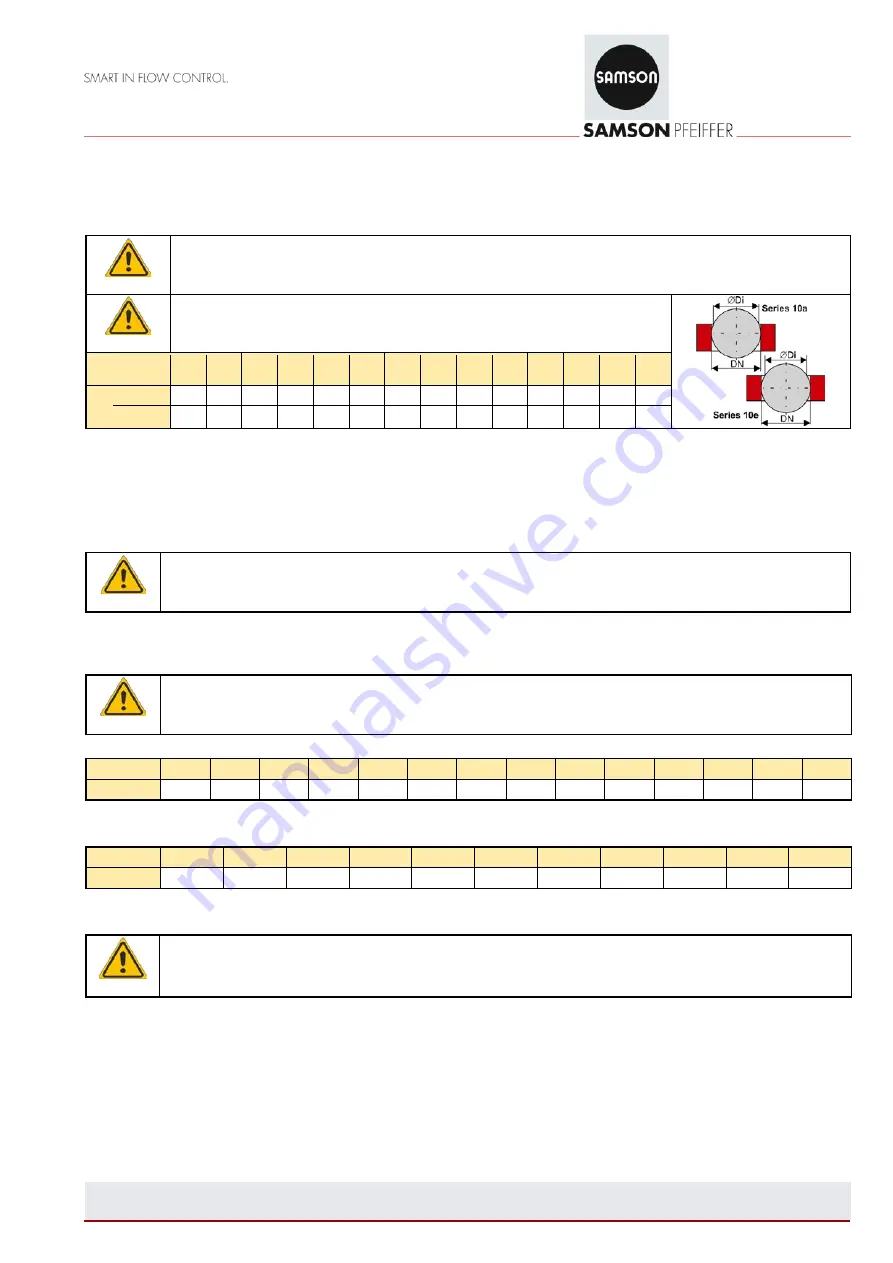
7 of 9
Specifications subject without notice
Edition: November 2017
Operating instructions BA 10a-02_EN
Prior to installation, carefully clean the valve and the connecting section of the pipeline from dirt, especially hard foreign
material.
Make sure, in particular, that flange facings and any flange gaskets used are free from any dirt prior to installation.
Note
The valve must be inserted in the gap between the pipe flanges with the butterfly disc in the closed position.
Otherwise, the butterfly disc could be damaged and the valve will not shut tightly.
Note
The inside diameter of the mating flanges must leave sufficient room for the
opened butterfly disc to ensure that it cannot be damaged on swinging out. See
Table 2.
DN
50
65
80
100 125 150 200 250 300 350 400 500 600 800
Di
BR10a
-
-
-
76,5
-
126 175 222 274 326 366 465 573 763
BR10e
45
45
62
86
116 140 187 238 282
-
390
-
-
-
Table 2 - Minimum required inside diameter of the mating flanges
The process medium can flow through the valve in either direction. The preferable mounting position for shut-off butterfly
valves is with a shaft in a horizontal position. However, if possible, the gear should not be located directly underneath the
shut-off butterfly valve.
Make sure the arrow on the valve body corresponds with the direction of flow in the pipeline.
Note
In special cases, it may be necessary for the valve to be tightly shut against the direction of flow. The installation
in such special cases must be determined by the operator of the pipeline (e.g. to protect a pump).
On inserting the valve (and flange gaskets) into a ready mounted pipeline, keep a certain clearance between the pipeline
ends to ensure that all facings (and gaskets) remain undamaged.
Caution
Tighten the flange bolts evenly and in a criss-cross pattern in at least three steps. Tighten all flange bolts using the
torques specified in Tables 2 or 3.
Use a torque wrench to ensure that the torque specified is reached, yet not exceeded.
DN [mm]
50
65
80
100
125
150
200
250
300
350
400
500
600
800
MA [Nm]
45
45
65
75
55
140
170
140
170
170
240
240
310
480
Table 3 – Flange torques for DIN-Flanges
DN [Zoll]
3“
4“
6“
8“
10“
12“
14“
16“
20“
24“
32“
MA [Nm]
65
50
100
150
140
160
160
230
240
300
470
Table 4 – Flange torques for ANSI-Flanges
Warning
Since PTFE plastic facings have a tendency to creep, we strongly recommend after installation to retighten the
bolted joint of the valve body using the tightening torques in Table 2 if the valves have been in storage for a long
time.
5. Pressure check in pipeline section
The pressure check of valves has already been carried out by the manufacturer. To check the pressure of a section of pipeline
with installed valves, the following points must be observed: