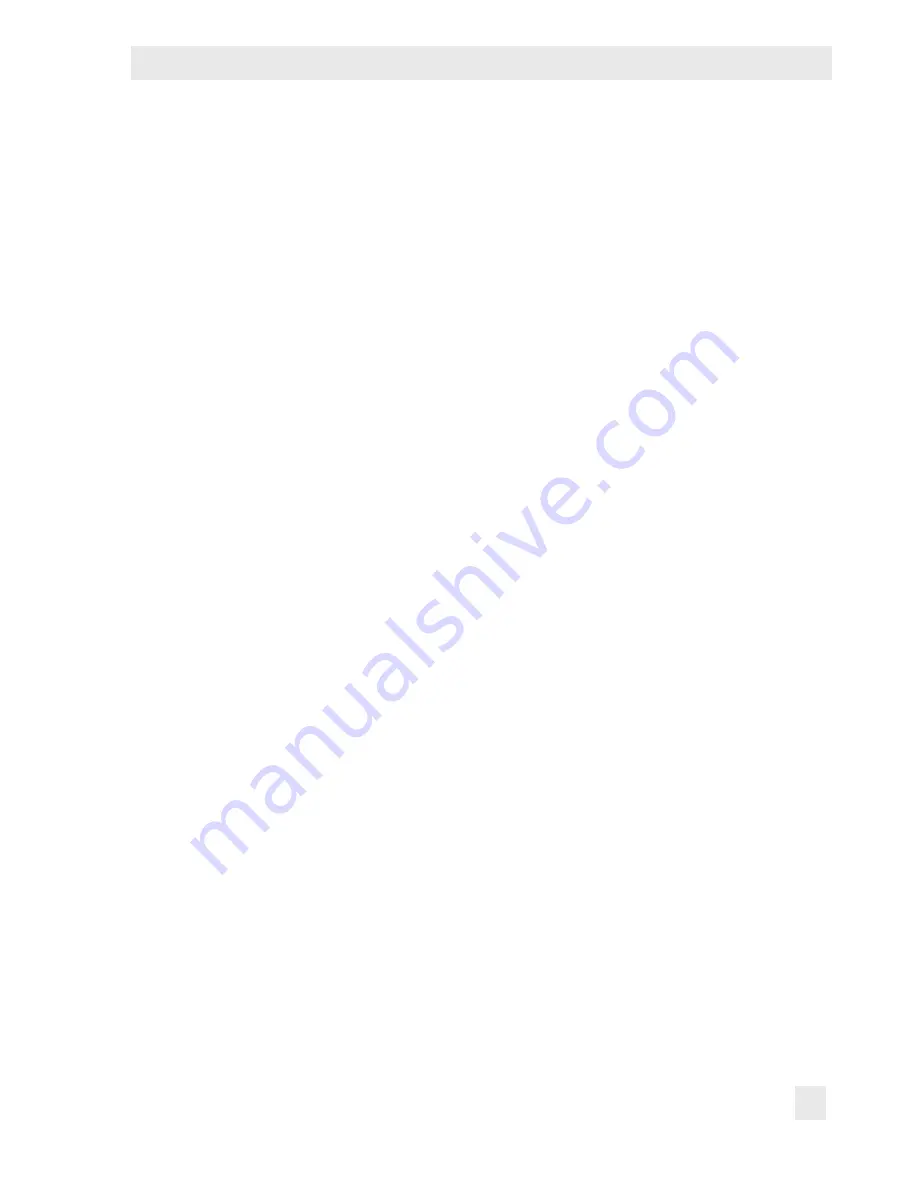
EB 2552-1 EN
11
Operation
5
Operation
See Fig. 1 and Fig. 2.
5.1
Start-up
First start up the regulator after mounting all
parts (e.g. valve and control line). Open con-
trol line with needle valve and check to ensure
it is connected correctly.
Rinsing the plant
· After filling the plant, first
completely open the consumer and adjust the
regulators to achieve the maximum flow rate.
Rinse out the pipeline at full flow rate for sev
-
eral minutes. Check the installed strainer (e.g.
by measuring the pressure drop). Clean the
strainer, if necessary.
−
Slowly
fill the plant. Make sure that the
pressure rises simultaneously upstream
and downstream of the regulator to
avoid damaging the balancing bellows/
diaphragm.
−
Open all the valves on the consum-
er side. Slowly open the shut-off valves
starting on the flow pipe side in small
steps waiting a few minutes inbetween.
5.2
Steam applications
Observe the following points for applications
with steam:
−
Before start-up, all pipes conveying the
process medium must be completely
drained and dry (to prevent steam ham-
mering).
−
Before start-up, fill the condensation
chamber (10) with water (also at the pi-
lot valve, if necessary).
−
Slowly
start up the plant and allow time
for the pipes and valves to warm up.
−
Air and condensate must be allowed to
escape from the plant. Install steam trap
(e.g. SAMSON Type 13 E) or air vent for
steam-operated systems (e.g. SAMSON
Type 3) at a suitable location.
5.3
Set point adjustment
See Fig. 1 and Fig. 2.
Adjust the required downstream pressure set
point while the plant (consumer) is open by
turning the set point adjuster at the pilot valve
(5).
When the adjusted downstream pressure set
point is reached, the pilot valve closes, caus-
ing the main valve to close as well.
Turn clockwise (
P
):
−
The set point pressure increases.
Turn counterclockwise (
Q
):
−
The set point pressure is reduced.
The pressure gauge located on the down-
stream pressure side allows the adjusted set
point to be monitored.
First set the minimum set point by turning the
set point adjuster counterclockwise (
Q
).
Wait until the pressure reducing valve starts
to regulate before adjusting the set point by
slowly turning the adjuster clockwise (
P
).
Содержание 2333 series
Страница 23: ......