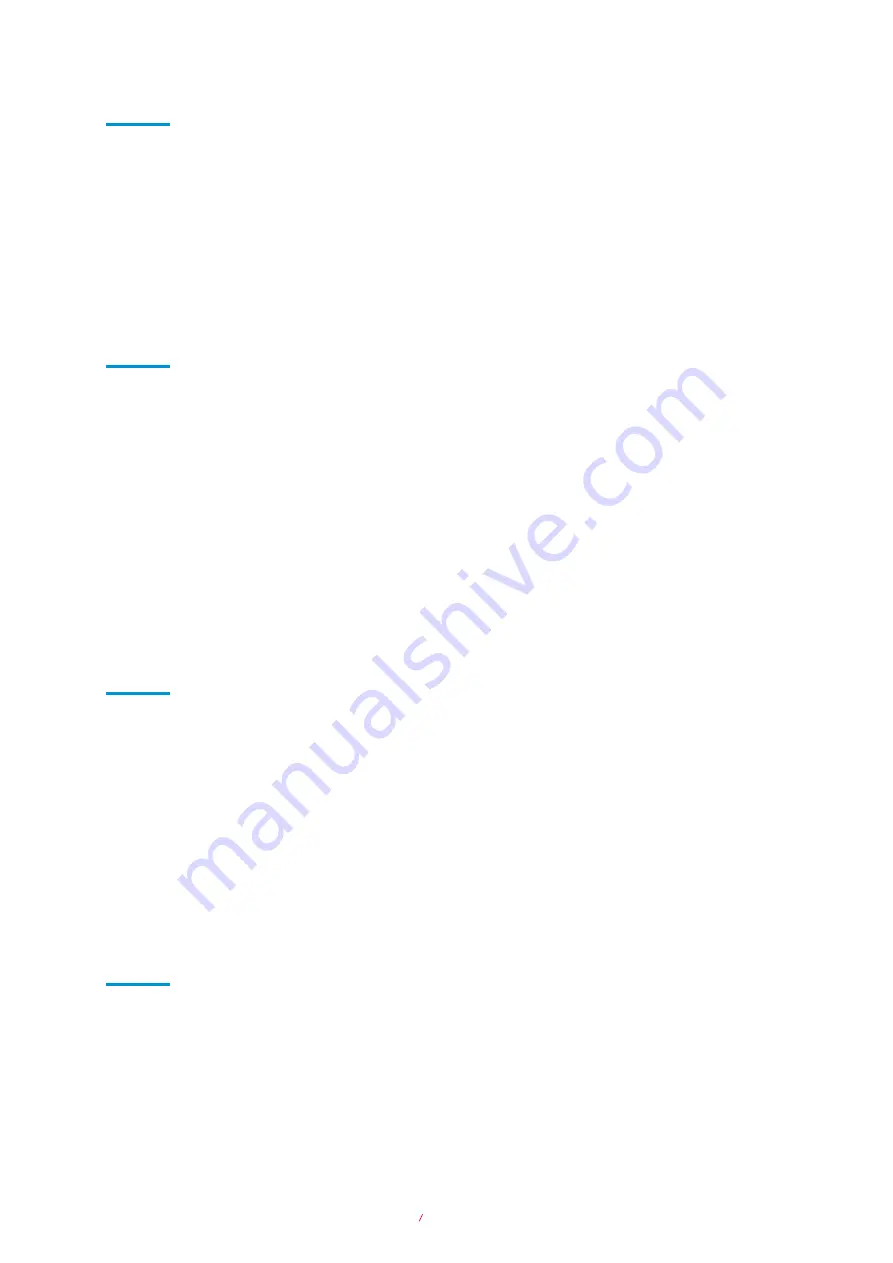
VISION-LITE® / VISION-LITE II®
PROCESSING GUIDELINES
MAY 2022
17
Once again, the cleanliness of VISION-LITE® II coating before entering the enamelling process is
important.
VISION-LITE® II may be fully or partially enamelled using screen printing technique. Given the variety of
enamelling products, different operations and practical experiences, each processor should carry out
tests with its own equipment. It is processor responsibility to validate enamel material compatibility with
the layer and its adherence must be previously checked.
It is recommended that any offer for the possible supply of enameled VISION-LITE® II be subject to
previous acceptance by the client of samples produced in the operation concerned.
Only enamel without lead content may be applied.
Following toughening / heat-soaking or heat-strengthening, each pane should be separated with pads.
It is also possible to stack the individual panes with strips of 2 mm thick polyethylene – stretch – foam
film (in that case, particular care should be taken when stacking different glass dimensions).
•
Glass panes must be stored vertically (at 3 to 7 degrees) under the following conditions:
• In a dry, well ventilated store, to prevent any condensation on the surface;
• Protected from rain and running water (any roof leaks must be rectified);
• Never outside or in the open air;
• Protected from wide changes in temperature and humidity levels (store coated glass products
far from opening doors).
•
Clean, dry and soft gloves must be worn for all handling.
•
In case heat-treated VISION-LITE® II is assembled into double-glazed units, this should be performed
within 2 days.
SEMI VISION-LITE® for annealed laminated glass or tempered SEMI VISION-LITE® II only can be laminated
with the coating outside the sandwich. It means that the lamination is always carried out on the glass
(uncoated) side. Never have the anti-reflective coating on the interlayer side.
•
To assemble the glass, ensure that the calendaring rollers are in good condition (clean and no
particles of glass). Check that the circumferential speed is regular and corresponds to that of the
conveyor system. Clean off all deposits of PVB in contact with the coating before placing in the
furnaces or autoclaves.
•
Apply the standard autoclaving cycles. Use dry spacers (example: wood) or protected spacers.
•
When laminating heat treated SEMI VISION-LITE® II, it is important to take care that the PVB
thickness is adapted as to compensate the possible glass deformation (roller wave, bow, edge lift)
created during the heat-treatment process. Contact your local TSM if necessary.
3.9. ENAMELLING
3.10. HANDLING OF HEAT-TREATED GLASS
3.11. LAMINATION
It is recommended to assemble the panes in insulating glass units as quickly as possible. When
manufacturing double-glazed units using VISION-LITE® range, please follow the handling, cutting, and
washing instructions detailed above.
Important focus on drying marks and possible unwashed residues must be done. Indeed, all traces will
be more visible on antireflective coating than standard float glass.
Good efficiency of the washing and
drying at IGU line should be controlled regularly.
The coated glass must be washed before making it into insulating glass units. Recommended washing
3.12. MANUFACTURE OF INSULATING GLASS UNITS