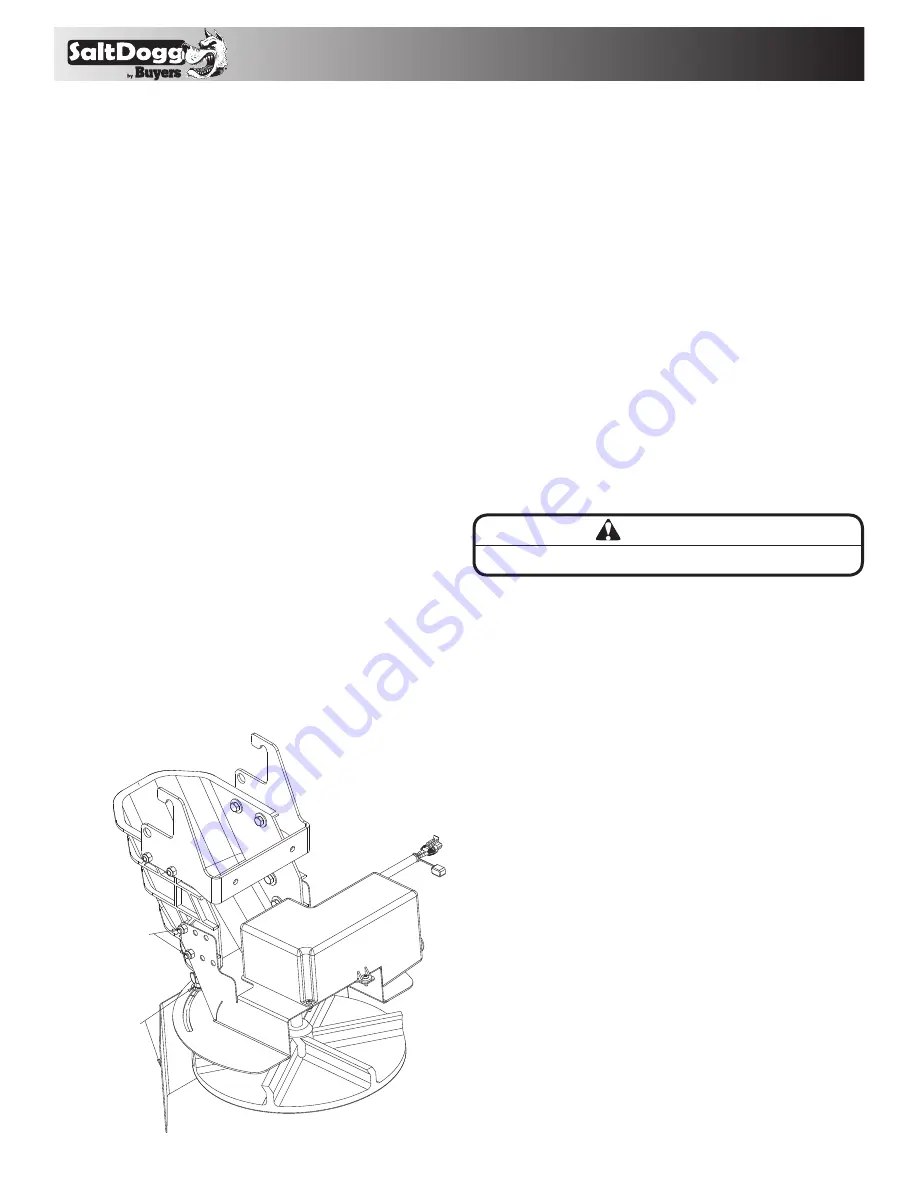
5
Fig. 8
Material Flow Adjustments
Always use screen during spreader operation!
Various materials have different moisture absorption rate,
some materials may not perform as desired. Therefore, the
substitution of the alternate material may be necessary for
optimum performance.
SHPE2000 has two discharge openings in the bottom of the
hopper. Material flow through these openings can be controlled
using two sliding baffles. The spreader is shipped from the
factory with baffles adjusted for dry bagged salt. In this setting
rear baffle has 4.0" opening and baffle in the middle of the
hopper has 2.0" opening. However if you are using a sand/
salt mixture or any chunky and hard to flow materials. Adjust
the rear baffle opening to 3" and the baffle in the middle of the
hopper to a 1" opening.
IMPORTANT! -Always open rear (closer to gear motor
compartment) opening first. Always turn off power before
adjusting baffles!
Spread Pattern Adjustment.
Spread pattern can be adjusted by changing spinner disc speed
on controller by turning Spinner knob to desired speed level
from 1 (low) to 9 (high). Direction of material spread can also be
adjusted by rotating shield on chute assembly. To rotate shield
lose 2 wing nuts, rotate shield in desired direction, and retighten
wing nuts. See Fig.8. Make sure that after adjustment, bracket
stays inside shield groove located on top of shield. In addition,
chute assembly can be adjusted to lighter (drier) and heavier
(more moist) materials. Use different holes on bracket for lighter
or heavier materials to have material drop on spinner disc
center. See Fig.8.
Spreader Maintenance
1.
Wash spreader after every use. Make sure no material is left
under auger and/or inside trough.
2.
Inspect and retighten fasteners after every 5-7 hours of
operation.
3.
Lubricate bearing every 7-10 hours of operation using
general automotive grease.
4.
Inspect terminals/connectors every time you disconnect
spreader from wire harness. Apply thin layer of dielectric grease
on terminals. If any tarnish/corrosion is found, clean terminals
and apply dielectric grease.
5.
Use dielectric grease on all electrical connectors before an
electrical connection is made or after connector is disconnected
6.
Grease and spray with lubricant Auger bearing after every 20
hours of use.
7.
Empty the spreader of all ice control materials when not in
use. Wash out the spreader to prevent material builds up.
8.
It is recommended to cover spreader with the tarp during
storage periods.
LOOSE WING NUTS
ROTATE SHIELD
HOLES FOR BRACKET
POSITION ADJUSTMENT
WARNING
Never remove spreader with material in hopper.
End of Season Maintenance
1.
Wash spreader. Make sure no material or residue is left in and
outside the hopper.
2.
Lubricate bearing using general automotive grease.
3.
Inspect wire harness, connectors for broken insulation, missing
components. Replace if necessary.
4.
Apply dielectric grease on all electrical connectors.
5.
Store hopper indoors, in a dry, cool place.
6.
Remove controller from truck. Store controller indoors, in a dry,
cool place.
7.
Inspect wire near connectors. Check for broken or missing
insulation. Check for tarnished or corroded wires. Trim corroded
wires and replace connectors if necessary.
Summer Storage
1.
Apply dielectric grease or similar protective compound on all
electrical connectors & protect them with caps before storage.
2.
Disconnect and remove speed controller from vehicle and
store it in dry and cool place. Protect controller from excessive
heat and moisture.
3.
Clean hopper and trough from all kinds of debris.
4.
Remove, thoroughly lubricate and reinstall trough bearing.
5.
Protect hopper from excessive temperatures during
summer storage.