipped before
July 1992 were equipped with the AT-12 control. Operating
parameters are set in the field using selector switches and
adjustment dials located on the programming panel of the
control.
CAUTION
When following the inspection procedures involving the
AT-12 control, decouple both switch operators from their
associated Mini-Rupter Switches . If the pad-mounted
gear to be inspected is not furnished with the decou-
pling feature, the inspection procedures can still be
followed, but exercising the operators will result in live
switching and momentary interruptions of service to the
load .
For operating instructions regarding the source-transfer
pad-mounted gear (including the AT-12 control), refer to S&C
Instruction Sheet 663-501, “S&C Pad-Mounted Gear Power-
Operated PMH Models:
With Directly Operable Accessible
Components
” or S&C Instruction Sheet 663-502, “S&C Pad-
Mounted Gear Power-Operated PMH Models:
For Automatic
Source-Transfer, Models with “R4” Supplement to the
Catalog Number
,” as appropriate. For AT-12 troubleshooting,
refer to S&C Instruction Sheet 514-520, “S&C Type AT Source-
Transfer Controls:
Troubleshooting Guide
.”
Applicable instruction sheets, drawings, and wiring dia-
grams are in an envelope entitled “Installation and Operation
Information Kit,” located in Compartment 1.