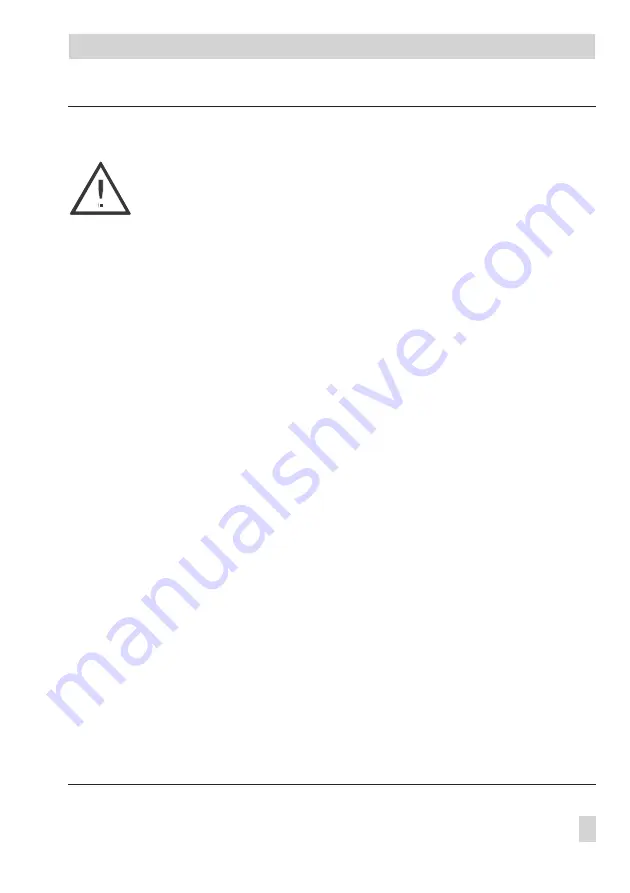
EB 8093 EN
3
Safety instructions
General safety instructions
4
The control valve may only be mounted, started up or serviced by fully
trained and qualified personnel, observing the accepted industry codes and
practices. Make sure employees or third persons are not exposed to any
danger. All safety instructions and warnings in these mounting and
operating instructions, particularly those concerning assembly, start-up and
maintenance, must be observed.
4
The control valves fulfill the requirements of the European Pressure
Equipment Directive 97/23/EC. Valves with a CE marking have a
declaration of conformity that includes information about the applied
conformity assessment procedure.
The corresponding declaration of conformity can be viewed and
downloaded on the Internet at http://www.samson.de.
4
For appropriate operation, make sure that the control valve is only used in
areas where the operating pressure and temperatures do not exceed the
operating values which are based on the valve sizing data submitted in the
order. The manufacturer does not assume any responsibility for damage
caused by external forces or any other external influence!
4
Any hazards which could be caused in the control valve by the process
medium, operating pressure, signal pressure or by moving parts are to be
prevented by means of the appropriate measures.
4
Proper shipping and appropriate storage of the control valve are assumed.
Caution!
4
For installation and maintenance work on the valve, make sure the relevant
section of the pipeline is depressurized and, depending on the process
medium, drained as well. If necessary, allow the control valve to cool down
or warm up to reach ambient temperature prior to starting any work on the
valve.
4
Prior to performing any work on the valve, make sure the supply air and
control signal are disconnected or blocked to prevent any hazards that
could be caused by moving parts.
4
Special care is needed for pneumatic control valves when the actuator
springs are pretensioned. These actuators are labeled correspondingly and
can also be identified by three long bolts protruding from the bottom of the
actuator. Prior to starting any work on the control valve, relieve the
compression from the pretensioned springs.
Содержание 3248-1
Страница 14: ...14 EB 8093 EN...
Страница 15: ...EB 8093 EN 15...